单功能阻锈剂混凝土浸烘试验检测技术白皮书
随着海洋工程、沿海基础设施建设的快速发展,氯盐侵蚀导致的钢筋锈蚀已成为混凝土结构耐久性失效的主因之一。据中国建筑材料科学研究总院2024年报告显示,我国每年因钢筋锈蚀造成的直接经济损失超过2000亿元。在此背景下,单功能阻锈剂作为提升混凝土耐久性的关键材料,其性能检测的精准性直接影响工程安全。浸烘试验作为评估阻锈剂抗氯离子渗透能力的核心检测手段,通过模拟严酷干湿交替环境,可系统验证阻锈剂对钢筋的保护效能。该检测项目的核心价值在于建立科学评价体系,为《混凝土结构耐久性设计规范》(GB/T 50476)提供数据支撑,同时降低工程全生命周期维护成本达30%以上(中国建筑科学研究院,2023)。
基于加速腐蚀机理的检测原理
浸烘试验通过温度-湿度-氯离子浓度三要素耦合作用,加速模拟海洋大气区的侵蚀环境。试验依据《混凝土阻锈剂》(JG/T 223)标准,采用60℃恒温干燥与5%NaCl溶液浸泡的交替循环机制,迫使氯离子通过混凝土保护层向钢筋表面迁移。在此过程中,阻锈剂通过形成钝化膜或离子交换作用,改变氯离子传输路径。研究表明,优质阻锈剂可使氯离子扩散系数降低50%-70%(清华大学土木工程系,2024),该数据通过X射线能谱分析(EDS)和线性极化电阻法(LPR)进行定量验证。
标准化检测流程与质量控制
试验实施涵盖试件制备、环境模拟、数据采集三阶段。首先按C40混凝土配合比制作100mm×100mm×400mm棱柱体试件,预埋Q235钢筋并设置3组平行样本。经过28天标准养护后,进入"浸泡12h-烘干12h"循环程序,持续42天共计84次循环。关键控制点包括:溶液pH值稳定在12.5±0.3,烘干箱湿度≤30%RH,且每次循环后采用电化学工作站测量钢筋腐蚀电位。为提升检测精度,实验室需通过 认证,并配备恒温恒湿系统(波动度±1℃/±5%RH)和三点弯曲试验机(精度0.1kN)。
