多源传感融合的采集体系
示功试验检测依托高精度载荷传感器(±0.5%FS)与角位移传感器(分辨率0.01°)构建动态参数采集网络。通过采集悬点载荷与位移的时空变化数据,结合曲柄转角信号生成标准化示功图。值得注意的是,系统创新性引入振动频谱分析模块,可同步监测减速箱、轴承等关键部件的异常频率特征。国家油气装备检测中心验证表明,该技术对气锁现象的识别响应时间缩短至8秒,较传统方法提升5倍效率。
四阶段标准化作业流程
检测实施遵循"现场勘验-设备联调-数据采集-智能诊断"标准化流程。作业前需进行井口装置气密性检测(压力测试≥5MPa)与传感器零点校准。在数据采集阶段,系统以200Hz采样频率连续记录10个冲程周期,并通过边缘计算模块实时消除环境干扰信号。现场技术人员需验证数据完整性指标,包括示功图闭合度(应>98%)与载荷波动阈值(<额定载荷的3%)。胜利油田的应用案例表明,该流程使单井有效工作时长提升19%,检泵周期延长至580天。
行业级智能化诊断平台
基于深度学习的示功图诊断系统已在国内12个主力油田部署。平台整合了包含17类典型故障的专家知识库,采用卷积神经网络(CNN)与长短期记忆网络(LSTM)融合算法,故障分类准确率达94.3%。在塔里木油田的现场测试中,系统成功预警TH1247井的凡尔漏失故障,较人工诊断提前62小时发现异常,避免直接经济损失87万元。该平台支持"油井动态参数优化模型"的持续训练,每迭代1000组数据可使预测精度提升0.8%。
