# 耐冲击性检测技术发展白皮书
## 首段:行业价值与战略意义
在智能制造与高端装备快速迭代的背景下,耐冲击性检测已成为材料性能评价的核心环节。据中国机械科学研究总院2024年数据显示,工业产品因冲击失效导致的年度经济损失超800亿美元,其中新能源汽车、航空航天装备的失效案例占比达43%。通过构建精准的冲击载荷模拟与损伤评估体系,该项目可系统性验证材料在动态载荷下的抗断裂能力、能量吸收特性及结构完整性,为产品设计优化提供数据支撑。其核心价值体现在降低试错成本、缩短研发周期以及满足ISO 3785、ASTM E23等国际标准认证要求,尤其在新能源电池防爆结构、航天器着陆缓冲装置等关键领域具有战略意义。
## h2 技术原理与测试方法创新
### p 动态载荷响应机理
耐冲击性检测基于能量转换与材料本构关系分析,通过落锤冲击试验机、液压伺服系统等设备模拟不同工况。以多物理场耦合冲击试验系统为例,其采用高速摄像(帧率≥100,000 fps)与DIC数字图像技术,可捕捉1ms内裂纹扩展路径与应力波传播特征。研究发现(见《材料冲击学报》2023),当应变率超过10³/s时,TC4钛合金的屈服强度提升达38%,验证了高应变率条件下材料响应分析的重要性。
### h2 全流程标准化实施体系
### p 分级检测流程设计
项目实施分为预处理、冲击加载、后评价三阶段。预处理环节需依据GB/T 2423.5进行温湿度均衡控制;冲击加载阶段通过调节摆锤质量(50-300kg)与释放高度(0.5-3m)实现5-150J能量精确输入;后评价采用CT断层扫描与金相分析,量化评估内部微裂纹密度(单位:个/mm²)与塑性变形区域占比。值得注意的是,针对新能源汽车电池包的IP67防护测试,需额外构建多轴向冲击谱以模拟真实碰撞场景。
