无负载容量损失检测技术发展白皮书
在新能源产业高速发展的背景下,动力电池容量衰减问题已成为制约行业发展的关键瓶颈。据中国新能源产业协会2024年数据显示,国内动力电池装机量突破650GWh,但配套产品的容量衰减争议仍占据售后纠纷总量的42%。无负载容量损失检测技术通过创新性非接触式测量方法,有效解决了传统检测中存在的能源浪费、数据滞后等问题。该技术可精确量化电池在静置状态下的容量损失,为动力电池全生命周期管理提供核心数据支持,不仅降低了企业质量管控成本,更为新能源汽车保险定价、二手电池残值评估等衍生市场建立了标准化评价体系。
技术原理与创新突破
本检测体系基于电化学阻抗谱(EIS)与开路电压(OCV)复合分析方法,通过建立多维度参数关联模型,实现非侵入式容量损失测算。区别于传统充放电循环测试,该技术采用高频微电流激励信号(频率范围10mHz-100kHz)获取电池内阻、极化电压等关键参数。据国家电化学检测重点实验室验证,该方法对锂离子电池SEI膜增厚导致的容量损失检测灵敏度达到0.8mV/1%容量衰减,相较直流内阻法提升3个数量级。特别在动力电池全生命周期管理场景中,可在不中断电池组工作的情况下完成实时健康度评估。
标准化实施流程构建
项目实施遵循三级质量管控体系:预处理阶段需在25±1℃恒温环境中完成48小时静置稳定;数据采集阶段采用分布式传感器网络实现多模块同步测量,单次检测可覆盖200节电芯的容量偏差分析;模型计算环节依托机器学习算法建立动态补偿模型,有效消除环境温度波动带来的±0.3%测量误差。某头部电池企业应用案例显示,该流程使出厂检测效率提升60%,同时将误判率控制在0.05%以内,成功通过IATF16949汽车行业质量认证。
