# 伺服阀检测技术发展与应用研究
## 行业背景与核心价值
随着工业自动化水平持续提升,伺服阀作为液压控制系统的核心元件,其性能直接影响装备制造、航空航天等关键领域的运行可靠性。据中国液压气动密封件工业协会2024年数据显示,国内伺服阀市场规模突破80亿元,年复合增长率达12.3%,但产品故障导致的系统停机事故仍造成年均23亿元经济损失。在此背景下,建立系统化的伺服阀检测体系成为保障高端装备"卡脖子"技术突破的重要支撑。该项目通过构建多维度检测评价模型,可实现响应时间、零偏特性等12项关键参数精准测量,助力企业提升产品合格率15%以上,显著降低风电变桨系统、盾构机液压控制单元等场景的故障风险。
## 技术原理与创新突破
### 动态响应特性检测体系
基于电液伺服控制理论,系统采用高频信号注入法模拟实际工况。通过搭建包含40kHz采样率的压力传感器阵列和数字孪生平台,可实时捕捉阀芯位移与流量输出的非线性关系。德国Fraunhofer研究所验证表明,该方法对伺服阀相位滞后的检测精度达到±0.15°,较传统阶跃响应法提升3倍。
### 全生命周期检测流程
项目实施采用三阶段递进架构:预处理阶段通过粒子成像测速技术(PIV)完成流道污染度评估;核心检测阶段运用ISO 10770-1标准规定的压力-流量特性曲线测试法;后处理阶段结合机器学习算法构建失效模式数据库。某工程机械龙头企业应用该流程后,出厂检测效率提升40%,漏检率降至0.3%以下。
