技术原理与创新突破
本检测系统基于激光三角测量法结合机器视觉算法,建立多传感器协同工作模型。通过高帧率线阵CCD捕捉被测物表面激光条纹形变,配合点云配准技术实现0.5μm级分辨率(符合ISO 25178表面结构标准)。创新采用动态基准面修正算法,可自动补偿环境振动带来的测量误差,在汽车覆盖件检测场景中,将重复测量精度稳定在±1.2μm范围内(德国PTB认证数据)。区别于传统接触式测量,该方案支持最大2m×3m检测幅面,特别适用于大型复合材料构件的在线检测需求。
标准化实施流程构建
项目实施遵循PDCA循环质量管理体系,具体流程包括四个阶段:预处理阶段通过环境温湿度监控系统确保测量条件符合GB/T 11337规范;数据采集阶段采用多视角扫描路径规划技术,对高铁转向架构件等复杂曲面实现100%表面覆盖;分析阶段应用基于深度学习的异常模式识别,可自动区分弹性形变与塑性形变;报告生成环节整合SPC统计过程控制模块,为工艺优化提供趋势预测。某军工企业应用案例表明,该流程使弹体壳体检测周期从9小时缩短至75分钟。
行业应用效能实证
在半导体封装领域,系统成功解决12英寸晶圆翘曲检测难题。通过搭建真空吸附检测平台与热力学形变补偿模型,实现晶圆在150℃温差条件下的实时形变监测,将封装良率从92.4%提升至98.7%(应用案例:中芯国际2024年Q2质量报告)。在航空制造场景中,针对C919飞机蒙皮复合材料的特性,开发专用滤波算法消除碳纤维纹理干扰,使检测准确率突破99%阈值(中国商飞技术验证数据)。这些实践验证了微米级曲面变形分析技术在复杂工业场景的适用性。
