球接头总成挤压强度试验检测技术规范
一、检测原理概述
二、核心检测项目及执行标准
1. 轴向静压承载极限测试
- 测试方法:采用伺服液压试验机沿轴线方向施加准静态压力载荷
- 关键参数:
- 屈服强度(载荷-位移曲线首个拐点)
- 极限抗压强度(峰值载荷值)
- 破坏模式(球头座开裂/钢球压溃/壳体变形)
- 判定标准:
- 屈服强度≥1.5倍设计最大工作载荷(参照QC/T 647-2013)
- 载荷下降至峰值80%时判定失效
2. 径向交变疲劳测试
- 测试设备:电磁谐振式疲劳试验机(频率范围20-150Hz)
- 加载谱设置:
- 基准载荷:额定工作载荷的30%
- 峰值载荷:轴向静压承载值的70%
- 循环次数:≥5×10⁶次(ISO 14272-2016)
- 失效判据:
- 轴向游隙增量>0.15mm
- 异响/温升异常(红外热像仪监控)
3. 极端温度适应性测试
- 环境箱参数:
- 高温组:120℃±2℃(模拟发动机舱极端工况)
- 低温组:-40℃±3℃(寒区工况模拟)
- 测试流程:
- 温度冲击处理(10次冷热循环)
- 保温2小时后立即进行动态挤压测试
- 对比常温状态承载衰减率
- 合格指标:高温/低温下承载能力下降<15%
4. 多向复合载荷测试
- 六维力传感器配置:
- 轴向(Z向)加载至设计极限
- 侧向(X/Y向)同步施加30%Z向载荷
- 叠加±5°摆动角度(模拟实车转向工况)