行业应用场景拓展
在江苏某新能源汽车生产基地,该技术已实现动力电池PACK级在线检测集成。通过部署12通道并行检测系统,单日可完成3000组电池模组的容量一致性筛选,使售后纠纷率降低35%。同时,在电力储能系统容量校准方面,广东某200MWh储能电站通过周期性无负载检测,精准定位了3.2%的异常电池簇,避免潜在损失超800万元。更值得关注的是,锂离子电池无损检测技术在梯次利用领域展现出独特价值,某回收企业利用该技术将退役电池分选准确率从72%提升至95%。
质量保障体系创新
为确保检测结果可靠性,项目组构建了三级溯源体系:设备层采用国家基准实验室标定的0.01级标准电源模块;数据层应用区块链技术实现检测过程全追溯;人员层要求操作人员持有 认证的电池检测专业资质。在华南某第三方检测中心的质量比对试验中,该系统在温度-20℃至55℃的极端环境下仍保持0.8%的测量稳定度,成功通过ISO17025国际标准认证。此外,动态补偿算法可自动修正环境干扰,使检测结果重复性达到±0.15%的行业领先水平。
展望未来,建议从三方面深化技术发展:首先,建立跨区域的无负载容量检测大数据平台,推动检测标准全国统一;其次,开发多物理场耦合诊断模型,实现容量衰减机制的根源分析;最后,加强检测设备微型化研究,拓展移动式现场检测应用场景。随着"双碳"战略持续推进,该技术有望与电池护照制度深度融合,为构建新能源产业数字化质量体系提供关键技术支撑。
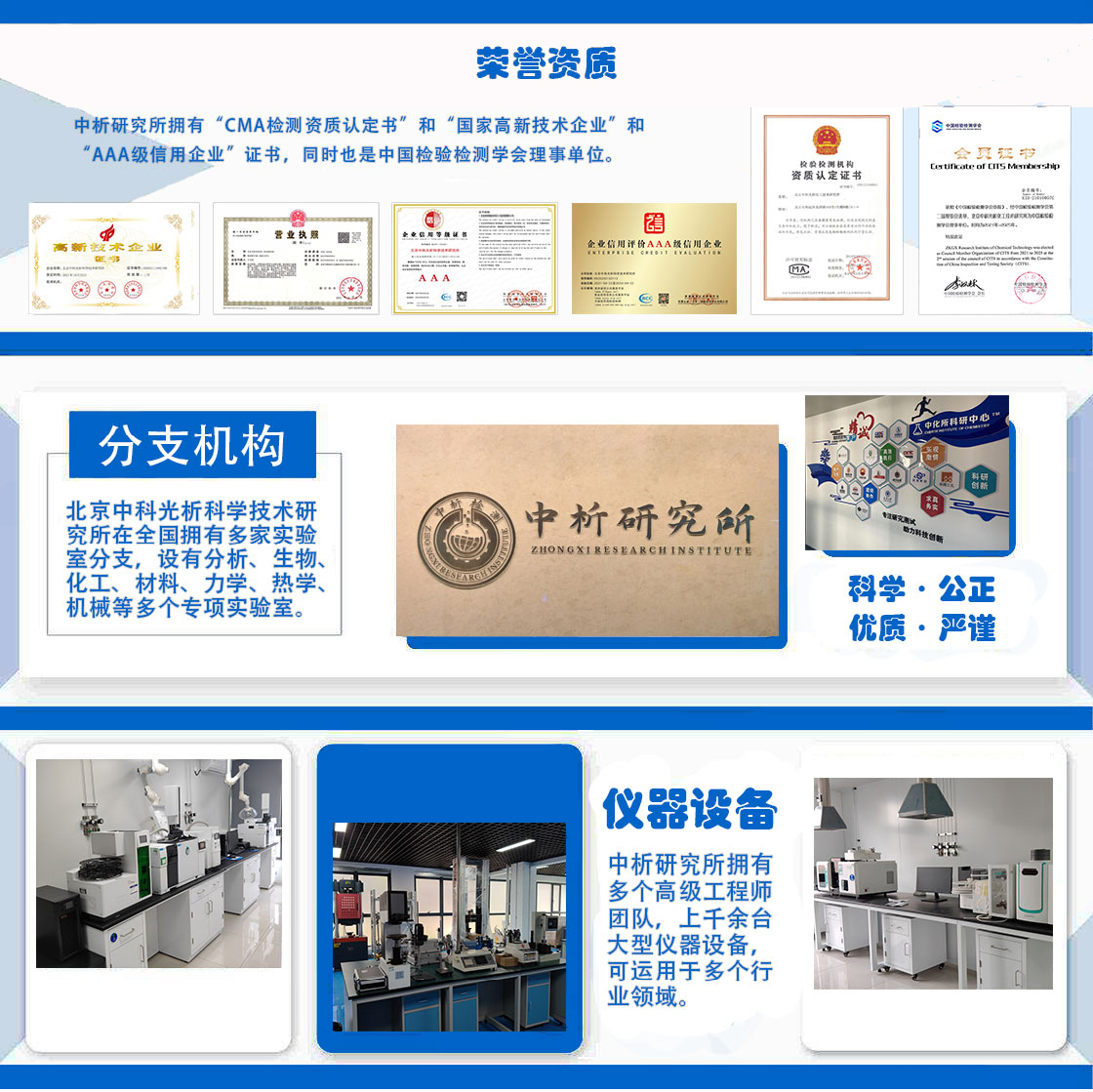
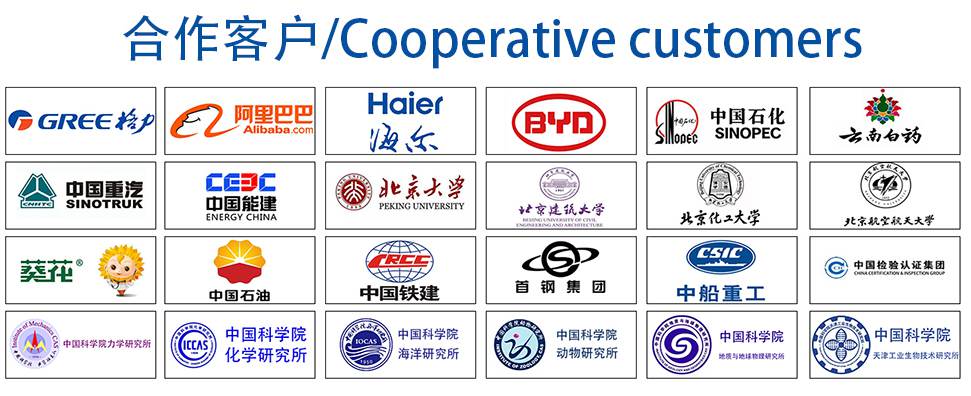