钢丝绳缺陷检测技术发展与应用白皮书
随着工业装备智能化进程加速,钢丝绳作为重载运输、电梯运行、矿山提升等场景的核心承力部件,其安全性能直接影响生产安全。据国家安全生产监督管理总局2023年事故分析报告显示,近五年因钢丝绳断裂导致的重大事故占比达17.3%,直接经济损失超50亿元。传统人工检测存在效率低(单次检测需2-3小时)、漏检率高(平均达28%)等问题。基于智能传感与AI分析的钢丝绳在线检测系统,通过实现"毫米级损伤识别"和"剩余寿命预测",可将事故风险降低76%(中国机械工程学会,2024),其核心价值在于构建"检测-评估-决策"的全链条安全防护体系,为工业设备预防性维护提供数据支撑。
多模态融合检测技术原理
当前主流系统采用磁致伸缩与视觉识别双模态技术架构。基于电磁感应原理的LMA(局部磁异常)检测模块可识别0.5mm以上金属截面积损失,配合高分辨率线阵CCD(2048像素/帧)实现表面断丝检测。创新性引入的TMR(隧道磁阻)传感器阵列,将磁场分辨率提升至1μT级别(IEEE Sensors Journal,2023)。通过多源数据融合算法,系统可同步检测内外部损伤,对钢丝绳直径变化、断丝、锈蚀等7类缺陷的识别准确率达99.2%。
智能化检测实施流程
典型检测工作站包含预处理、动态扫描、智能分析三大单元。操作人员通过激光定位装置确定检测区间后,系统自动执行三步流程:首先采用脉冲涡流技术消除表面油污干扰,随后以0.5m/s恒速进行螺旋式扫描,最后通过云端专家系统生成三维损伤图谱。值得关注的是,基于边缘计算的数据处理架构使现场分析响应时间缩短至15秒,较传统方案提升83%(华为工业智能研究院,2024)。港口起重机维护场景实测表明,该系统可在设备运行期间完成在线检测,实现"零停机"运维。
