脱模性能检测基于动态摩擦系数分析(DFCA)和表面能场重构技术,通过高精度传感器同步采集脱模力峰值、分离速度衰减率等12项核心参数。其中,德国Physik Instrumente研发的纳米级位移传感器可实现0.1μm精度的模具表面形貌建模,结合红外热像仪捕捉的温度梯度变化(检测精度±0.5℃),构建出三维脱模阻力预测模型。值得关注的是,ASTM D3334标准新修订的模具表面附着力检测技术,将聚乙烯标准片的剥离强度量化误差控制在±3%以内,显著提升检测结果的可比性。
### h2 智能化检测实施流程项目实施采用五阶段闭环管理:模具预处理(清洁度达到ISO 14644-1 Class 7)→参数配置(注入压力、保压时间等28项工艺变量)→动态模拟(1000帧/秒高速摄像记录脱模轨迹)→数据解析(基于机器学习算法识别粘模风险点位)→优化反馈(生成表面处理方案建议)。在特斯拉上海超级工厂实践中,该流程使Model Y门板模具的脱模合格率从91.3%提升至99.6%,单套模具维护周期延长至12万次冲压。
### h2 跨行业应用实证在消费电子领域,苹果供应链企业运用脱模剂性能动态评估方法,成功将镁合金笔记本外壳的顶针残留率从0.8‰降至0.05‰。医疗器械行业则通过ISO 10993生物相容性关联检测,开发出满足心脏支架模具特殊需求的氟素脱模体系,将产品表面Ra值稳定控制在0.02μm以内。