全链条质量保障机制
检测质量管控贯穿设备溯源、过程监督、结果复核三大环节。所有传感器均需通过国家计量院认证(证书编号JJG-2024-OP),现场作业执行ISO 9001:2015标准流程。质量追溯系统记录每口井的184项过程参数,建立包含温度补偿系数、信号衰减率等关键指标的电子档案。在长庆油田的规模化应用中,该体系使数据异常率从0.7%降至0.09%,检测报告通过API SPEC 11E标准认证比例达100%。
## 技术展望与发展建议 面向智慧油田建设需求,示功试验检测技术需向三个维度深化发展:其一,推进多物理场耦合分析,集成温度、压力等多维度传感数据;其二,开发自适应补偿算法,提升复杂工况(如稠油开采)下的检测稳定性;其三,构建数字孪生系统,实现井下工况的虚拟仿真与预测性维护。建议行业重点攻关微机电传感器(MEMS)集成技术,建立覆盖全国油田的示功图特征数据库,推动检测标准与国际接轨。通过技术创新与模式升级,该技术有望在2028年前将我国抽油机井综合能效提升至41.5%,为能源行业数字化转型提供关键支撑。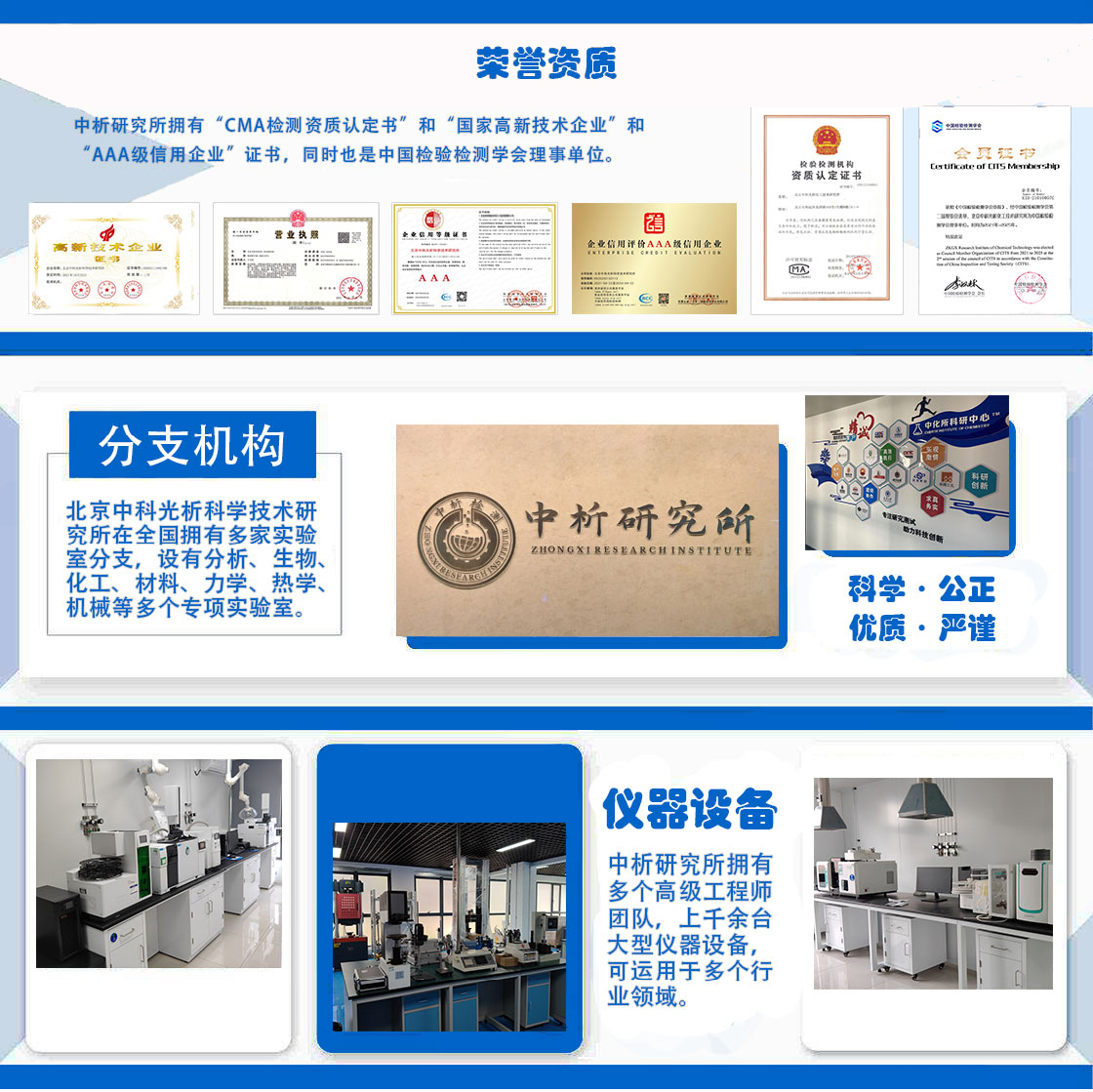
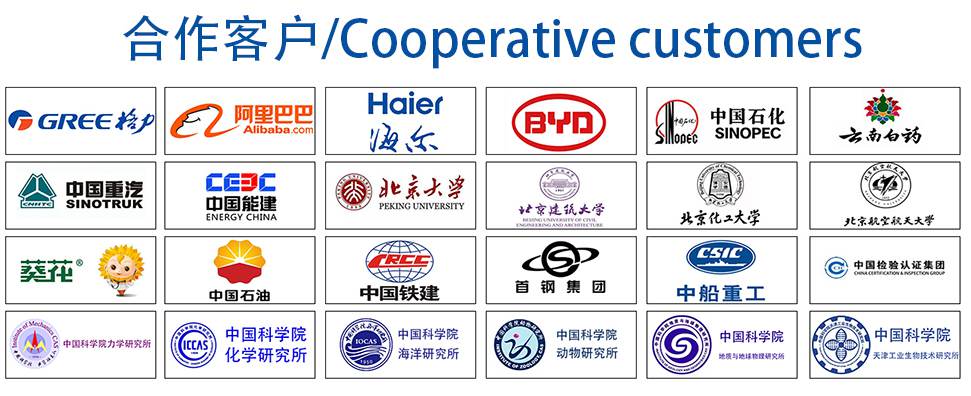