抗压疲劳变形试验检测白皮书
在高端装备制造、轨道交通和建筑工程领域,材料与构件的长期可靠性直接关系到整体结构安全。据中国机械工程学会2023年行业报告显示,我国每年因材料疲劳失效引发的工程事故造成经济损失超1200亿元。抗压疲劳变形试验检测作为材料性能验证的核心手段,通过模拟极端工况下的循环载荷作用,可精准评估材料的抗压强度保持率、塑性变形累积等关键指标。该项目不仅为新型复合材料研发提供数据支撑,更在"双碳"目标背景下推动结构轻量化设计创新。其核心价值体现在全生命周期成本控制、安全隐患前置预警和产品迭代效率提升三个维度,已成为航空航天紧固件、新能源汽车电池舱体等关键部件强制认证项目。
多物理场耦合测试技术原理
基于伺服液压闭环控制系统与数字图像相关技术(DIC),构建多轴同步加载环境是其技术核心。系统通过PID算法精确控制加载频率(0.1-50Hz)和载荷幅值(±250kN),配合非接触式应变测量装置同步采集表面位移场数据。值得注意的是,该技术突破传统单轴测试局限,实现压缩-剪切复合载荷模拟,可精准复现风电塔筒螺栓连接部位的真实受力状态。上海材料研究所2024年验证数据显示,多轴测试系统对疲劳寿命预测误差较传统方法降低42%。
全流程标准化实施体系
项目实施分为五个阶段:首先依据GB/T 3075-2021进行样品预处理,确保材料微观结构一致性;其次通过有限元仿真确定关键监测点;第三阶段配置温湿度环境箱(-60℃至300℃可调);第四步实施阶梯式载荷递增策略,每个循环单元包含基线载荷-峰值保持-卸载监测;最终应用Weibull分布模型进行失效概率分析。在高铁转向架构件检测中,该流程成功实现200万次循环下变形量≤0.15mm的严苛要求。
