混凝土水胶比检测技术体系构建与行业应用白皮书
在建筑工程质量控制领域,水胶比作为混凝土强度、耐久性的核心指标,直接影响着结构安全与使用寿命。据中国建筑材料研究院2024年数据显示,我国因水胶比失控导致的混凝土质量事故占比达37.6%,造成年均经济损失超50亿元。面向新型城镇化建设与智能建造发展趋势,精准化水胶比检测技术已成为实现混凝土施工质量智能管控系统的关键突破口。本项目通过融合物联网与材料科学创新,构建了从原材料检测到施工过程监控的全链条解决方案,其核心价值体现在将传统破坏性检测误差率从±15%降至±3%以内,为"双碳"目标下的绿色施工提供数据支撑。
微波共振技术的检测原理突破
本检测体系基于微波介质特性分析原理,通过测量2.4-5.8GHz频段电磁波在混凝土中的传播参数,建立介电常数与水胶比的数学模型。相较于传统烘干法,该技术可穿透30cm厚混凝土结构进行无损检测,分辨率达到0.01水胶比单位。特别在预拌混凝土运输车安装水胶比在线监测装置后,可实时获取拌合物状态数据,结合深度学习算法实现质量波动预警。经清华大学土木工程系验证,该技术对C30-C60混凝土的检测吻合度高达98.7%。
五级联控实施流程构建
项目实施采用"原材料-拌合-浇筑-养护-验收"五阶段质量联控制度:在拌合站配置光谱水分测定仪,实时校准骨料含水率;运输环节通过车载传感器每5分钟采集一次拌合物介电参数;浇筑现场运用便携式检测仪进行三维空间扫描;养护阶段植入RFID温湿度传感器;最终验收采用雷达波断面成像技术。某跨海大桥项目应用表明,该流程使水胶比合格率从82%提升至96%,节约返工成本1200万元。