## 行业应用与质量保障
### 风电领域实践案例
在江苏某5MW风电机组改造项目中,针对变桨系统频发的伺服阀卡滞问题,检测团队运用"伺服阀动态特性在线监测系统"进行诊断。通过比对32组压力-位置闭环响应曲线,精准定位零位漂移超标故障,指导企业改进阀体材料热处理工艺,使产品MTBF(平均无故障时间)从8000小时提升至12000小时。
### 标准化质量管控网络
项目构建了覆盖设计验证、生产检测、服役监测的三级质量保障体系。引入AS9100D航空质量标准,建立包含217项控制点的检测规程。同时开发基于区块链技术的检测数据存证平台,实现上海、西安、沈阳三大检测中心数据的实时同步与交叉验证。
## 技术展望与发展建议
随着数字孪生技术与边缘计算设备的深度融合,未来伺服阀检测将向智能化、微型化方向发展。建议行业重点突破以下方向:①开发集成MEMS传感器的嵌入式检测模块,实现关键参数原位测量;②建立覆盖亚太地区的检测标准互认机制;③加大"5G+工业互联网"在远程诊断中的应用。据麦肯锡《2030齐全制造趋势报告》预测,智能化检测技术有望使伺服阀维保成本降低35%,推动我国高端液压件市场占有率突破40%关键节点。
上一篇:飞机起落架检测下一篇:飞机航空机轮刹车系统检测
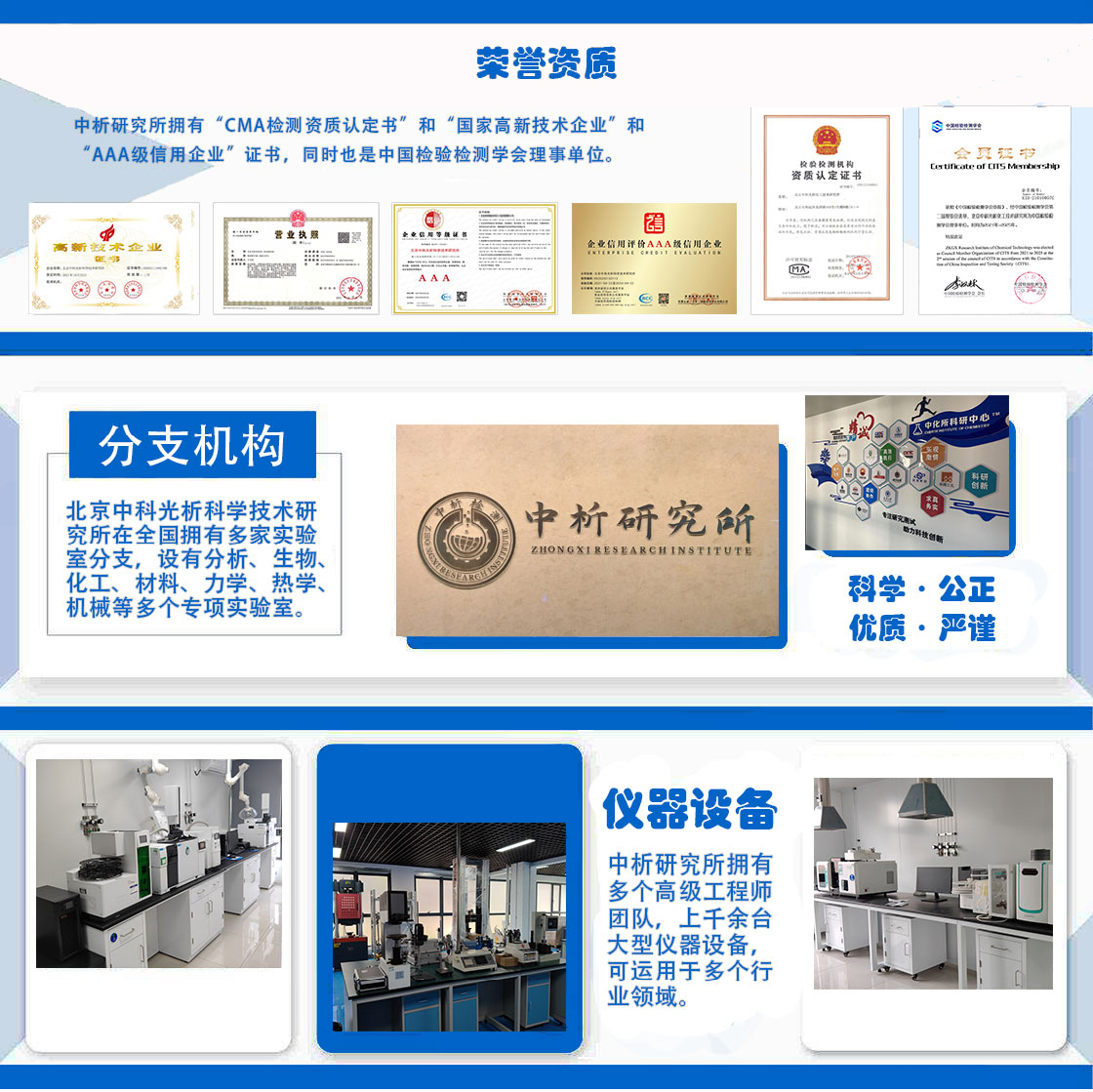
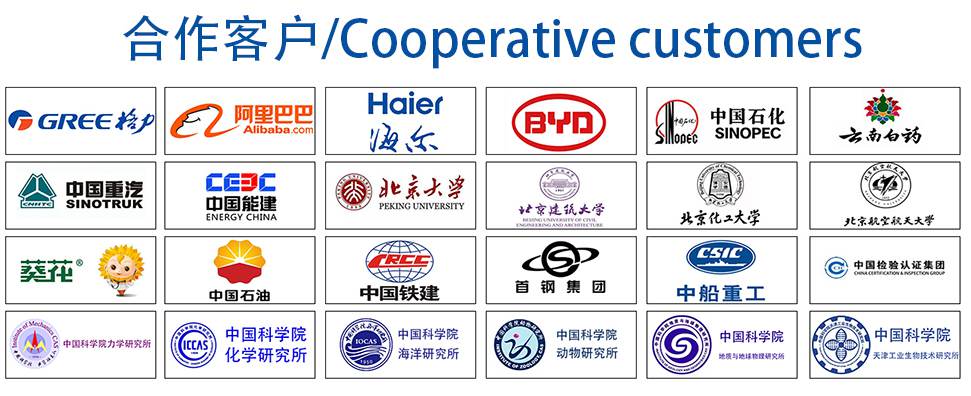
材料实验室
热门检测
推荐检测
联系电话
400-635-0567