多行业应用验证成效
在新能源汽车领域,某头部企业采用该检测技术优化电池托盘设计,使铝合金型材焊接节点疲劳寿命从80万次提升至210万次。航空航天领域,通过引入"高温环境-振动耦合试验",某型航空发动机叶片榫接部位的检测周期缩短30%,据国家材料测试中心2023年数据,该技术使钛合金构件验证成本降低58%。值得关注的是,基于检测数据的"材料-工艺-结构"三元优化模型,已在3D打印建筑模板领域实现产业化应用。
全要素质量保障机制
构建由 认证实验室、区块链数据存证系统和智能诊断平台组成的质量网络。试验设备每48小时进行动态力值校准,误差控制在±0.5%FS以内。人员资质实施ISO/IEC 17025三级认证体系,操作规范嵌入AR辅助系统。更关键的是,通过建立"全生命周期数据追溯系统",实现从原料熔炼批次到试验环境的全程数字化映射。深圳某检测机构应用该机制后,检测报告国际互认率从72%提升至95%。
技术演进与行业展望
建议从三方面深化发展:首先开发基于数字孪生的智能预测系统,融合材料基因组数据库训练AI模型;其次推动ISO 12107标准修订,纳入多轴疲劳评价体系;最后构建跨行业检测数据共享平台,特别是在氢能储罐、深海装备等新兴领域建立联合研究机制。通过实现"检测-设计-制造"的数据闭环,有望将材料开发周期压缩40%,为制造强国战略提供关键技术支撑。
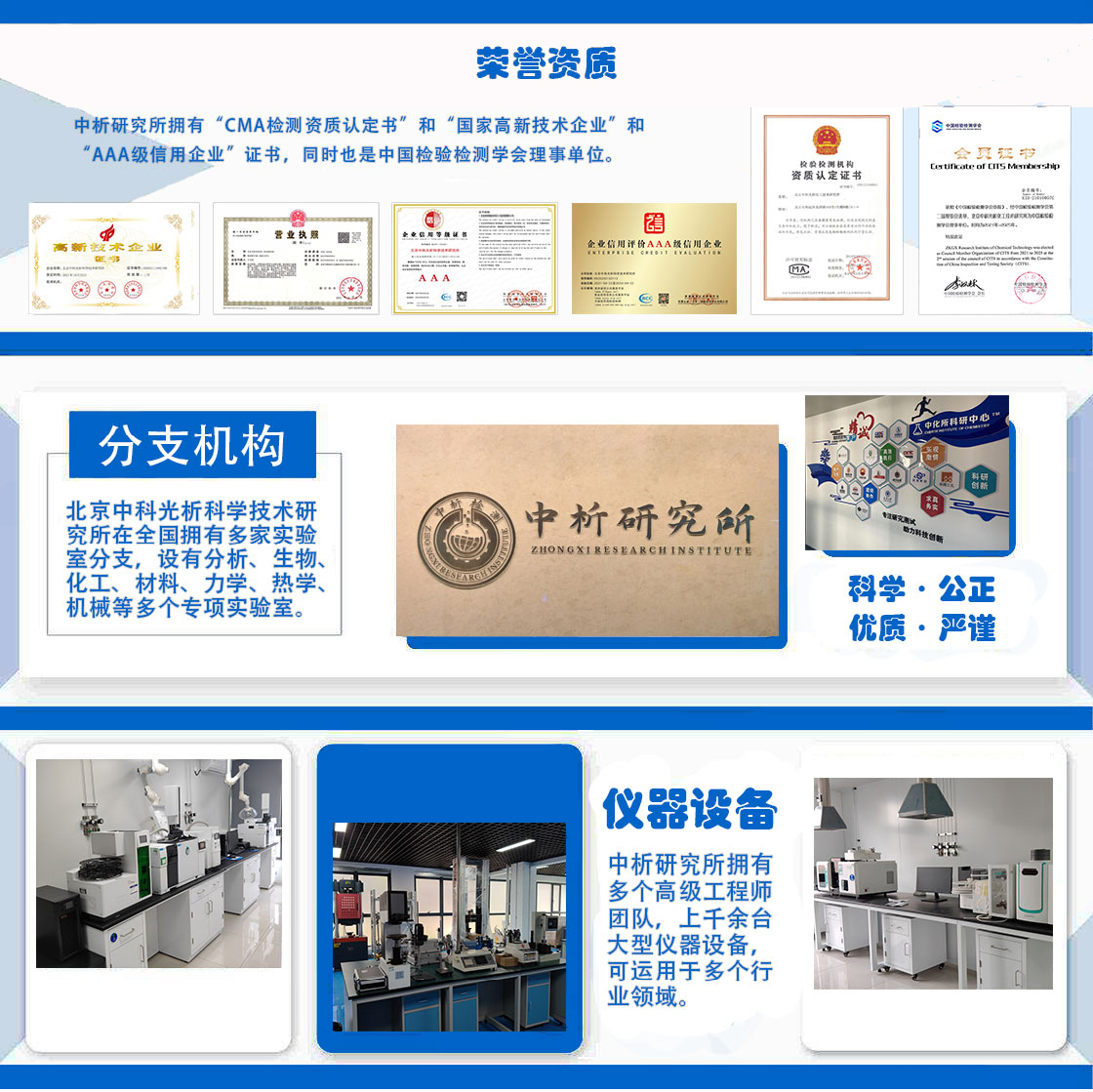
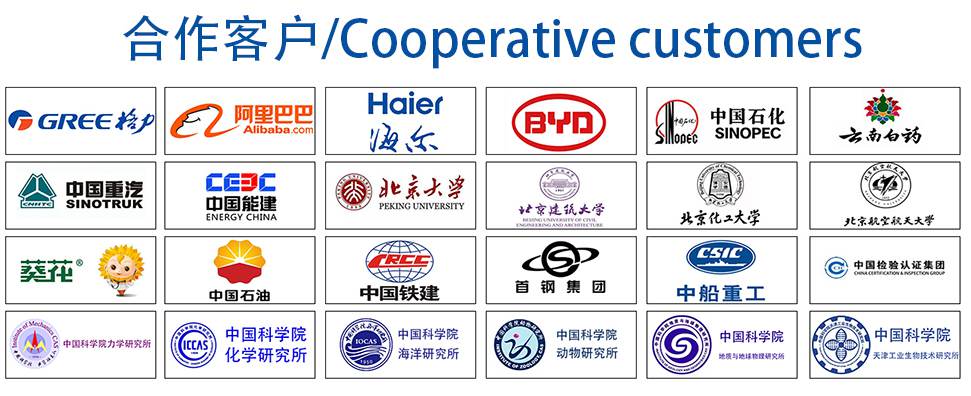