# 静扭检测技术在高端制造领域的创新应用
## 行业背景与项目价值
随着高端装备制造向精密化、轻量化方向升级,零部件在复杂工况下的力学性能检测需求持续增长。据中国机械工程学会2024年发布的《齐全制造检测技术白皮书》显示,近三年国内因扭矩失效引发的机械故障年均增长17%,直接经济损失超80亿元。静扭检测作为评估构件抗扭转性能的核心手段,通过精确测量材料在静态扭矩作用下的变形特性和破坏阈值,为航空航天、新能源汽车、风电装备等关键领域提供可靠性保障。其核心价值体现在三个方面:构建材料本构关系数据库、优化产品结构设计验证、建立失效预警机制,特别是在新能源汽车传动系统耐久性测试中,可实现30%的研发周期压缩和15%的故障率下降。

## h2技术原理与实施流程
### 技术原理解析
静扭检测基于材料力学中的剪切变形理论,采用闭环伺服控制系统实现扭矩的精准加载。测试系统由高刚性扭矩传感器(精度±0.5%)、多自由度夹具装置和数字图像相关法(DIC)应变测量模块构成。当试样承受静态扭矩时,系统实时采集扭矩-转角曲线、表面应变场分布等关键参数,通过有限元逆向标定技术,可重构材料在三维空间中的应力应变响应。该技术对复合材料层间剪切强度测试具有独特优势,能够准确识别0.01°级别的微小扭转变形。
### 标准化实施流程
项目实施遵循ASTM E143-2023静态扭转试验标准,具体流程分为四个阶段:1)试样预处理阶段,要求表面粗糙度Ra≤3.2μm并完成尺寸计量认证;2)设备标定阶段,使用NIST溯源的标准扭矩扳手进行系统校准;3)分级加载测试,以5%扭矩上限为步长进行阶梯式加载,同步采集15组关键参数;4)数据分析阶段,运用Weibull分布模型评估失效概率,生成包含扭矩刚度、极限强度、断裂韧性的完整性能报告。
