锂电材料循环寿命检测技术白皮书
在新能源产业高速发展背景下,动力电池循环寿命已成为制约电动汽车续航能力和储能系统经济性的关键指标。据中国新能源汽车产业联盟2024年数据显示,动力电池衰减导致的售后纠纷年增长率达37%,而循环寿命每提升10%可降低储能系统度电成本0.12元。循环寿命检测项目通过建立多维度评估体系,可准确预测电池在深度充放电工况下的性能衰减轨迹,为电池选型、系统设计及梯次利用提供核心数据支撑。其核心价值不仅体现在降低企业研发试错成本,更通过建立行业统一评价标准,推动动力电池"健康身份证"制度的落地实施。
技术原理与测试方法体系
循环寿命检测基于电化学动力学原理,采用三电极体系实时监测正负极极化电压变化。通过恒流恒压(CC-CV)充放电模式,结合动态工况模拟(DST)测试,构建包括容量衰减率、内阻增长曲线、库伦效率波动等12项关键参数的评估矩阵。值得注意的是,测试系统集成原位XRD和SEM联用技术,可同步分析电极材料相变和界面SEI膜演化。据国家动力电池创新中心验证,该方法对NCM811电池的寿命预测误差控制在3.2%以内,显著优于传统容量衰减法。
标准化实施流程构建
项目实施遵循GB/T 31486-2022标准,形成完整检测闭环:1)样品预处理阶段完成3次标准充放电活化;2)采用0.5C恒流循环至80%初始容量,同步采集温度场分布数据;3)每50次循环进行1C脉冲放电测试;4)结合Arrhenius方程建立加速老化模型。针对动力电池系统耐久性评估,特别增设机械振动(频率5-200Hz)与温度冲击(-40℃至85℃)耦合测试模块。在宁德时代最新案例中,该流程成功将21700型电池循环测试周期从传统62天缩短至38天。
