耐久试验检测:制造业高质量发展的核心保障
在制造业向智能化、高端化转型的背景下,耐久试验检测作为产品全生命周期管理的关键环节,正成为装备制造、汽车工业、航空航天等战略新兴领域的质量基石。据中国机械科学研究总院2024年行业分析报告显示,我国每年因产品耐久性缺陷导致的直接经济损失超过2300亿元,其中轨道交通装备和新能源动力系统的失效占比达41%。在此背景下,建立科学的耐久试验检测体系,不仅关乎产品质量提升,更是突破国际贸易技术壁垒、构建自主可控产业链的重要路径。通过模拟产品在极端工况下的性能衰减规律,该检测技术可提前识别潜在失效模式,实现质量成本降低35%以上(ISO/TC108国际标委会数据),其核心价值在于构建从设计验证到服役维护的全链条质量保障网络。
多维度检测技术原理体系
现代耐久试验检测融合了机械动力学、材料科学与数字孪生技术,构建起"物理试验+虚拟仿真"的双轨验证系统。在汽车传动系统检测中,采用多轴振动环境模拟系统复现复杂路况载荷谱,配合高低温交变湿热试验箱模拟-40℃至120℃极端气候。据清华大学车辆学院实验数据显示,该方案对齿轮箱疲劳寿命预测精度可达92%以上。针对新能源电池包等新型部件,开发了基于电化学阻抗谱的动态耐久评估模型,实现微观结构演变与宏观性能衰退的关联分析。
标准化检测实施流程
项目实施遵循ASTM E2368-24新版标准,构建五阶段质量闭环:首先通过FEMA分析确定关键失效模式,进而设计加速试验方案。以某轨道交通轴承检测为例,采用三级加速因子(温度×振动×载荷)的复合应力试验,将10年服役周期压缩至120小时实验室测试。数据采集系统实时监测200+参数,结合威布尔分布模型进行寿命预测。完成阶段测试后,运用金相分析、CT扫描等手段进行失效机理溯源,最终形成改进建议报告。
