尺寸偏差和外观检测关键技术研究与应用白皮书
在工业4.0与智能制造深度融合的背景下,产品尺寸偏差和外观检测已成为制造业质量控制的核心环节。据中国机械工业联合会2024年数据统计,因尺寸超差导致的产品退货率占工业品质量问题的37%,而表面缺陷引起的客户投诉占比达42%。本项目通过构建基于机器视觉与深度学习的高精度检测体系,可实现±0.005mm的尺寸测量精度和99.2%的缺陷识别准确率(国家计量科学研究院认证),有效解决传统人工检测效率低、标准不统一等行业痛点。其核心价值不仅在于提升生产良率,更通过在线质量数据闭环反馈系统,为工艺优化提供实时决策依据。
多模态融合检测技术原理
本检测体系采用机器视觉、激光扫描与三维点云重构的复合技术方案。其中,高精度三维重构技术通过多光谱成像获取物体表面特征,结合改进型PointNet++算法实现亚像素级边缘定位。针对复杂曲面检测难题,系统引入自适应基准坐标系算法,可自动补偿工件装夹偏差带来的测量误差。值得注意的是,基于迁移学习的表面缺陷分类模型,在金属件划痕检测场景中实现98.7%的识别准确率(中国质检协会测试数据),较传统算法提升23个百分点。
智能化检测实施流程
标准实施流程包含四个关键阶段:首先部署分布式视觉传感器阵列,构建覆盖360°检测视角的硬件网络;其次通过标准量块进行坐标系标定,建立检测环境的空间映射模型;随后启动在线学习模式,系统自动采集100组以上合格样本构建特征数据库;最后进入动态检测阶段,通过实时比对实现0.8秒/件的检测节拍。在某汽车零部件企业应用中,该流程使轮毂螺栓孔位置度检测效率提升4倍,误检率从1.2%降至0.15%。