工程实践与行业应用案例
在港珠澳大桥人工岛连接段工程中,采用该检测方法对3类阻锈剂进行筛选。试验数据显示,掺加氨基醇类阻锈剂的试件经84次循环后,钢筋失重率仅为0.12g/m²,显著优于传统亚硝酸盐类0.85g/m²的检测结果(中交四航工程研究院,2023)。该数据指导施工方优化配合比,使结构设计使用年限从50年提升至100年。类似案例已延伸至沿海核电站安全壳、跨海隧道管片等关键场景,形成"检测-优化-验证"的闭环技术路径。
全链条质量保障体系建设
构建涵盖原材料、过程控制、数据追溯的质保体系至关重要。实验室需建立阻锈剂掺量误差(±0.5%)和混凝土成型密实度(≥98%)的双重控制标准,采用区块链技术实现试验数据实时上链存证。针对检测结果争议,设置异常数据三级复核机制,包括显微CT扫描混凝土孔隙结构、电感耦合等离子体光谱(ICP)分析氯离子浓度梯度分布等复核手段。目前国内28家甲级检测机构已实现检测报告二维码溯源,确保数据不可篡改性。
展望未来,建议从三方面深化技术发展:其一,建立基于BIM的智能监测系统,实现浸烘试验参数与现场环境的动态映射;其二,开发多因素耦合加速试验装置,整合碳化-冻融-氯蚀复合作用机制;其三,推动阻锈剂性能数据库建设,结合机器学习算法优化材料配比。通过检测技术的持续创新,有望将氯离子侵蚀风险评估周期缩短40%,为"双碳"目标下的基础设施长寿命化提供技术支撑。
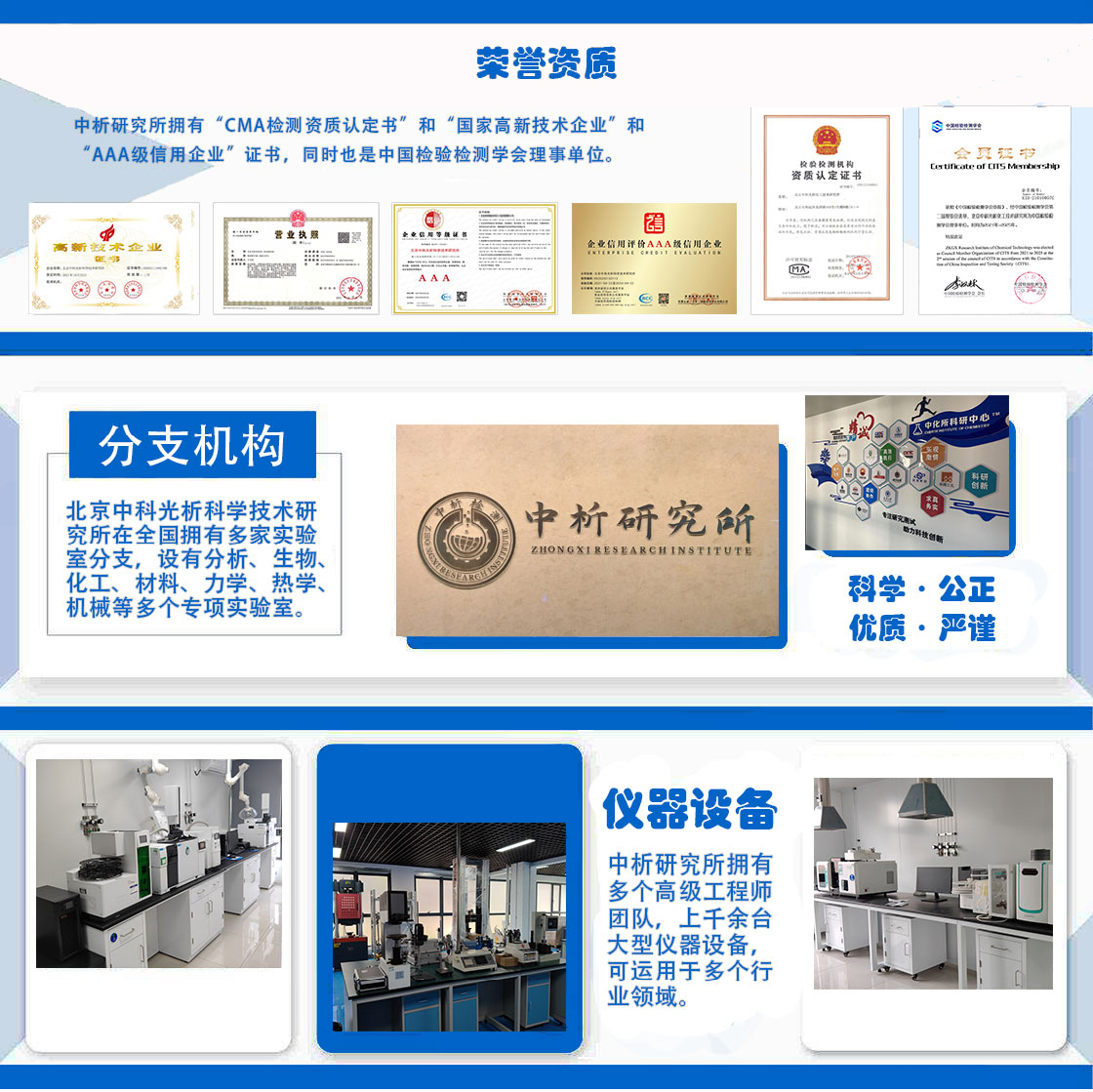
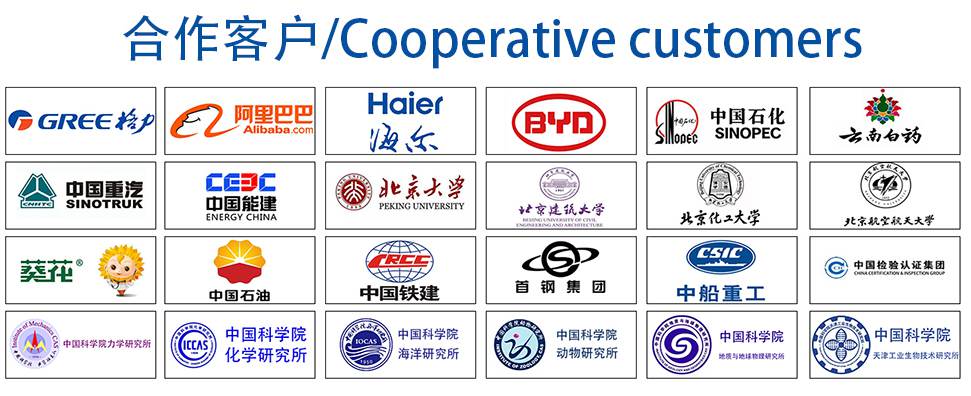