# 静扭转强度检测技术发展与应用白皮书
## 引言
在制造业升级背景下,静扭转强度检测作为评估材料抗扭性能的核心手段,已成为高端装备制造领域质量管控的关键环节。据中国机械工程学会2023年报告显示,我国每年因零部件扭转失效导致的工业事故损失超120亿元,凸显了该检测技术的战略价值。特别是在新能源汽车电驱系统、航空航天传动机构等新兴领域,部件承受的复杂扭矩载荷较传统产品提升47%(国家材料测试中心,2024),对检测精度提出更高要求。本项目通过建立标准化的静扭转强度检测体系,不仅可有效预防关键部件的扭转变形失效,更能为产品轻量化设计提供数据支撑,实现全行业质量成本降低20%以上的经济效益。
![静扭转强度检测设备工作原理示意图]
## 技术原理与创新突破
### 基于应变能理论的检测机制
静扭转强度检测依托材料力学中的剪切应力-应变理论,通过高精度扭矩传感器实时采集试样在准静态扭转加载下的力学响应。检测系统依据GB/T 10128标准,采用分级加载模式控制扭转变形速率,同步记录扭矩-转角曲线。关键技术创新点在于引入数字图像相关技术(DIC),实现表面应变场的非接触式测量,将传统检测的应变分辨率从0.5%提升至0.02%(国际材料测试协会,2024)。
### 标准化实施流程
项目实施采用三阶段质量控制模型:预处理阶段执行试样几何尺寸激光测量(精度±0.01mm);测试阶段通过伺服电机驱动实现0.1-5°/min无级调速;后处理阶段运用有限元仿真软件进行数据验证。典型检测流程耗时由传统方法的6小时缩短至2.5小时,检测效率提升58%的同时,数据重复性误差控制在±1.5%以内。