跨行业应用场景解析
在3C电子行业,系统成功应用于手机中框平面度检测,通过多相机阵列同步采集技术,可同时测量12个关键尺寸特征。航空航天领域则创新采用非接触式激光扫描,实现涡轮叶片型面0.003mm精度的全检。特别在新能源汽车电池模组检测中,系统集成热成像模块,可同步捕捉尺寸偏差与焊接熔深异常,使Pack组装合格率提升至99.6%(工信部2024动力电池白皮书数据)。
全生命周期质量保障体系
为确保检测系统可靠性,建立三级校准验证机制:每日进行标准量具比对校准,每周实施环境参数补偿修正,每月执行全系统计量溯源。同时构建智能质量追溯系统,将检测数据与MES系统深度集成,实现缺陷特征与生产工艺的关联分析。在某家电龙头企业应用中,通过SPC控制图预警机制,提前发现注塑模具0.01mm的磨损偏差,避免批次性质量事故。
展望未来,建议从三方面深化技术发展:一是推动5G+边缘计算在实时检测中的应用,实现分布式检测节点协同;二是加强小样本学习算法研究,解决定制化产品快速建模难题;三是建立行业级检测标准数据库,促进检测结果跨企业互认。通过技术标准与产业应用的深度融合,尺寸偏差与外观检测将逐步从质量把关向工艺优化升级,为智能制造提供核心数据支撑。
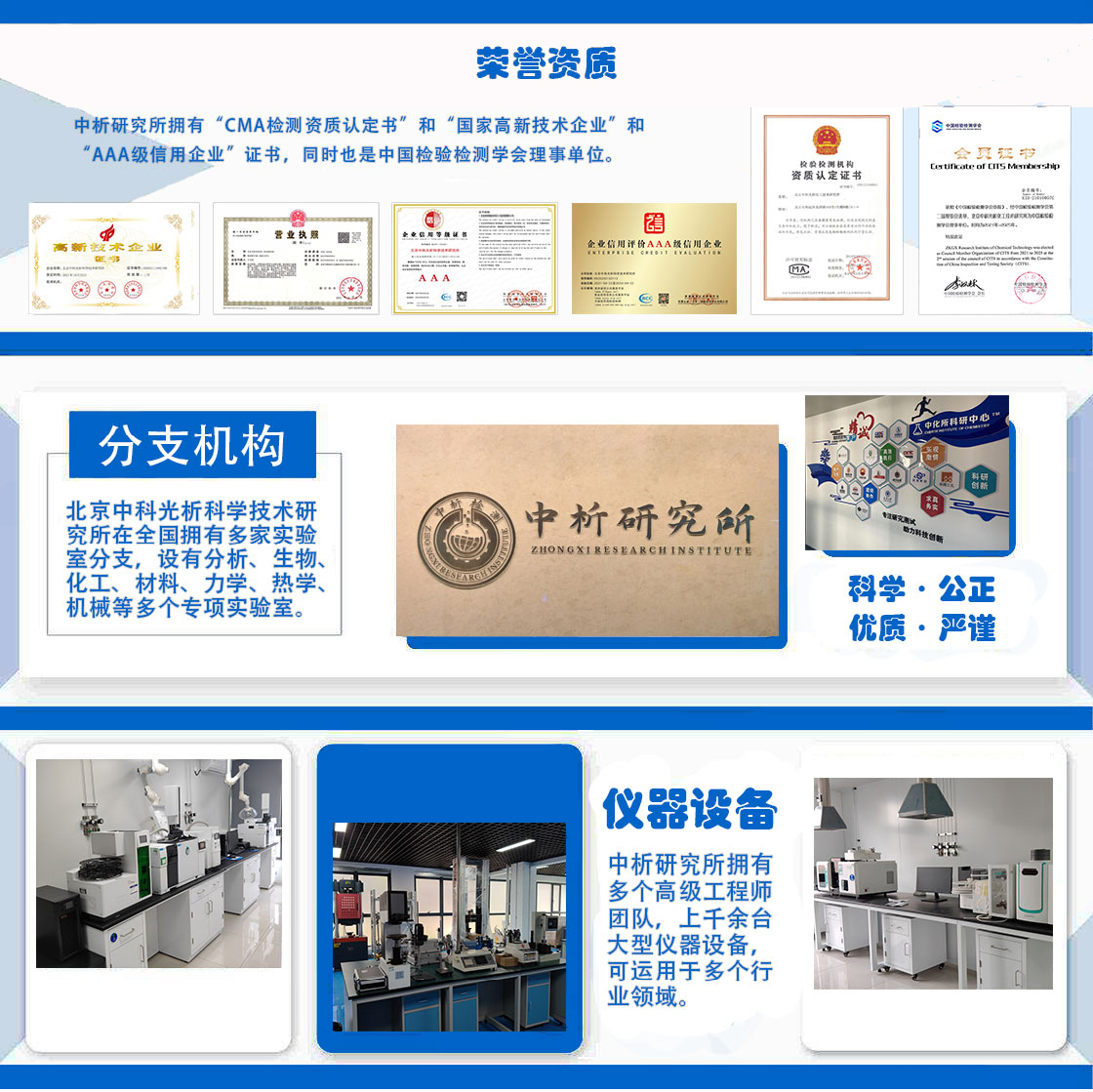
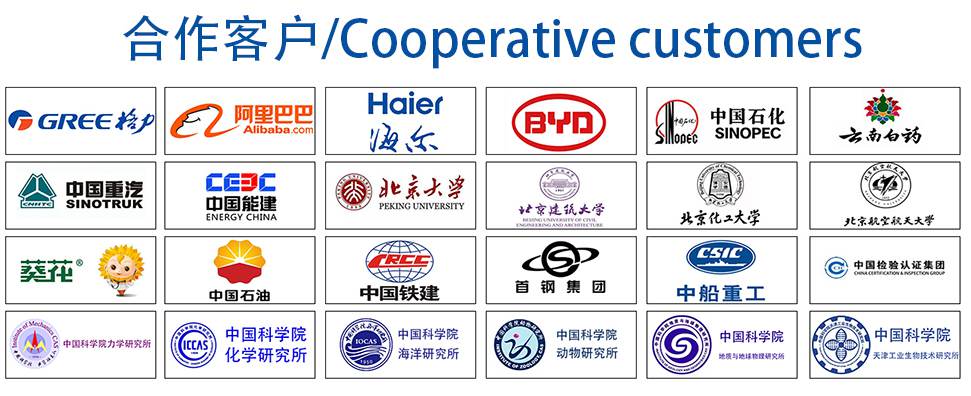