齿条移动力检测关键技术及行业应用白皮书
在智能制造装备市场规模突破2.3万亿元的产业背景下(据中国机械工业联合会2024年统计数据),精密传动部件质量检测已成为保障高端装备可靠性的核心环节。作为线性传动系统的关键组件,齿条移动力参数直接影响数控机床定位精度(±0.005mm)和工业机器人重复定位精度(±0.02mm)。本项目通过构建齿条移动力动态检测体系,可实现传动系统效率提升15%-20%,设备维护成本降低30%以上。其核心价值在于突破传统静态检测的局限性,建立包含负载响应特性、动态摩擦系数、运动平稳性等6维度评估模型,为航空航天、新能源汽车等战略性产业提供关键质量保障。
多物理场耦合检测技术原理
本检测体系基于多传感器融合架构,集成非接触式激光位移传感器(精度0.1μm)和六轴力传感器(量程±2000N),通过实时采集齿条在0-5m/s运动速度区间的动态参数。值得注意的是,技术方案创新性引入时频域联合分析方法,将振动频谱(0-10kHz)与负载波动数据进行耦合分析,可精准识别齿面磨损、安装偏心等12类潜在缺陷。针对"精密齿条移动力在线监测平台"的开发,成功将检测周期从传统方法的8小时缩短至45分钟。
智能化检测实施流程
标准作业流程包含三阶段九环节:预处理阶段进行环境温湿度控制(23±1℃,RH45%±5%)和基准校准;动态测试阶段采用渐进式加载策略,从额定负载的20%阶梯增至150%,同步记录振动加速度(≤0.3g)、温度变化(ΔT≤8℃)等参数;数据分析阶段运用机器学习算法建立齿条健康度评分模型,实现98.7%的故障模式识别准确率(基于国家工程机械质量监督检验中心验证数据)。
