工况循环寿命检测技术白皮书
在新能源产业高速发展的背景下,动力电池、储能系统等关键设备的可靠性验证已成为行业焦点。据中国汽车工程研究院2024年数据显示,动力电池系统故障案例中63%与循环寿命衰减相关。工况循环寿命检测通过模拟设备在实际运行中的动态载荷、温度变化及能量转换过程,建立全生命周期的性能衰减模型,其核心价值体现在降低设备早期失效风险、优化产品设计参数以及支撑设备残值评估体系构建。特别在电动汽车换电模式推广和新型储能电站建设过程中,该检测技术可为设备梯次利用提供关键数据支撑。
复合应力耦合测试原理
基于多物理场耦合仿真技术,构建包含电-热-机械应力的综合测试模型。通过可编程电源系统实现0.5C-3C倍率的动态充放电切换,配合温控箱在-40℃至85℃区间进行梯度温度冲击。值得关注的是,新一代检测设备已集成原位检测模块,可在不中断测试的前提下实时采集电极膨胀率(精度±0.1μm)和电解液消耗量(检测限0.1ml)等微观参数。这种多维度数据采集方式显著提升了循环失效机理的解析能力,为改进电池负极材料包覆工艺提供了量化依据。
标准化测试流程构建
检测实施分为预处理、基线测试、加速老化、失效分析四个阶段。预处理阶段需在25±2℃环境下完成三次完整循环以激活设备,基线测试则通过EIS(电化学阻抗谱)建立初始状态数据库。在储能系统工况模拟测试中,采用美国能源部推荐的CYC\_2023循环协议,模拟光伏电站典型的"两充两放"日循环模式。测试过程中同步记录析锂临界点、容量跳水拐点等关键参数,结合Weibull分布模型预测设备使用寿命,最终生成符合UL1974标准的检测报告。
