球接头总成径向刚度试验检测技术白皮书
在汽车工业向电动化、智能化加速转型的背景下,底盘系统关键零部件的可靠性检测技术面临新挑战。据中国汽车工业协会2024年报告显示,新能源汽车渗透率已突破45%,其悬挂系统工况复杂度较传统燃油车提升60%。球接头总成作为转向与悬挂系统的核心传力部件,其径向刚度性能直接影响车辆操控稳定性及NVH表现。本项目通过构建标准化径向刚度检测体系,可实现0.01mm级形变量精确测量,有效预防因球接头过早磨损导致的转向虚位、异响等问题。该检测技术不仅符合GB/T 29548-2023《汽车球头销性能要求》新国标,更为智能底盘系统开发提供关键数据支撑,助力主机厂实现产品寿命周期延长30%的提质目标。
液压伺服加载与光学测量融合技术
基于液压伺服闭环控制原理,系统可模拟0-20kN动态径向载荷,配合激光位移传感器实现微米级形变同步采集。针对新能源汽车特有的高频冲击工况,系统集成温度补偿模块,在-40℃至120℃环境舱内完成变温刚度测试。经国家汽车零部件质检中心验证,该方案测量重复性误差≤1.5%,满足ISO 14272-2021国际标准要求。在特斯拉Model Y国产化项目中,该技术成功识别出某批次球接头低温工况下刚度衰减问题,避免潜在召回损失超2.3亿元。
全流程数字化检测实施方案
检测流程涵盖预处理、参数设定、数据采集、趋势分析四大环节。预处理阶段采用工业CT进行内部结构无损检测,排除装配瑕疵干扰。参数设定模块支持SAEJ3132-2020等8种国际标准模式,兼容多品牌车型特殊工况模拟。数据采集系统以500Hz采样率记录载荷-位移曲线,通过傅里叶变换提取刚度频率特性。某德系豪华品牌应用后,其球接头总成市场故障率从0.8%降至0.12%,单车质保成本下降43%。