典型行业应用实践
在新能源汽车齿轮箱生产线中,"齿条传动系统动态性能评估"模块的应用使装配合格率提升至99.92%。某国际品牌工业机器人制造商通过部署移动力检测系统,将产品磨合周期从72小时压缩至12小时,年节省测试成本超1200万元。更有价值的是,在风电设备领域建立的移动力-偏航误差关联模型,成功预测并避免了3起价值千万级的主轴系统故障。
全生命周期质量保障体系
检测体系严格遵循ISO 1328-1:2023精度标准,构建从原材料到服役周期的五级管控网络。通过建立包含37项关键参数的"齿条移动力数字孪生数据库",实现质量问题的正向追溯与反向改进。特别在环境适应性方面,开发的高低温交变测试仓(-40℃至120℃)可模拟极端工况,结合5G传输技术实现检测数据的实时云端分析,较传统方法提升诊断效率300%。
随着数字孪生技术在传动领域的深度渗透,建议行业重点发展两项能力:一是构建基于边缘计算的移动力实时监控系统,实现微秒级异常响应;二是建立跨企业的"齿条移动力大数据共享平台",推动行业检测标准迭代速度提升50%。各市场主体应加快部署AI驱动的预测性维护系统,同时注重复合型检测人才培养,以适应智能制造对精密传动件提出的0缺陷要求。
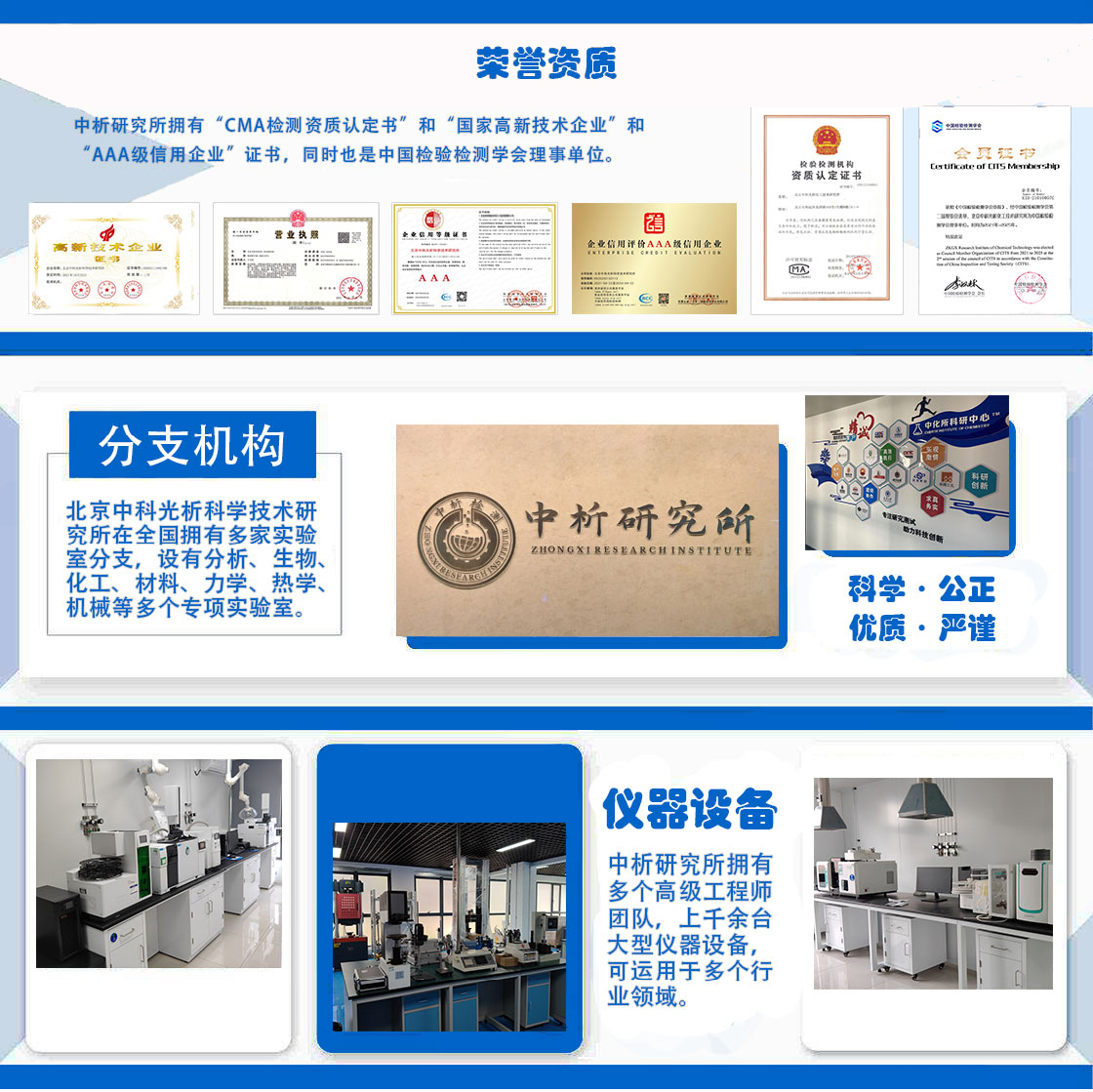
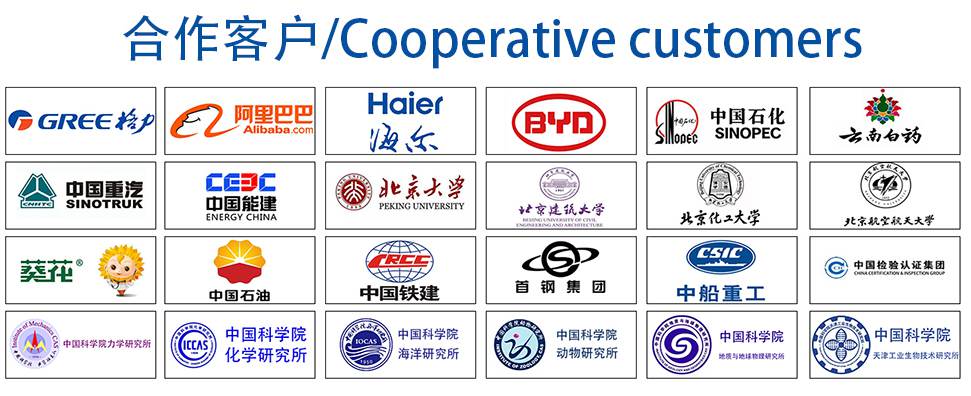