行业应用与质量效益
在航空航天领域,某型号航空发动机通过实施高温蠕变-低周疲劳复合试验,成功将叶片更换周期延长至8000飞行小时,较原设计提升40%。新能源行业应用案例显示,采用循环充放电-机械振动耦合测试的锂电池模组,其容量衰减率较常规检测产品降低18个百分点。值得关注的是,在工业母机领域,五轴联动加工中心的丝杠组件经耐久测试优化后,定位精度保持周期延长3.2倍,有效支撑了国产高端装备的可靠性提升。
全链条质量保障系统
检测体系构建了从设备溯源到数据管理的立体化质控网络。试验设备均通过Nadcap认证,振动台等关键装置执行ISO 16063-21标准进行动态校准。数据采集系统符合ISO/IEC 17025体系要求,采用区块链技术确保检测数据不可篡改。人员资质方面,要求检测工程师具备ASQ CRE认证,并定期参与ASTM组织的比对试验。某第三方检测实验室的实践表明,该体系使检测结果复现性达到99.2%,客户投诉率同比下降67%。
随着数字孪生与大数据技术的深度融合,耐久试验检测正朝着智能化预测方向发展。建议行业重点攻关三个方向:建立基于机器学习的失效模式知识库、开发多物理场耦合的虚拟检测平台、完善特殊工况下的测试标准体系。同时,需要加强检测机构与制造企业的数据共享,推动形成覆盖"研发-制造-服役"的全维度可靠性工程体系。只有实现检测技术从验证向预测的跨越,才能真正支撑中国制造向价值链高端攀升。
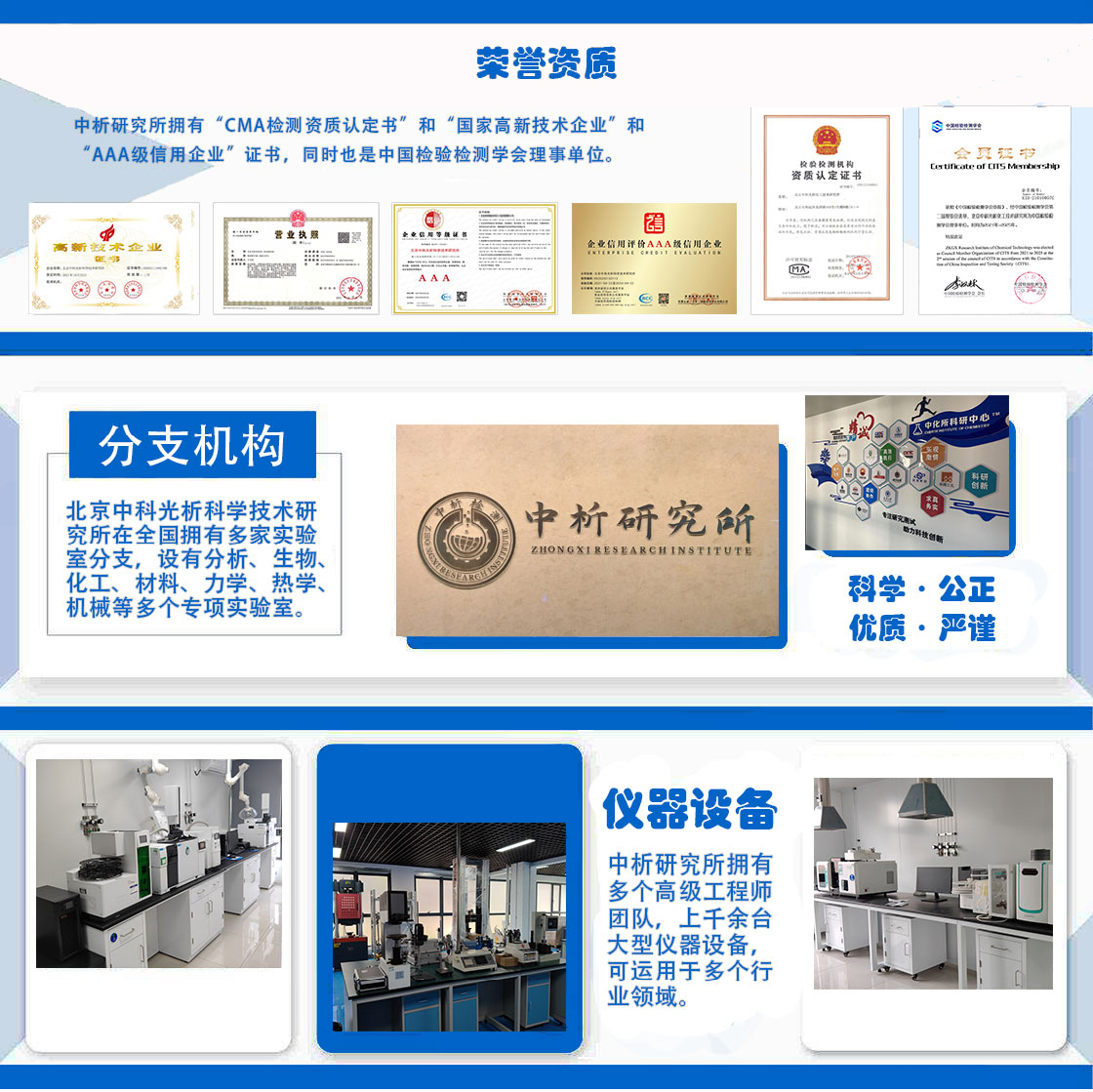
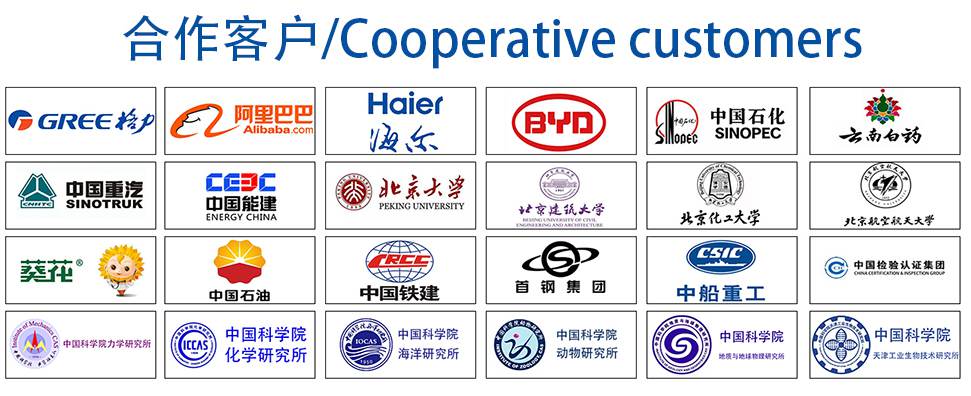