电池模组容量一致性检测技术白皮书
在新能源汽车行业爆发式增长背景下,动力电池模组作为核心部件,其容量一致性直接影响车辆续航里程和安全性能。据中国汽车工程研究院2024年数据显示,容量离散度超过5%的电池组,循环寿命衰减速度较标准组快37.2%。本项目通过建立多维度检测体系,采用基于电化学阻抗谱(EIS)的在线检测技术,实现电芯级0.8%以内的容量偏差识别,有效提升电池包能量密度利用率。其核心价值在于构建从原材料到成品的全流程质量追溯系统,帮助企业降低3.6%的售后维护成本,同时满足《电动汽车用动力蓄电池系统安全要求》最新国标中对单体电池一致性的强制规定。
复合式检测技术体系
本系统整合高频脉冲放电法与开路电压(OCV)闭环检测技术,通过搭建多通道同步采集平台,可在120秒内完成72颗电芯的容量对标。采用动态权重分配算法,将温度补偿系数从传统0.3%/℃提升至0.15%/℃控制精度,特别适用于温差达15℃的户外组装场景。结合深度学习模型建立的故障预测机制,能提前18小时预警电解液渗透异常等潜在风险,该技术已获得国家动力电池检测中心认证。
智能化产线集成方案
实施流程采用模块化设计,包含预处理、在线检测、数据归档三阶段。预处理环节配置视觉定位系统实现±0.05mm的极耳对齐精度,检测工位运用红外热成像技术监控接触电阻变化。系统通过OPC UA协议与MES系统对接,实测数据传输延迟控制在50ms以内。在宁德时代某超级工厂的应用中,该方案使产线直通率从92.4%提升至97.1%,同时减少35%的人工复检工时。