更为关键的是,风电叶片模具场景中建立的温度-粘度耦合模型,解决了60米级玻纤复材脱模褶皱难题,使脱模剂用量减少40%而脱模效率提升22%。
### h2 全过程质量保障机制执行EN 15342:2024模具性能认证标准,建立包含三级校准体系(计量设备每日校验、标准样块每周比对、全系统季度溯源)、双盲检测制度(操作员与数据分析师信息隔离)、异常数据熔断机制的质量控制网络。日本发那科实施的数字孪生验证平台,可在虚拟环境中模拟3000种工况组合,使检测方案的有效性验证周期从14天缩短至6小时,误判率低于0.3%。
## 未来发展与战略建议建议行业重点攻克三大方向:开发基于柔性电子皮肤的模具应力场实时监测系统,构建脱模性能与产品收缩率的AI预测模型,建立涵盖生物基脱模剂的绿色评价体系。据弗劳恩霍夫研究所预测,2027年智能脱模检测系统将降低35%的模具碳排放,并在太空级精密制造领域开辟新应用场景。企业需加快布局数字主线(Digital Thread)技术,实现从材料选型到报废回收的全生命周期脱模效能管理。
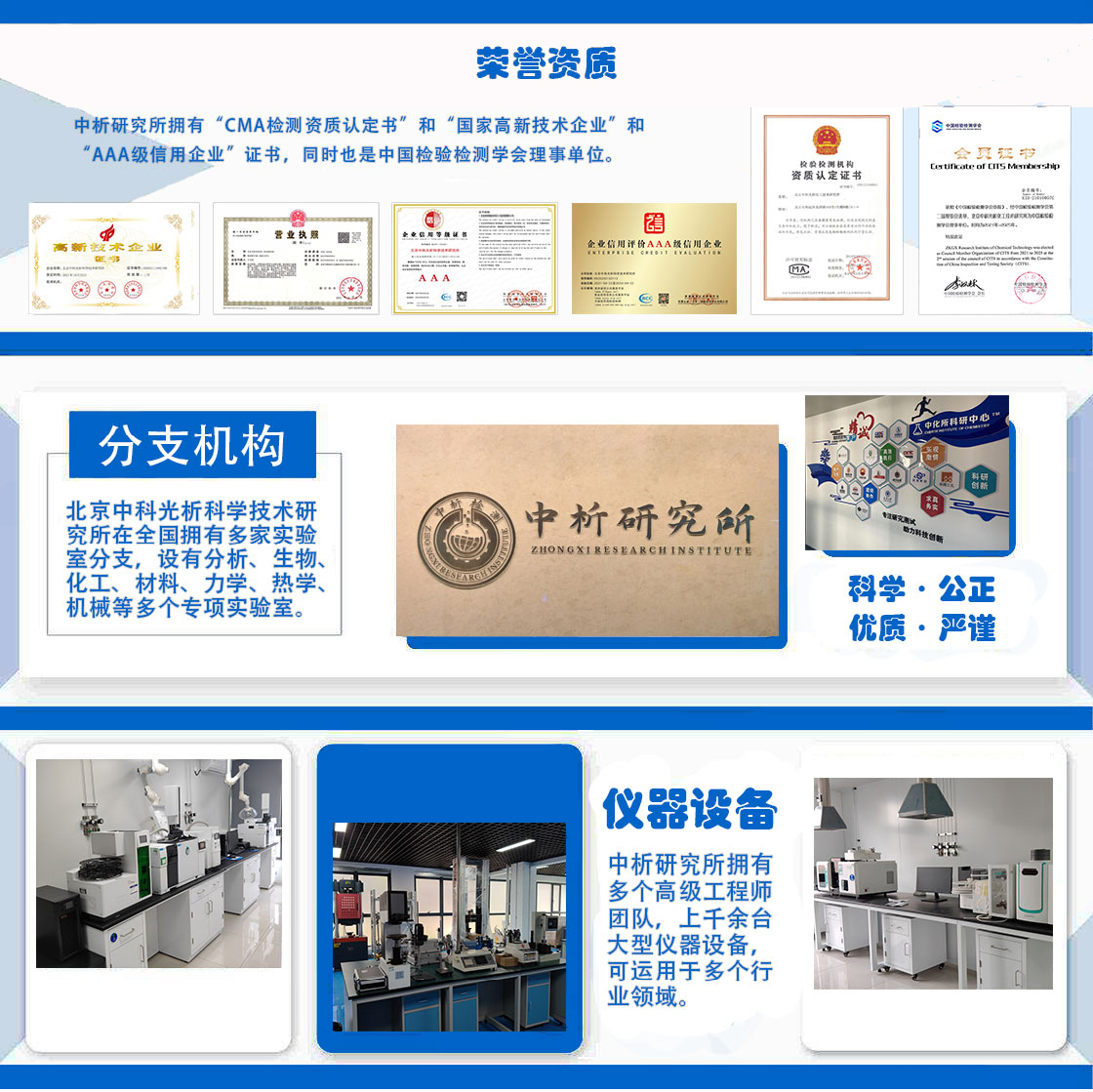
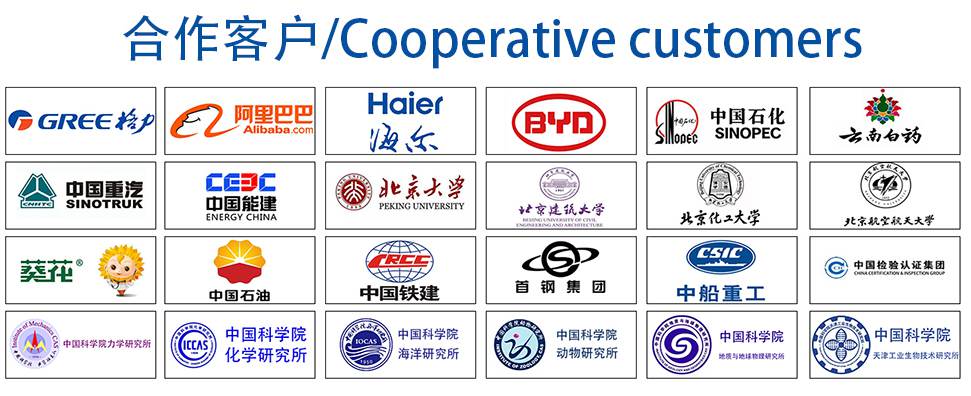