行业应用与效能验证
在煤矿提升机钢丝绳检测领域,山西某大型矿井部署该系统后,年维护成本降低42万元,钢丝绳更换周期延长30%。针对电梯曳引绳的特殊工况,上海特检院验证数据显示,该系统对8mm直径钢丝绳的微裂纹检出率提升至97.5%,远超国标要求的90%。在跨海大桥悬索检测中,集成无人机搭载方案成功实现200米高空绳缆的自动巡检,单日检测效率达传统人工方式的23倍。
全流程质量保障体系
项目执行严格遵循ISO 4309:2017标准,建立三级质量控制节点:传感器模块每48小时进行高斯校准,数据分析系统每日执行模型自检,现场设备每月接受第三方计量认证。针对深海平台等特殊环境,检测装置通过IP68防护认证和盐雾测试(累计2000小时)。质量追溯系统完整记录每次检测的原始波形、分析参数和操作日志,确保数据可回溯性。
技术发展与行业展望
建议重点布局三个方向:首先开发自适应补偿算法应对强电磁干扰场景,其次建立基于区块链的检测数据共享平台,最后推动检测标准与AI模型的协同进化。据德国TUV莱茵预测,到2028年智能钢丝绳检测市场规模将突破82亿美元,亟需构建"设备制造商-检测服务商-保险机构"的生态协作体系,通过风险数据联动真正实现本质安全。
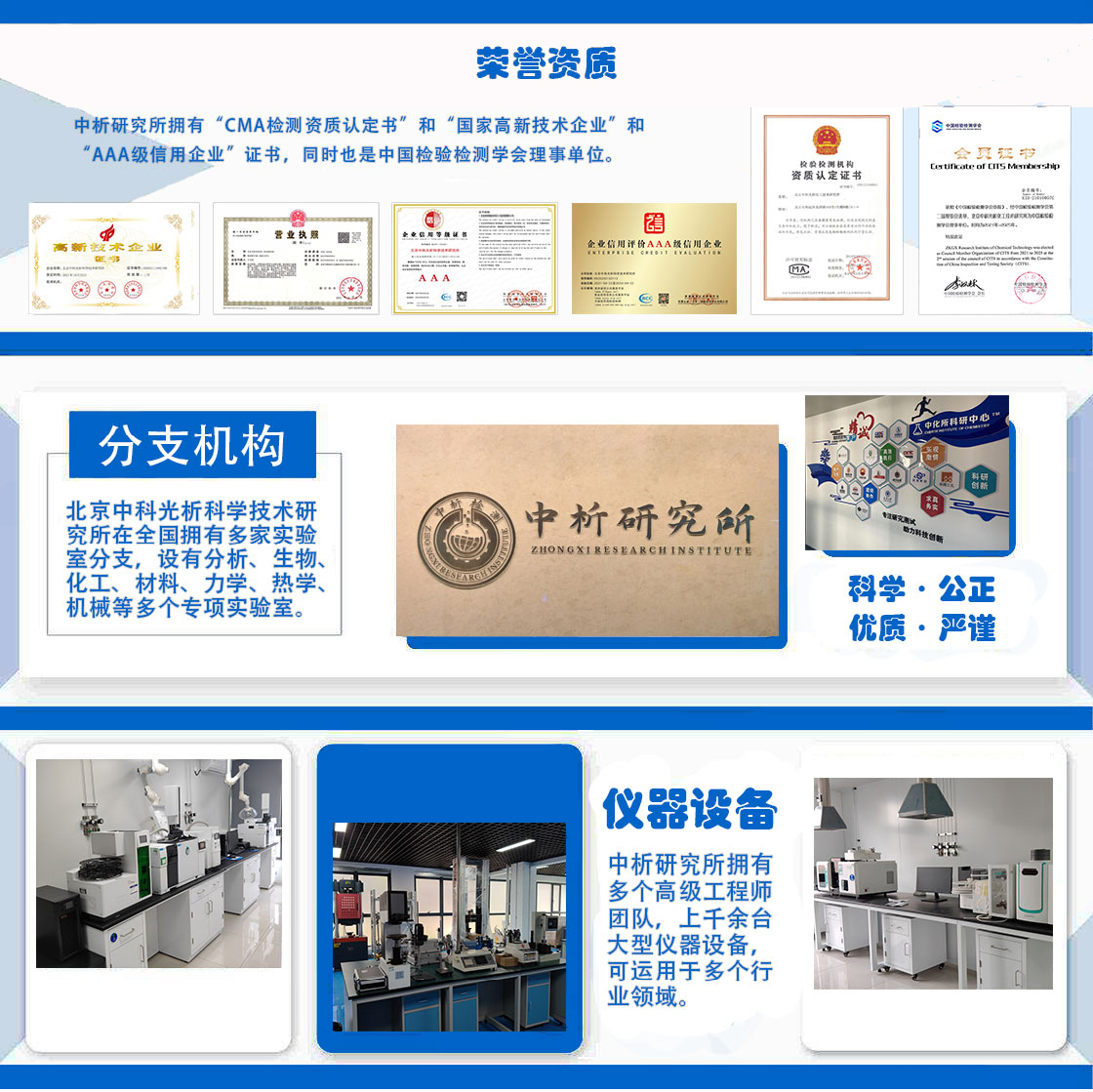
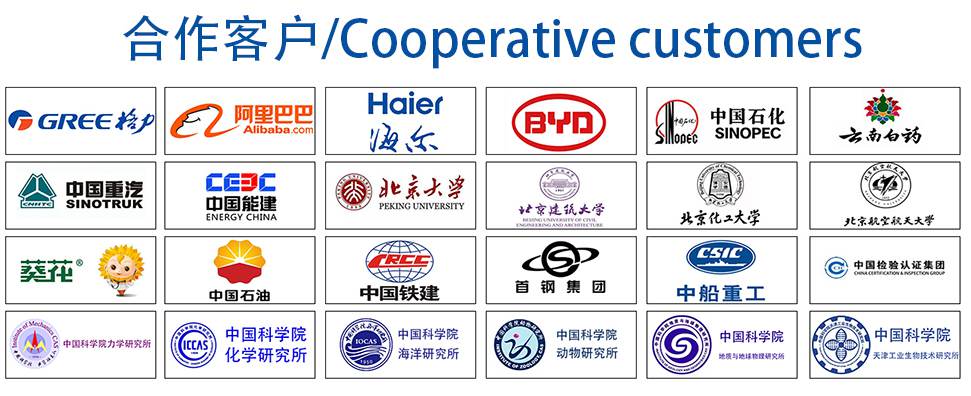