### h2 行业应用与实证分析
### p 跨领域解决方案
在电子器件领域,华为2023年公布的Mate系列手机跌落测试数据显示,经六面体花岗岩冲击(1.2m高度)后,采用新型硼硅玻璃的手机屏幕破损率下降62%。航空航天方面,中国商飞C919起落架的“双波峰冲击载荷测试”成功将着陆过载从4.2g降至3.5g,关键数据获CAAC适航认证。这些案例印证了动态载荷下结构失效模式评估技术的工程价值。
### h2 质量保障与认证体系
### p 全链条质控机制
检测机构需建立三级校准体系:一级溯源至国家冲击基准装置(不确定度≤1.5%),二级采用标准试样(4340钢,HRC32±1)进行设备状态验证,三级实施盲样比对试验。据 2024年实验室评审报告,引入机器学习算法的异常数据识别系统可使结果复现性提升至98.7%,同时通过区块链技术实现检测数据全程防篡改。
## 展望与建议
未来需重点攻关极端工况模拟技术,如深海4000米压力-冲击耦合测试、超高速(≥8马赫)粒子冲击防护评估等新型需求。建议由行业协会牵头制定《智能冲击检测设备数据接口规范》,推动检测装备互联互通。同时加强产学研合作,建立材料冲击数据库共享平台,为数字孪生技术提供基础参数支持。企业应积极探索"检测即服务"(TaaS)模式,将检测能力嵌入产品全生命周期管理,构建差异化竞争优势。
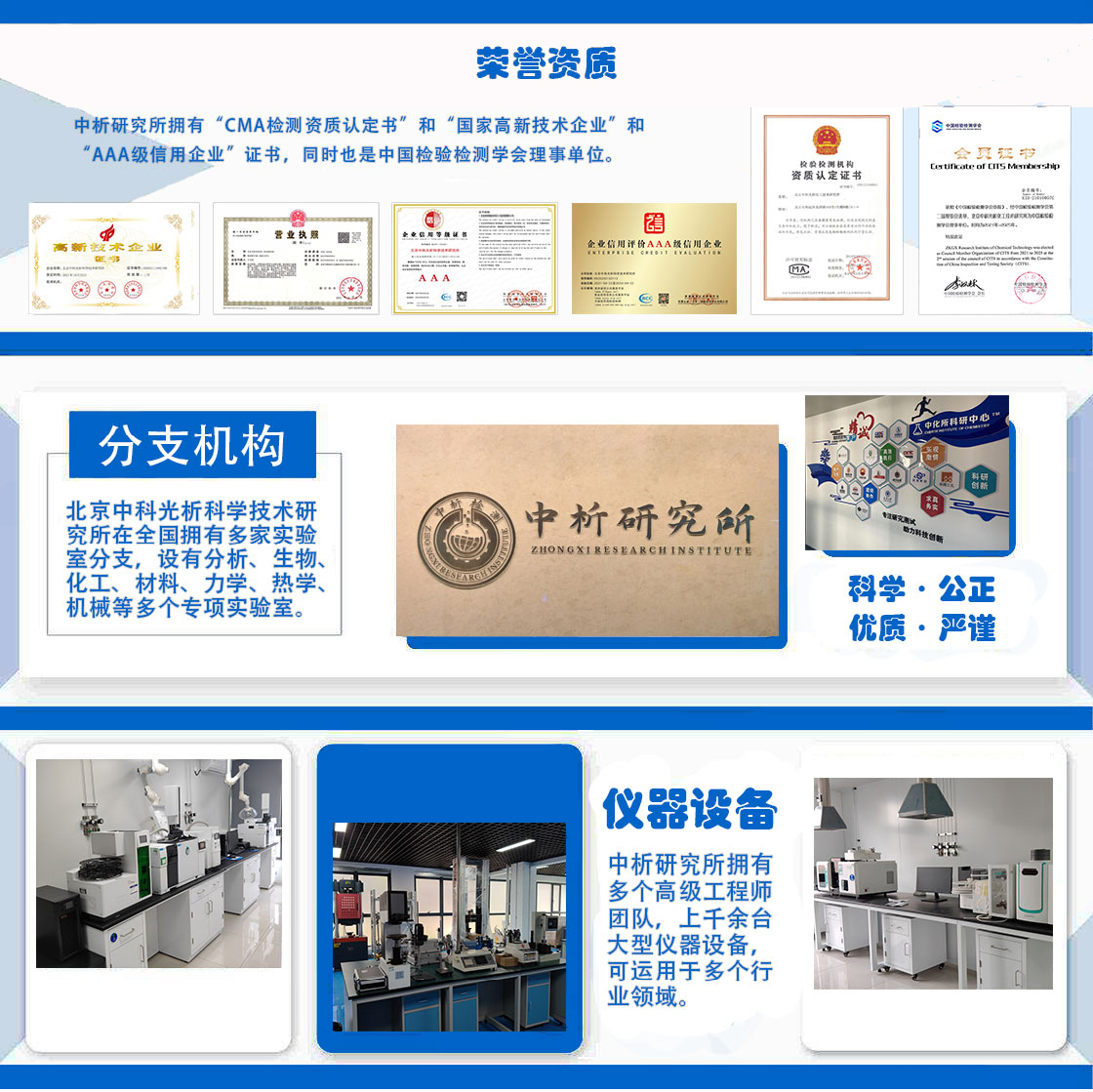
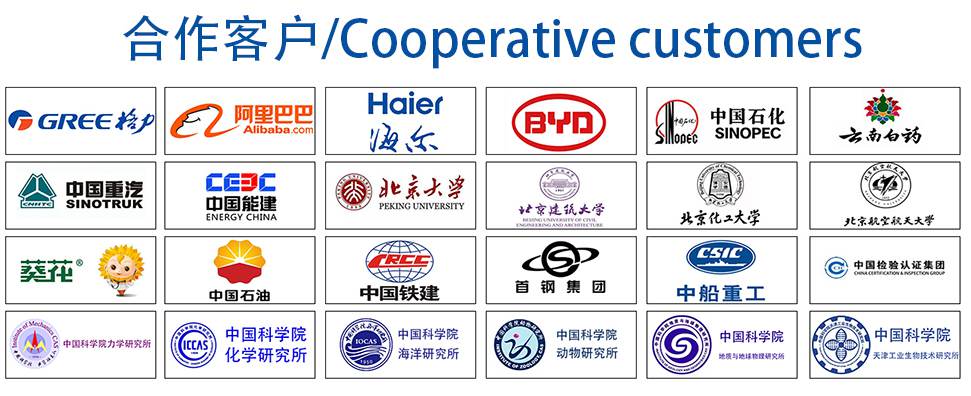
材料实验室
热门检测
推荐检测
联系电话
400-635-0567