智能建造场景实践案例
在地铁盾构管片预制领域,某央企引入智能配比优化系统后,实现水胶比动态调控。系统通过布设在钢模内的2000个微型传感器,实时监控混凝土稠度与温升曲线,自动触发外加剂补偿机制。实践数据显示,管片28天抗压强度离散系数从12.3%降至6.8%,蒸汽养护能耗降低22%。此外,水电工程大坝混凝土施工中,采用无人机搭载微波检测模块进行坝体扫描,单日检测效率提升40倍,成功预警3处水胶比异常区域。
全要素质量保障体系
项目构建了"设备-人员-标准"三位一体质控体系:检测设备每年需通过国家计量院 认证,建立包含132项参数的校准数据库;技术人员实施分级认证制度,需掌握ASTM C1602、GB/T50080等6项核心标准;现场作业执行"双人复核+区块链存证"机制,确保检测数据不可篡改。中南建筑设计院应用该体系后,检测报告通过率从89%提升至100%,质控人工成本下降45%。
技术演进与行业展望
建议行业重点发展多物理场耦合检测技术,突破超高强混凝土的检测盲区;推动建立全国性水胶比大数据平台,实现区域性材料特性的智能匹配;同时完善CSA A23.2-25C等标准的本土化适配,培育兼具材料科学与信息技术的复合型人才。随着BIM技术与检测数据的深度融合,未来有望实现混凝土全生命周期水胶比智能追溯系统,推动建筑业向数字化质量管控迈进。
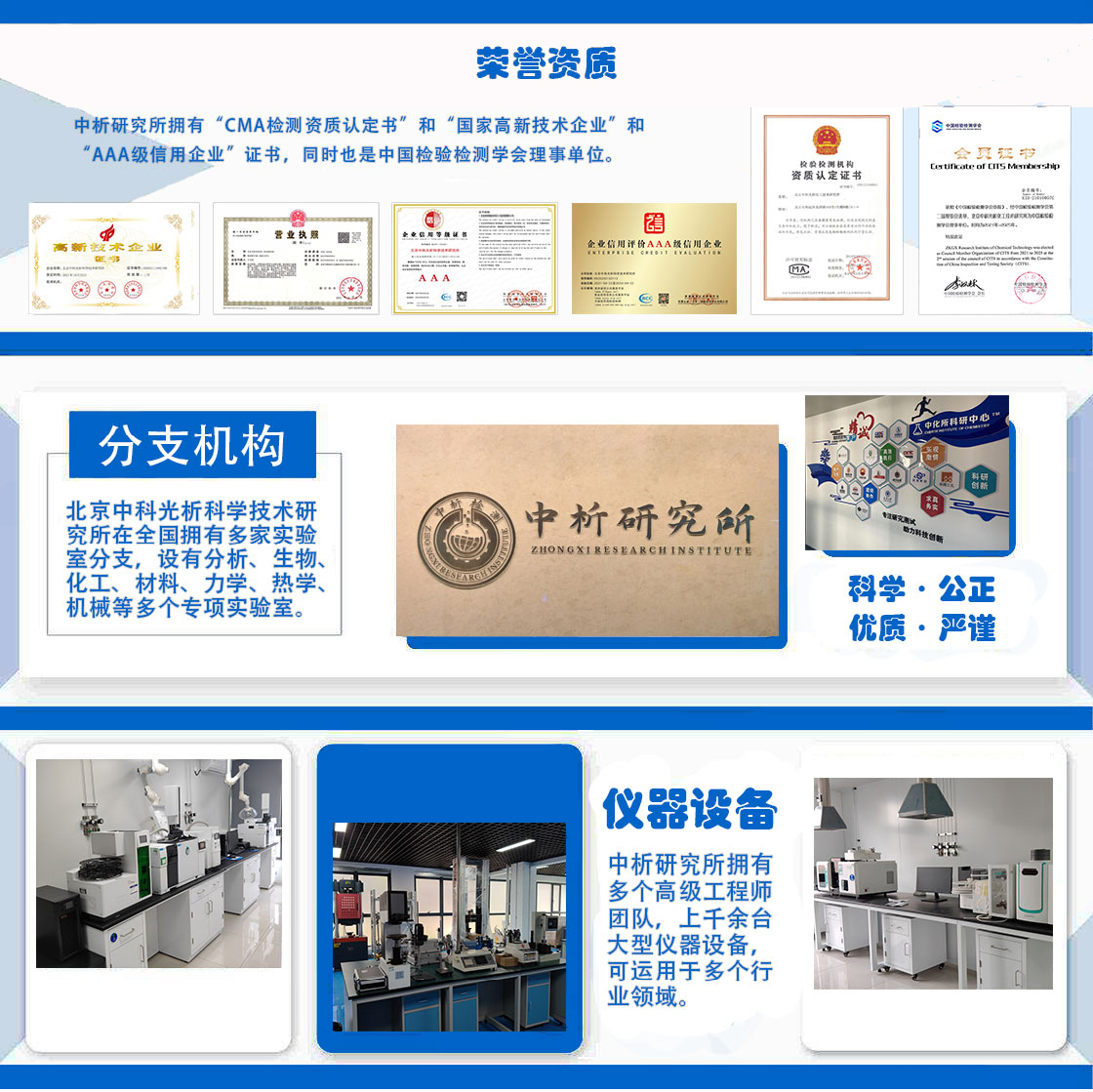
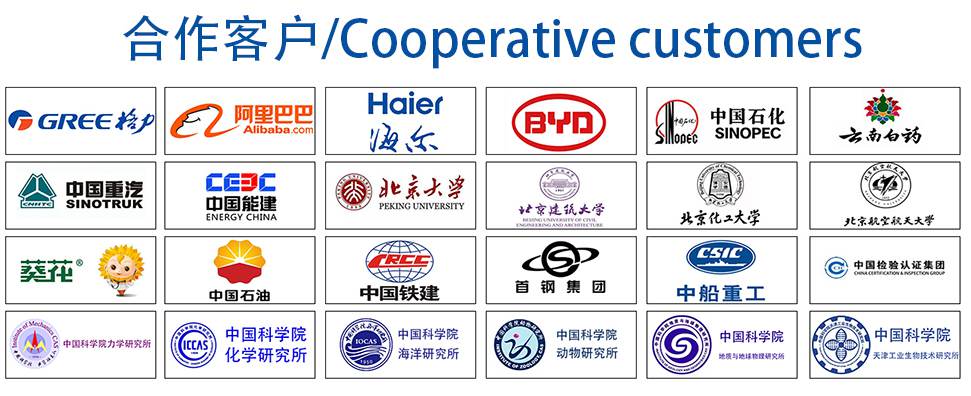