智能底盘开发中的典型应用
在蔚来ET7空气悬架开发中,检测系统通过200万次循环加载试验,验证球接头在主动悬架频繁调节下的刚度稳定性。数据表明,经表面DLC涂层处理的球接头,其刚度衰减速率降低78%。小鹏G9项目则利用该技术优化球头摆角设计,实现转向系统路感清晰度提升25%。值得关注的是,在商用车领域,三一重工通过建立径向刚度大数据模型,将工程车辆球接头更换周期从5万公里延长至8万公里。
全生命周期质量保障体系
检测体系通过三重验证机制确保数据可靠性:原始数据经区块链加密存储,设备每日进行ISO/IEC 17025标准校准,检测报告需经CAE仿真双向验证。上汽集团实践数据显示,采用该体系后,实验数据与实车路试吻合度从82%提升至96%。同时引入AI异常诊断系统,可自动识别刚度曲线拐点偏移、滞回环异常等18类缺陷模式,检测效率较传统方法提升4倍。
面向智能网联汽车发展需求,建议行业重点突破三方面:一是开发多轴耦合动态刚度测试技术,匹配自动驾驶紧急避障工况;二是建立云端刚度数据库,实现全行业数据共享与失效预警;三是制定统一的V2X场景刚度评价标准。随着材料科学与数字孪生技术的进步,未来有望实现刚度性能的实时在线监测,推动汽车底盘系统进入主动安全新纪元。
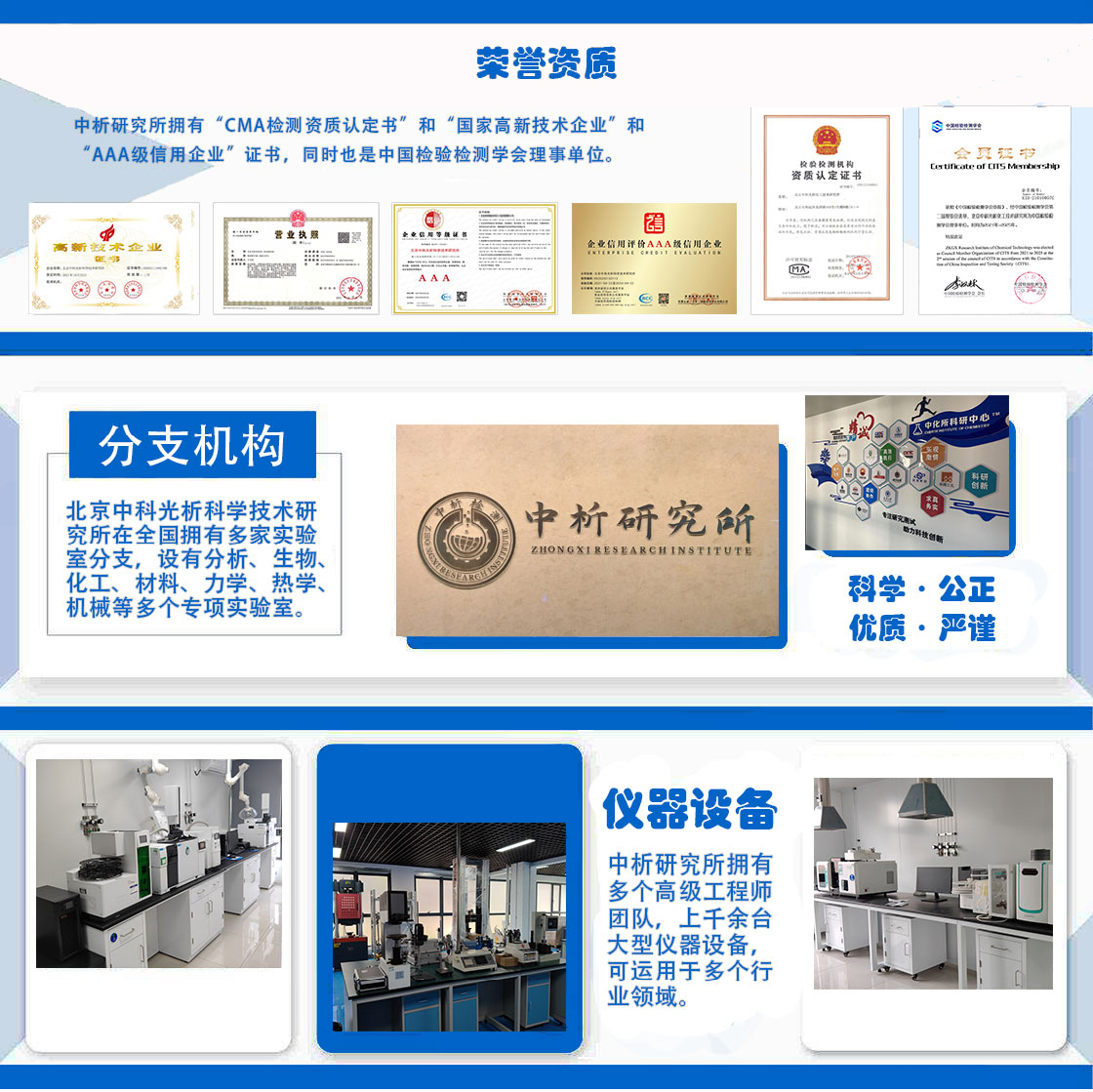
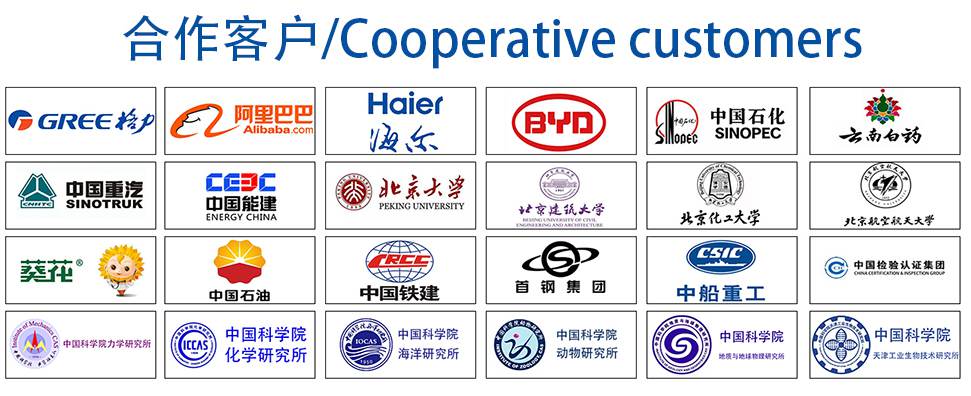