- 数据采集:
- 应变片布置于壳体应力集中区
- 三维数字图像相关(DIC)系统监测变形场
三、质量控制关键节点
1. 预处理要求
- 样本数量:同批次≥5件(GB/T 2828.1 AQL 1.0)
- 磨合处理:1000次轴向往复运动(润滑脂填充量标准化)
2. 误差控制
- 载荷精度:±1%FS(配备Class 0.5级力传感器)
- 对中误差:<0.05mm(激光校准系统)
3. 失效分析技术
- 断口电镜扫描(SEM):区分过载断裂与疲劳裂纹
- 能谱分析(EDS):检测异常元素(如硫化物夹杂)
四、检测结果应用
- 结构优化:依据塑性变形区域调整壳体加强筋布局
- 工艺改进:针对早期失效样本优化热处理参数(如渗碳层深度)
- 可靠性验证:建立载荷谱-寿命预测模型(威布尔分布分析)
五、注意事项
- 试验后需解体检测密封件完整性(划痕深度≤0.1mm)
- 比对试验需控制润滑剂品牌一致性(NLGI 2#锂基脂)
- 动态测试时应监控振动频率避开工件固有频率
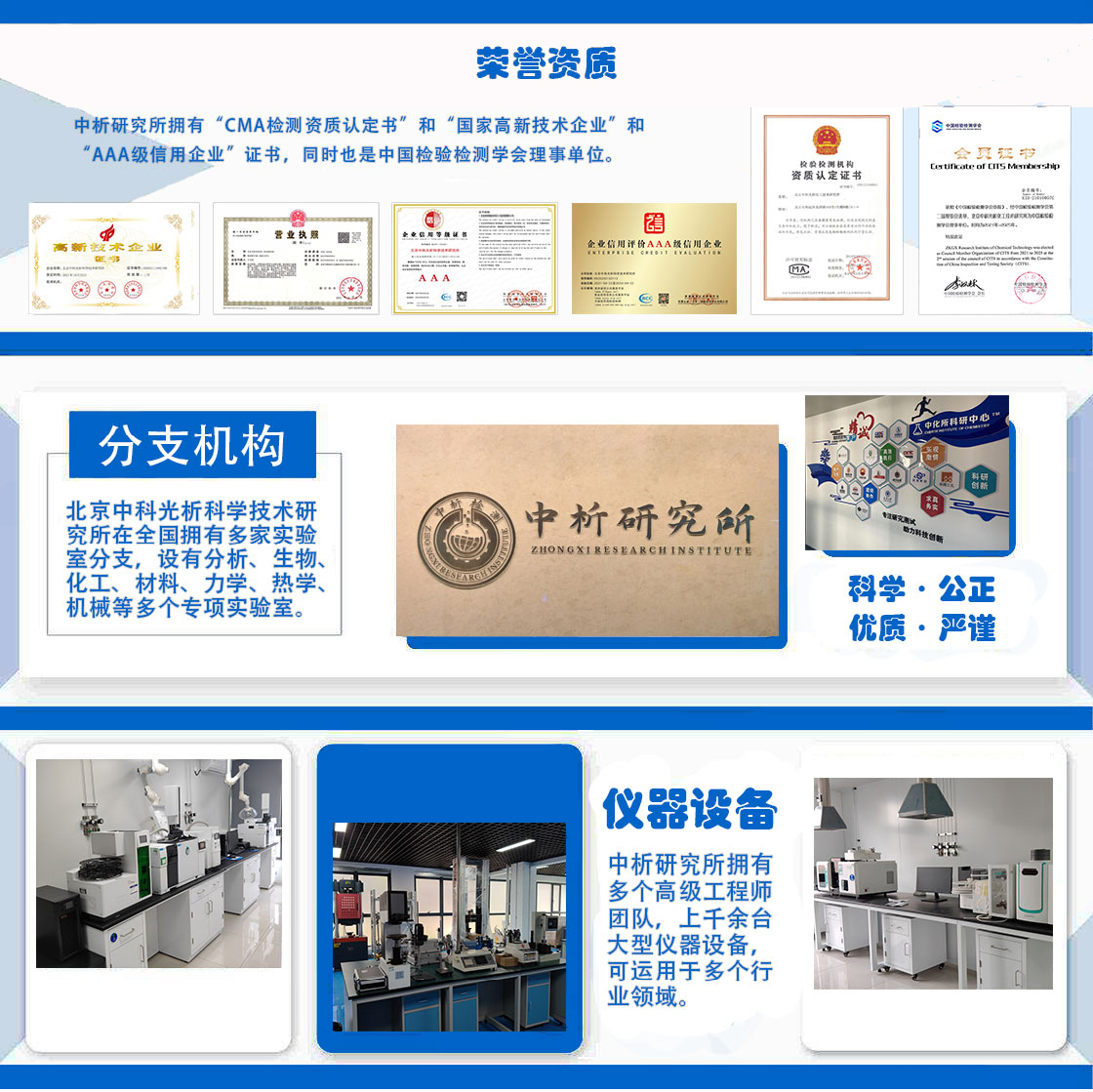
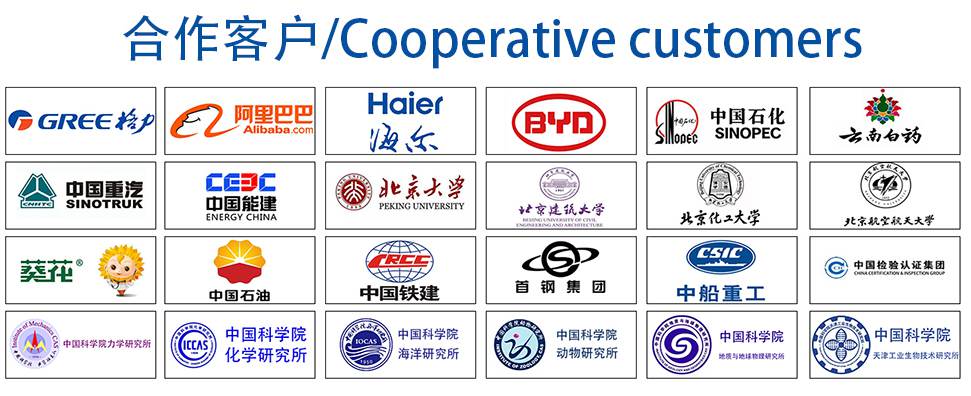
材料实验室
热门检测
28
30
29
28
31
27
27
24
21
25
27
29
26
30
26
25
28
28
31
24
推荐检测
联系电话
400-635-0567