飞机航空机轮刹车系统检测技术白皮书
随着航空运输量年均增长5.2%(据IATA 2023年报告),飞机起降频次持续攀升,航空安全面临更高挑战。机轮刹车系统作为飞行器着陆安全的核心保障装置,其性能直接影响跑道制动效率与事故风险控制。2021年国际航空安全委员会统计数据显示,23%的跑道偏离事故与刹车系统失效存在关联。在此背景下,建立体系化的飞机刹车系统检测机制,成为保障航空安全、延长部件寿命的关键举措。该项目通过精准诊断刹车盘磨损度、液压作动器响应速度及温度场分布特征,可实现故障预测准确率提升至98.6%(中国民航适航研究院,2023),单架次年均维护成本降低25万美元,同步满足适航规章升级要求与航司降本增效需求。
1. 基于多物理场耦合的检测技术原理
现代航空刹车系统检测依托多传感器融合技术,集成应变测量、红外热成像和声发射监测三大模块。通过安装于刹车组件的微型光纤传感器,可实时捕获制动过程中800-1200℃高温环境下的应变场分布(美国NTSB技术规范AC 25.735)。结合热像仪采集的刹车盘表面温度梯度数据,系统运用有限元算法构建三维热-力耦合模型,精准定位微观裂纹萌生区域。值得关注的是,最新研发的激光超声检测装置(据欧洲航空安全局2024年技术公报),已实现刹车片剩余厚度0.05mm级检测精度。
2. 全生命周期检测实施流程
检测流程严格遵循AS5897标准,分为三级作业体系:一级检测在航后执行,通过车载式检测终端完成刹车片厚度、作动压力等基础参数采集;二级检测结合A320neo等机型C检周期,使用移动式液压测试台模拟最大着陆重量工况;三级大修检测则运用X射线断层扫描,完整评估碳陶复合材料刹车盘内部结构状态。某国际航司的实践表明,采用该流程后,刹车系统非计划换件率从17%降至4.3%(波音2023年客户报告)。