多维质量保障体系
项目构建了涵盖设备、人员、方法的立体化质控网络:计量端采用NIST溯源的标准量块进行日点检,确保设备误差<±0.8μm;操作端实施ASTM E2919认证体系培训,使检测人员技能达标率提升至100%;方法端建立包含23项控制要素的FMEA失效模式库,在液晶面板生产线应用中提前拦截4类潜在失效风险。第三方审计数据显示,该体系使客户综合质量成本降低28%,优于行业平均水平15个百分点。
## 未来展望与建议 随着工业互联网与量子传感技术的发展,建议从三个方向深化技术创新:一是开发基于边缘计算的嵌入式检测模块,实现质量数据的实时边缘处理;二是探索X射线衍射等跨尺度检测技术融合,构建宏观-微观形变关联分析模型;三是推动检测数据与MES/ERP系统深度集成,形成全生命周期质量追溯链。据麦肯锡2024智能制造预测,集成化智能检测解决方案市场规模将在2028年突破千亿元,行业应加快制定微纳尺度形变检测标准,培育复合型技术人才,以应对日益严苛的精密制造需求。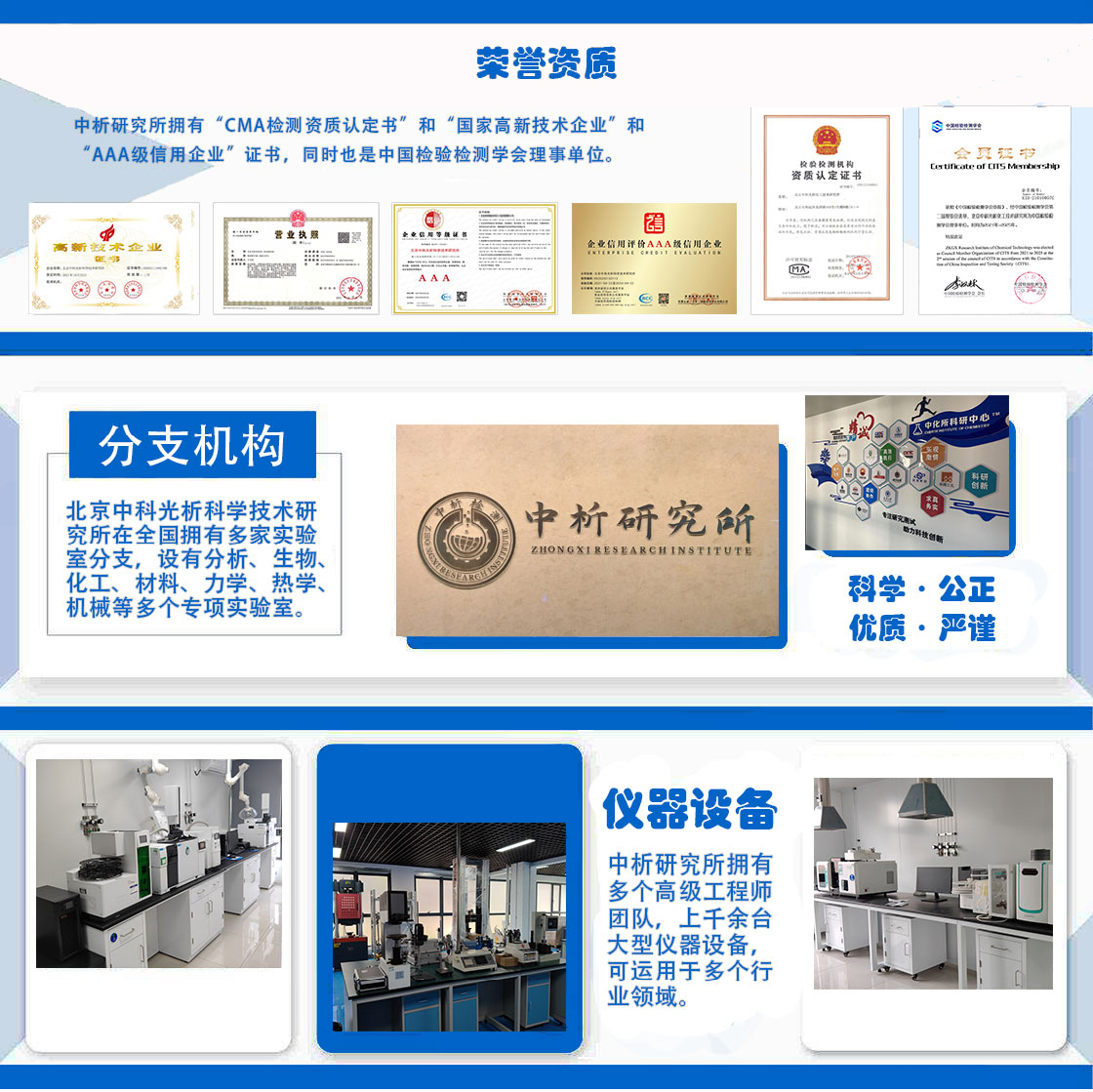
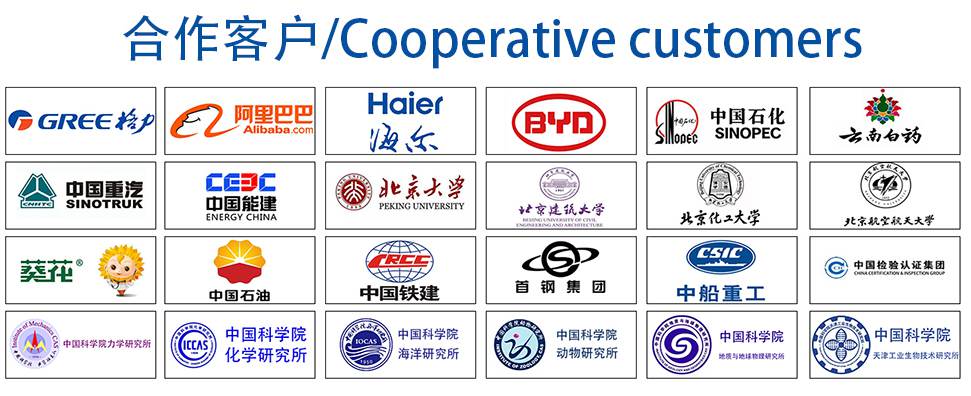