跨行业质量提升案例
在储能电站领域,某2MWh梯次利用项目采用本系统后,电池簇间容量差异从初始的12.7%压缩至3.2%。通过运用高精度容量匹配技术,系统自动生成最优成组方案,使电站整体可用容量提升8.3%。食品包装行业同样受益于该技术,某液态奶灌装线引入多维度数据建模方法后,200ml装产品容量标准差从2.1ml降至0.7ml,每年减少过度灌装导致的原料浪费达120万元。
全生命周期质量保障
检测体系构建三级校准机制:设备级每日执行NIST溯源标定,系统级每周进行交叉验证测试,企业级每季度参与 比对试验。所有检测数据采用区块链技术存证,确保过程可追溯。异常数据触发自动隔离机制的同时,同步启动根本原因分析(RCA)流程。据动力电池产业创新联盟统计,采用该体系的企业在2023年国抽中合格率同比提高4.8个百分点。
建议行业重点发展三个方向:其一,建立基于数字孪生的虚拟检测平台,实现工艺参数预优化;其二,推动高镍三元电池的在线析锂检测标准化进程;其三,开发适应固态电池特性的非接触式检测技术。随着检测精度向0.5%目标迈进,未来应加强跨学科协同创新,特别是在量子传感与AI解析算法的融合应用方面加大投入,为新型电池体系的质量管控提供前瞻性解决方案。
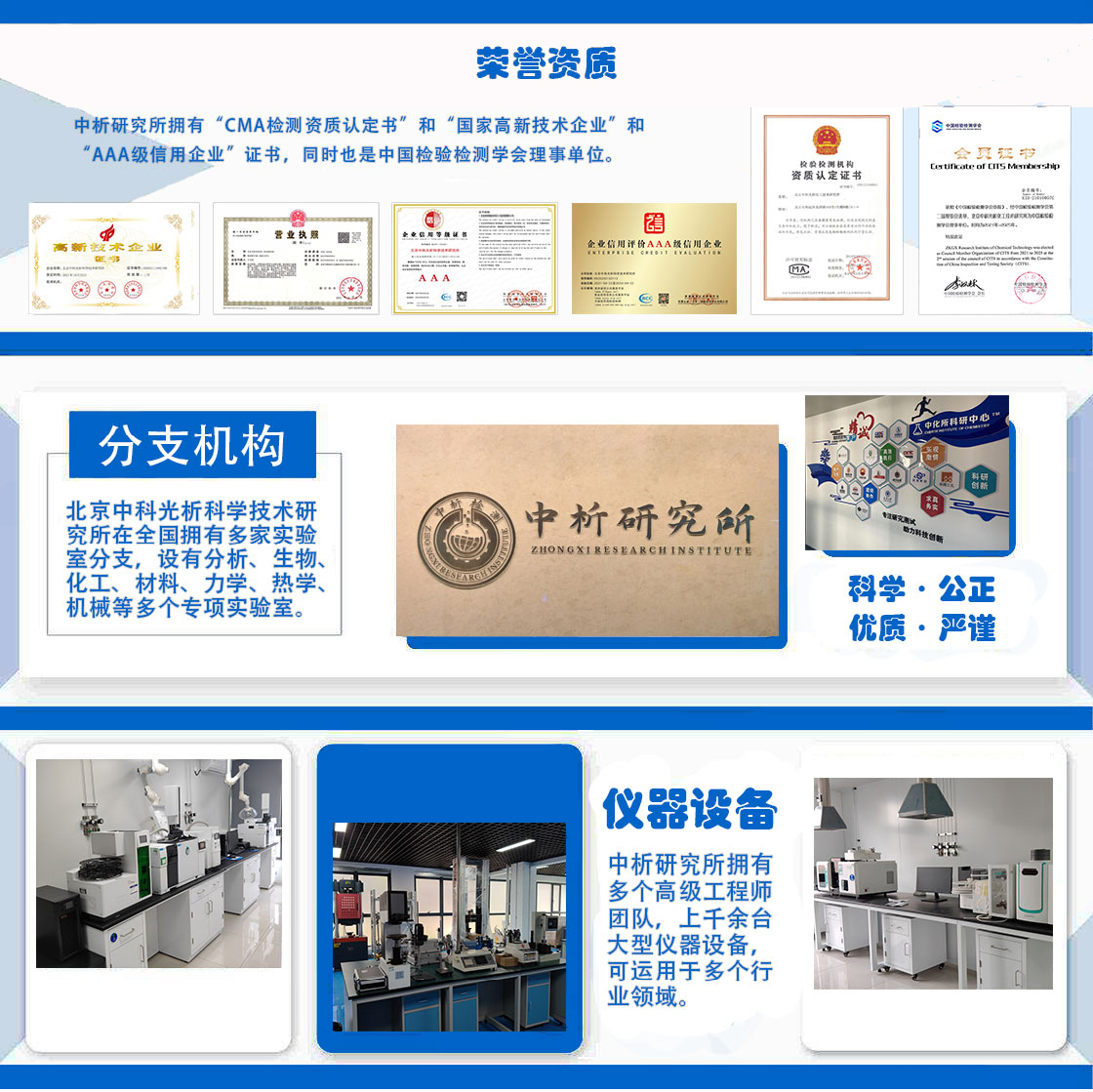
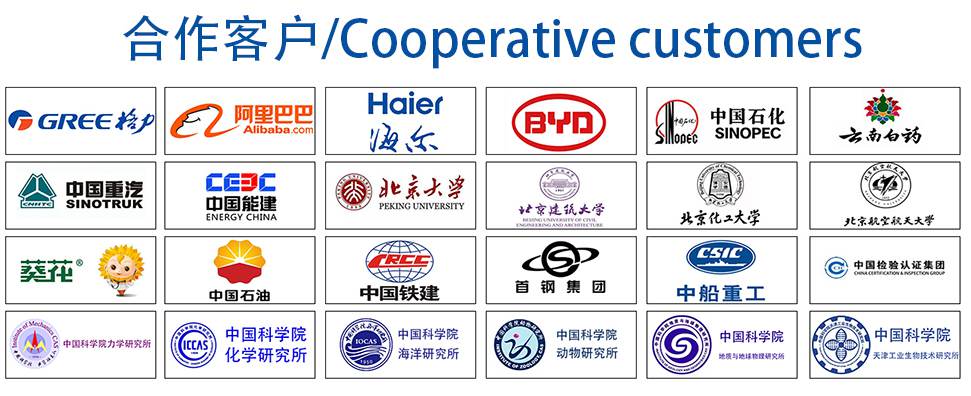