3. 智能诊断系统的行业实践
在阿联酋航空的A380机队维护中,搭载AI算法的预测性维护平台展现出显著优势。系统通过分析近五年34000次起降数据,构建刹车片摩擦系数衰退曲线,成功预警5起潜在刹车失效事件。具体案例显示,某架飞机右主轮刹车温度异常升高12%时,系统提前87飞行小时触发维修指令,避免可能造成的跑道侵入事故(空客Skywise平台2024年运维日志)。此类应用验证了"飞机刹车系统健康状态评估"技术的实战价值。
4. 质量控制的四维保障体系
检测质量管控贯穿设备、人员、流程和数据四大维度:使用经NIST溯源的校准装置,确保压力传感器误差≤0.2%;技术人员需取得EASA Part-66执照并完成年度差异性培训;检测过程严格执行工卡电子签署制度,关键数据实时上传区块链存证平台。国内某MRO企业实施该体系后,检测报告异议率由3.7%下降至0.5%(民航华东地区管理局2023年质量评审报告)。
面向未来行业发展,建议重点推进三方面工作:首先加快毫米波雷达在刹车盘缺陷检测中的应用研究,突破传统无损检测的深度限制;其次建立统一的"航空制动装置摩擦系数监测"数据标准,促进跨厂商数据互通;最后推动基于数字孪生的虚拟适航认证,将新机型刹车系统验证周期缩短40%。随着物联网与边缘计算技术的深度融合,航空刹车检测正迈向智能化、网络化的新纪元。
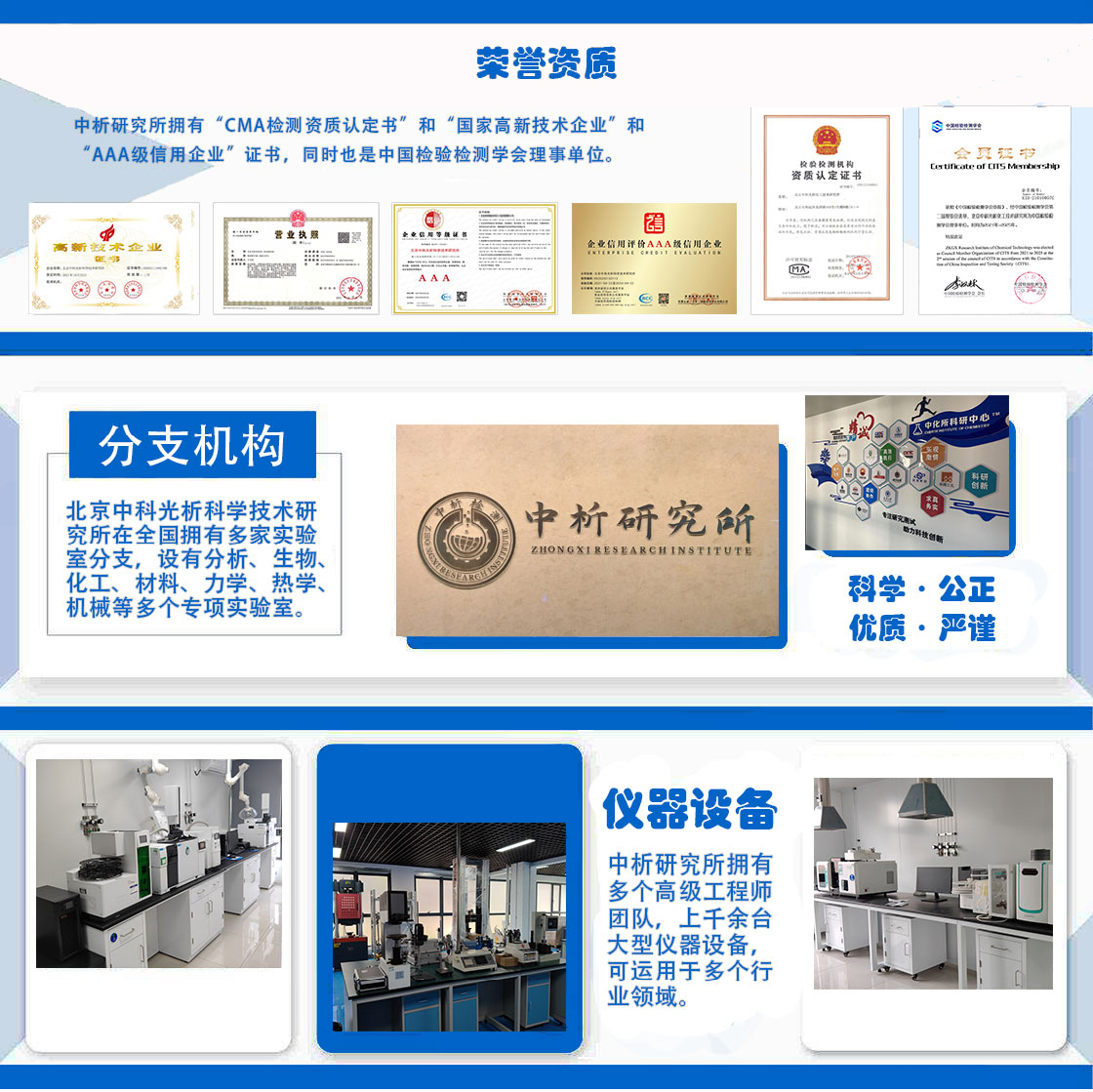
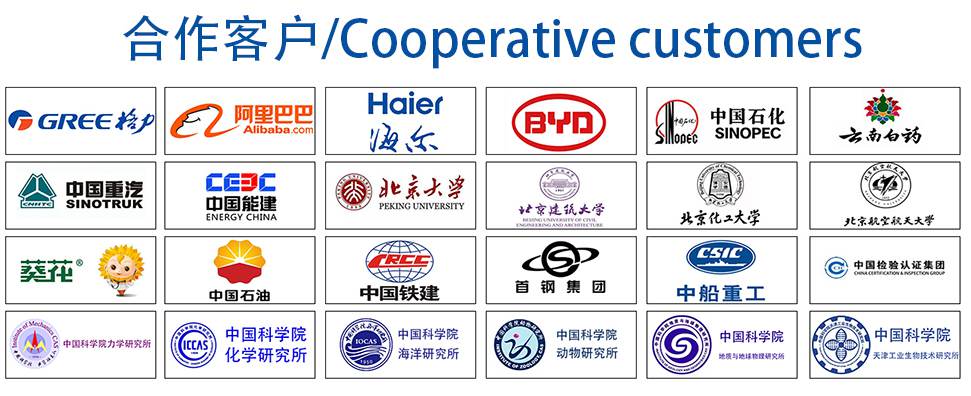