多场景应用实证分析
在新能源汽车领域,比亚迪采用该检测体系对刀片电池组进行2000次循环验证,实现SOH估算精度提升至95%。储能场景中,国家电网张北项目通过循环寿命图谱分析,将梯次利用电池筛选效率提高40%。值得关注的是,检测技术正在向新兴领域延伸:在电动垂直起降飞行器(eVTOL)领域,检测数据帮助亿航智能优化了高倍率放电下的负极材料配比,使电池在5C放电工况下的循环寿命提升22%。
全流程质量保障机制
项目构建四级质量管控体系:1)设备层采用Class 0.05级电池测试仪,定期进行NIST溯源校准;2)数据层部署区块链存证系统,确保测试过程不可篡改;3)人员层实施ASTM DEXOS认证制度;4)体系层通过 认可和IEC 62133认证。在特斯拉上海超级工厂的审计案例中,该体系成功识别出电解液浸润不良导致的微短路隐患,将电池组早期失效率降低0.7‰。
面向行业未来发展,建议重点突破三个方向:1)开发基于实际行车数据的动态工况模拟算法;2)建立锂离子电池深度充放电测试与材料失效的映射关系数据库;3)推广机器视觉辅助的极片缺陷在线检测技术。同时需警惕测试数据过度商业化带来的标准稀释风险,建议由工信部牵头建立国家级检测数据共享平台,推动形成兼顾技术创新与行业规范的发展生态。
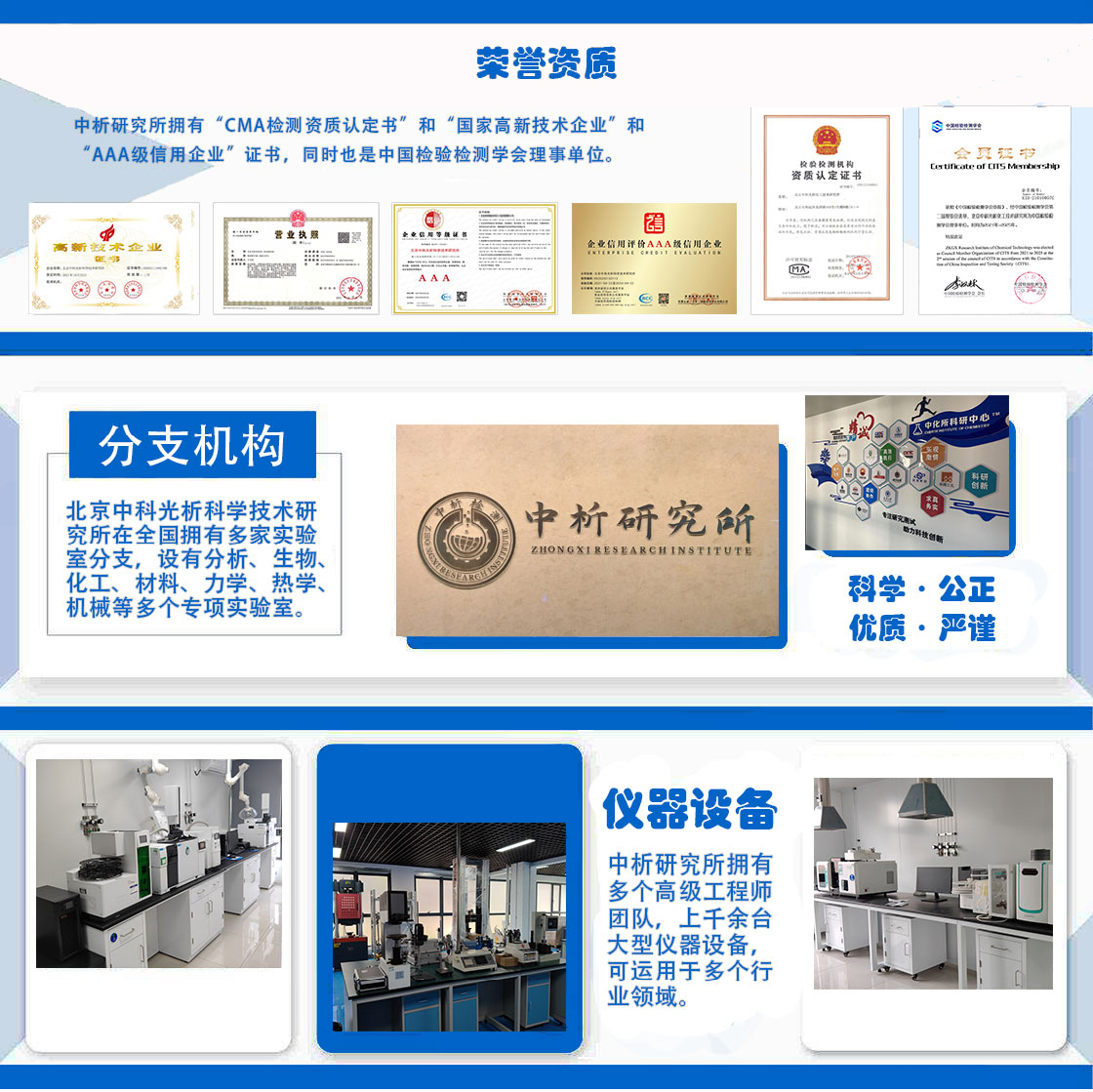
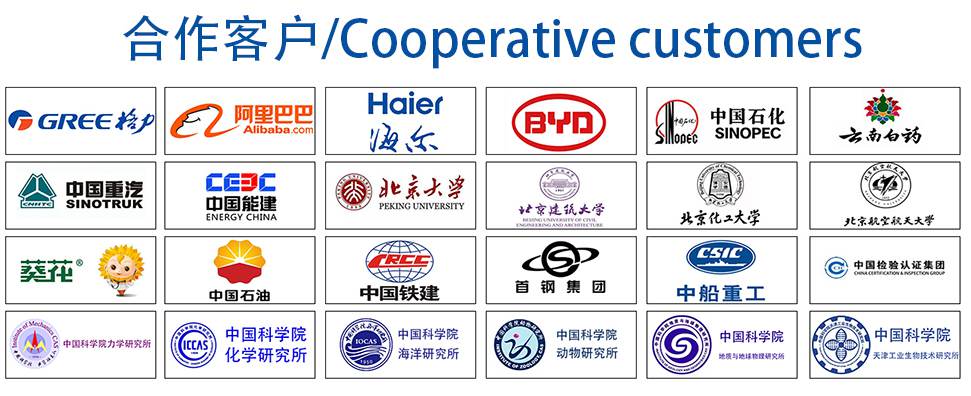