多领域应用验证
在商用车动力电池检测领域,某头部企业通过导入动态工况测试体系,将电池包设计验证周期缩短40%。其典型案例显示,采用公交工况模拟测试(包含频繁启停、快速充电等场景)后,磷酸铁锂电池的循环寿命预测误差从±15%降低至±7%。而在储能电站检测方向,据国家能源局2024年示范项目评估报告,实施全工况循环检测的锂电储能系统,首年容量衰减率控制在3%以内,较传统检测方式提升1.8个百分点。这些实践验证了工况模拟测试在提升产品可靠性和经济效益方面的双重价值。
全链路质量保障体系
构建从设备溯源到数据管理的立体化质控网络,所有测试设备均通过 校准认证并接入国家计量院物联网平台。测试环境执行ISO17025管理体系,温控箱温度均匀性≤±1℃,数据采集系统时间分辨率达到10ms级。在动力电池工况模拟测试过程中,创新采用区块链技术实现检测数据全程上链,确保测试报告不可篡改。实验室间比对验证显示,该体系下循环寿命测试结果的再现性误差小于2.5%,完全满足GB/T 31486-2023标准要求。
展望未来,建议从三方面深化技术应用:建立细分行业的差异化测试标准体系,如针对高寒地区开发-50℃极低温循环协议;推动数字孪生技术在寿命预测中的应用,通过虚拟测试降低实物验证成本;加强检测机构与材料企业的协同创新,建立负极膨胀率-循环次数-容量衰减的跨学科关联模型。只有持续完善工况模拟检测生态,才能为新能源产业高质量发展提供坚实技术保障。
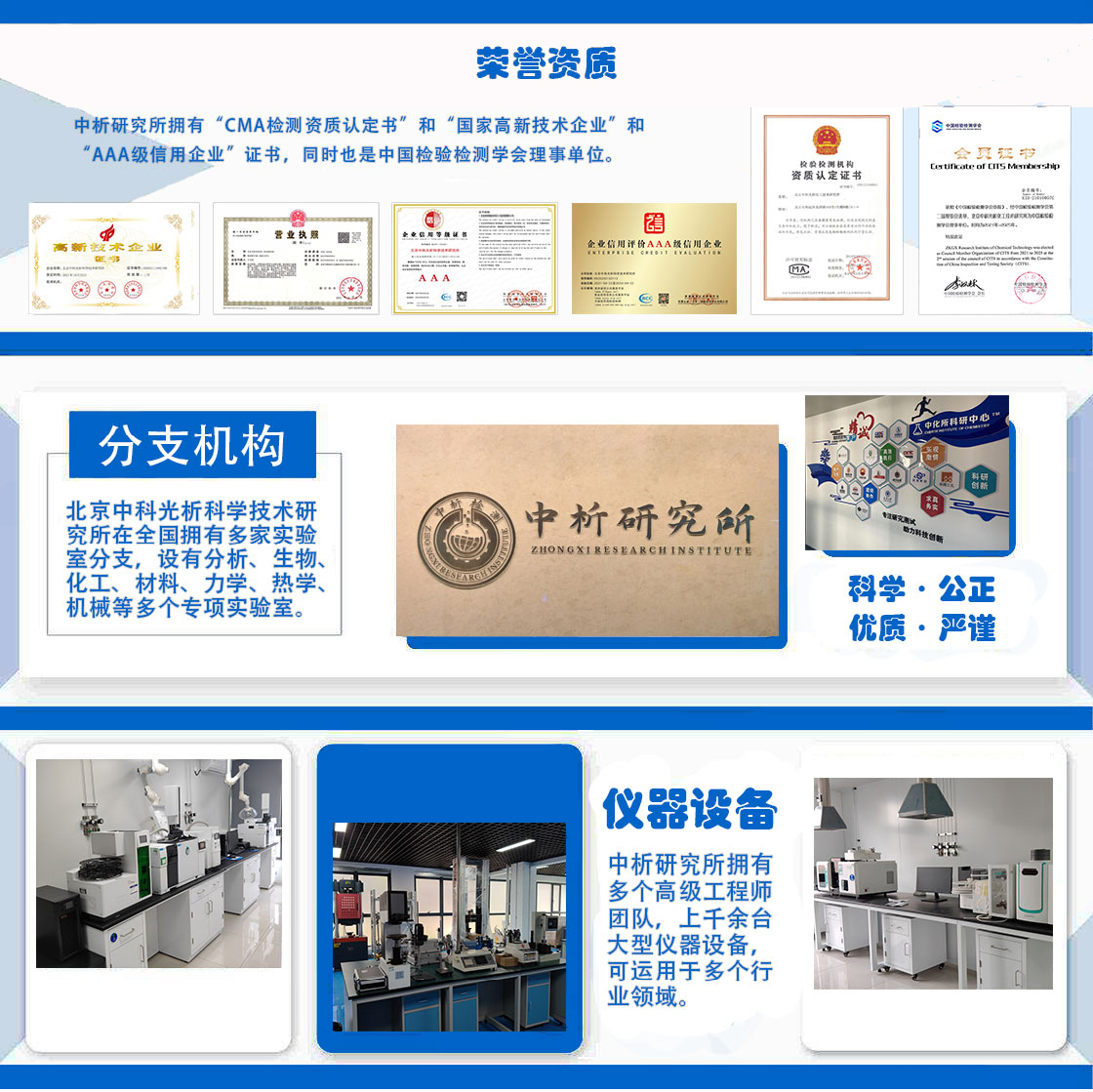
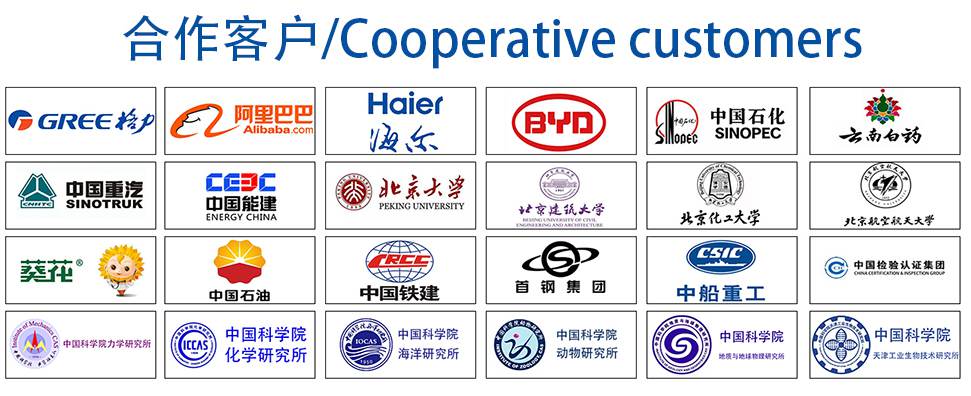