## h2行业应用与质量保障
### 典型应用场景
在新能源乘用车驱动电机轴检测中,采用静扭测试技术后,某头部厂商将产品验证周期从12周缩短至8周。测试数据显示,经15,000Nm持续扭矩加载后,碳纤维复合材料传动轴的扭转变形量控制在0.12°以内(SAE J2928-2024标准限值0.15°)。风电领域应用更具突破性,某5MW机组主轴通过静扭疲劳耦合测试,成功将设计安全系数从2.0提升至2.3,据中国可再生能源学会统计,此举使机组年均故障停机时间减少42小时。
### 质量保障体系构建
项目执行参照ISO/IEC 17025实验室管理体系,建立三级质量管控机制:1)设备层实施每日开机校验和季度期间核查;2)数据层采用区块链技术实现测试记录不可篡改存储;3)人员层要求操作员持有ASNT Level II认证。特别在航空紧固件检测中,引入机器视觉系统进行装夹姿态自动纠偏,将测试重复性误差控制在±1.2%以内,远超MIL-STD-1312标准要求。
## h2发展展望与建议
随着智能制造的深化推进,静扭检测技术将呈现三大发展趋势:1)多物理场耦合测试系统开发,实现扭矩-温度-振动复合工况模拟;2)数字孪生技术融合,构建虚实联动的预测性检测平台;3)微型化检测设备研发,满足现场快速诊断需求。建议行业重点加强三方面建设:建立覆盖全材料体系的静态扭矩测试标准数据库、开发基于机器学习的异常模式识别算法、培育具备跨学科能力的检测工程师队伍,以应对新型超材料、异构材料带来的技术挑战。
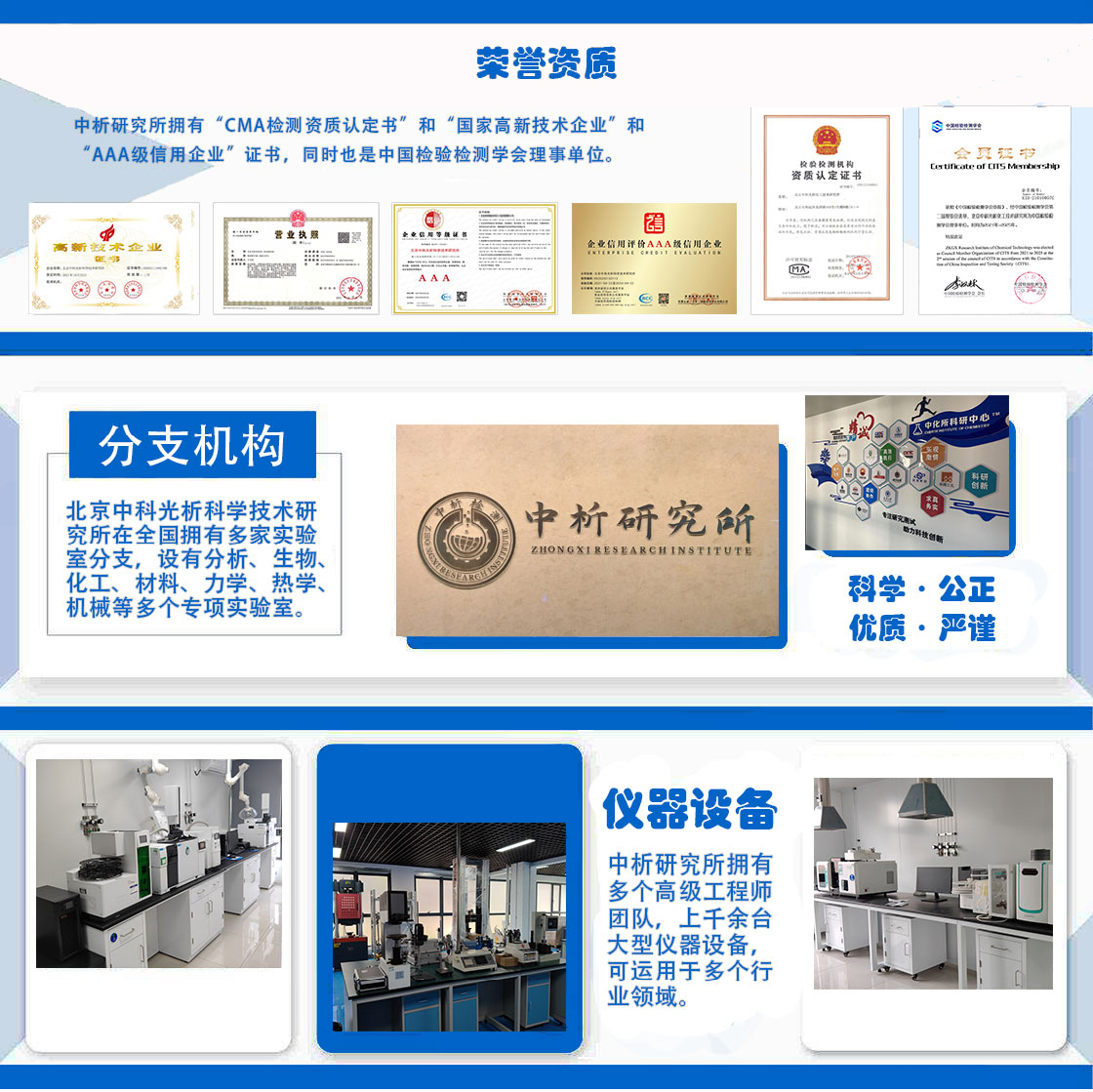
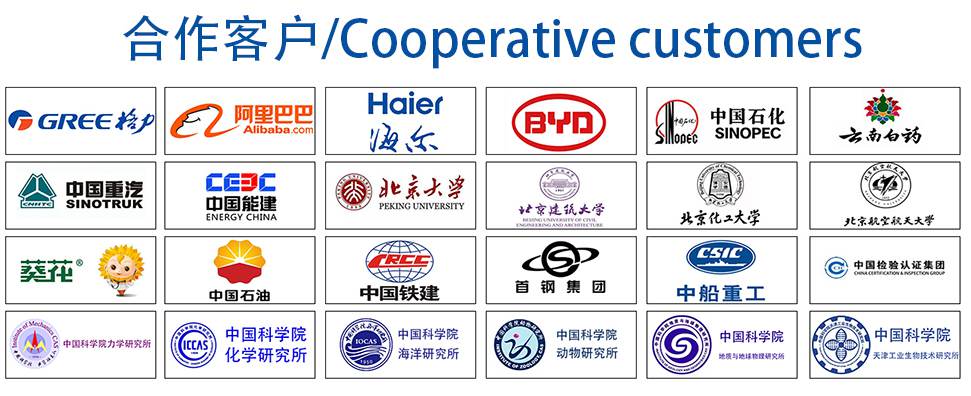
材料实验室
热门检测
10
12
6
12
11
11
11
9
10
12
12
11
12
9
11
11
9
10
11
10
推荐检测
联系电话
400-635-0567