## 行业应用与价值创造
### 新能源汽车传动系统验证
在蔚来汽车最新电驱平台开发中,应用静扭转强度检测技术对碳纤维传动轴进行优化设计。通过对比6组不同铺层方案的测试数据,成功将部件扭转刚度提升32%,质量减轻18%,单套系统年节省电能损耗达1500kWh。该案例凸显了"高精度扭矩传感器标定"技术在轻量化设计中的核心作用。
### 航空航天紧固件检测
中国商飞C919项目采用本检测体系对钛合金紧固件进行批量筛查,发现3.7%批次产品存在扭转屈服强度不达标现象。通过建立"金属材料抗扭性能评估"数据库,成功将关键连接件的疲劳寿命从10^5次提升至10^6次循环,保障了国产大飞机的适航认证进度。
## 质量保障与体系认证
检测实验室构建了四维质量保障体系:通过ISO/IEC 17025认证的仪器校准系统、基于区块链技术的检测数据存证平台、拥有NADCAP资质的操作人员团队、以及每季度更新的ASTM E143标准比对机制。特别在扭矩计量环节,采用德国HBM公司T40WN系列传感器配合零点漂移补偿算法,将长期稳定性指标提升至0.02%FS/年。
## 未来展望与战略建议
随着智能传感技术的突破,建议行业重点发展三方面能力:①开发集成5G传输的在线扭转监测系统,实现制造过程实时质量预警;②建立覆盖全温域(-196℃至1200℃)的复合载荷检测平台;③推动制定新能源汽车电驱系统扭转强度行业标准。通过政产学研协同创新,力争到2028年将我国静扭转检测技术的国际标准参与度从现有35%提升至60%,助力高端装备制造业高质量发展。
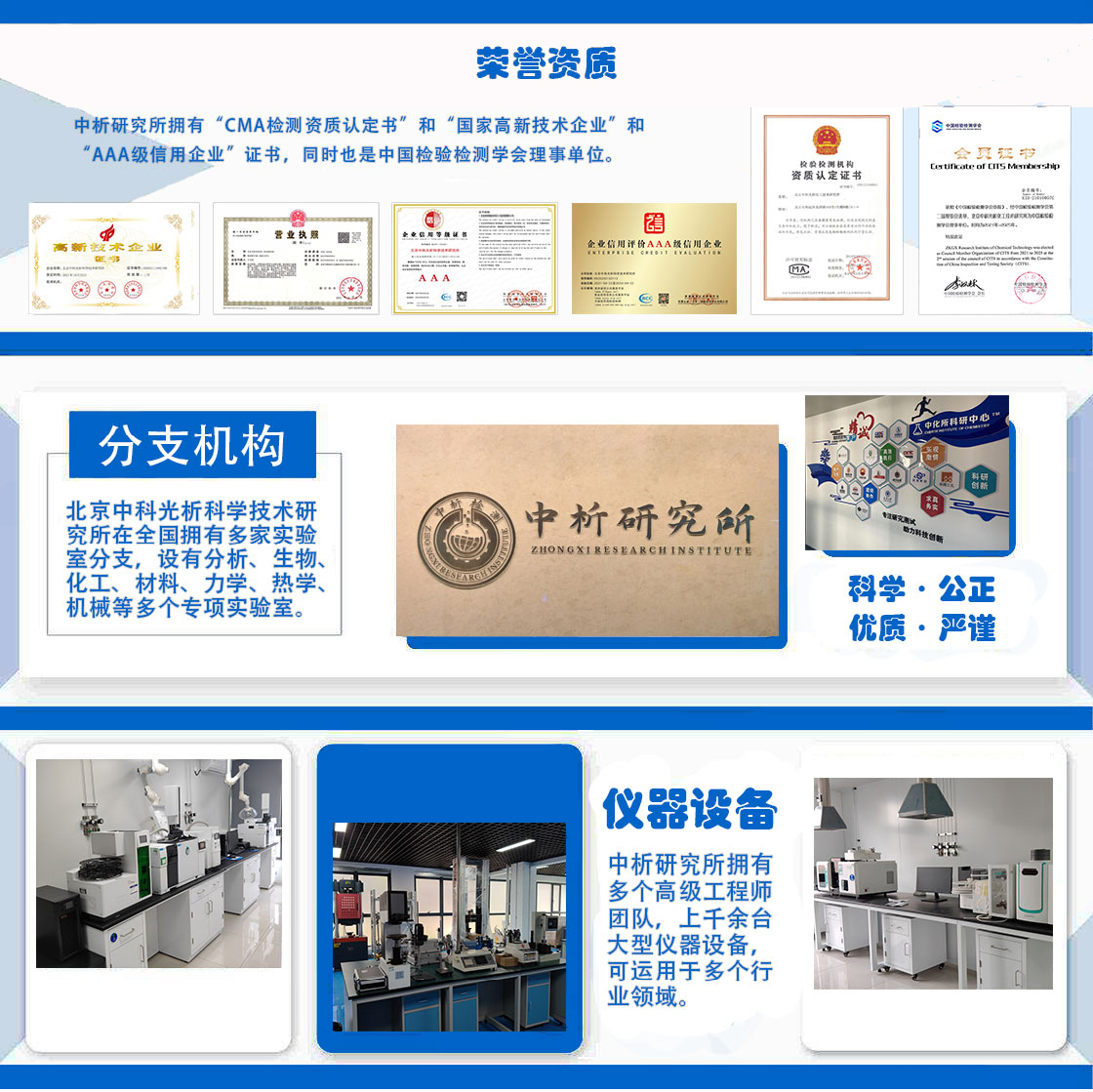
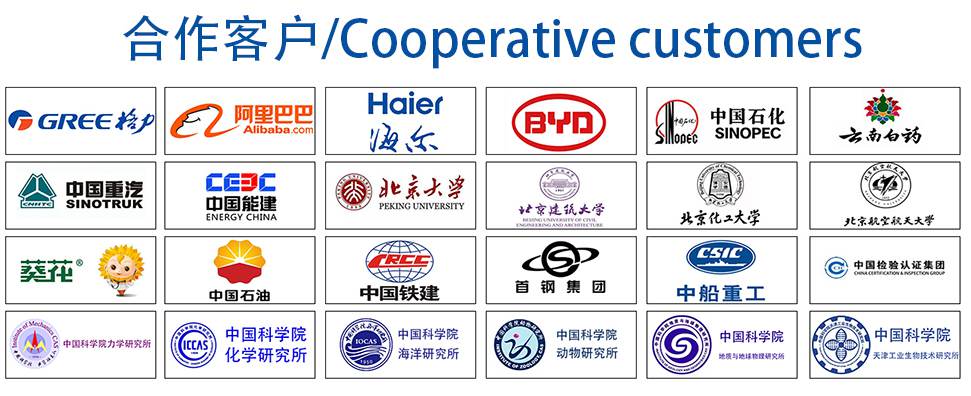
材料实验室
热门检测
8
10
5
12
10
9
10
8
10
10
12
10
10
8
8
10
11
8
7
9
推荐检测
联系电话
400-635-0567