混凝土拌和物拌和均匀性试验检测技术白皮书
在基建工程高速发展的背景下,混凝土作为核心建筑材料,其拌和质量直接影响结构安全与服役寿命。据中国建筑材料研究院2024年行业报告显示,因拌和不均匀导致的混凝土强度离散度超标案例占比达12.7%,造成的年经济损失超过80亿元。拌和均匀性检测通过量化评估骨料分布、浆体包裹度等关键指标,可有效预防蜂窝麻面、强度分层等质量缺陷。该技术的核心价值在于建立从生产到施工的全流程质量监控链,为高性能混凝土制备提供科学依据,特别是在高速铁路轨道板、大坝碾压混凝土等精密工程中具有不可替代的管控作用。
技术原理与检测方法创新
基于电阻率法的拌和均匀性检测技术,通过分析混凝土三相介质的导电特性差异,建立介电常数与物料分布的相关模型(符合GB/T 50080标准)。采用双通道高频信号采集系统,可同步获取拌和物宏观均匀度与微观包裹度数据,分辨率达到±0.5%。相较于传统筛分法,该技术突破性地实现了无损、实时检测,检测周期由45分钟压缩至8分钟,满足搅拌站连续生产的质量控制需求。
全流程标准化实施体系
检测流程分为取样规范、数据采集、模型解析三个阶段。在高铁CRTSⅢ型轨道板生产场景中,技术人员需在搅拌车卸料初期、中期、后期分三次取样,每次取6个等间距截面样本。通过便携式均匀度分析仪获取三维介电图谱后,经神经网络算法计算得出均匀性系数(K值)。据中铁十七局项目数据显示,该体系使轨道板混凝土强度标准差由4.8MPa降至2.3MPa,达到《铁路混凝土工程施工质量验收标准》TB10424的A级要求。
行业典型应用场景分析
在乌东德水电站大坝工程中,针对碾压混凝土VC值波动问题,项目团队采用拌和均匀性-振动压实度联合控制方案。通过植入RFID芯片的智能骨料追踪技术,精准定位搅拌车卸料过程中的物料离析区域。实际监测数据显示,经优化后的拌和工艺使粗骨料分布变异系数从18.6%降至9.4%,碾压层间结合强度提升27%,成功攻克了百米级大坝的层间抗剪难题。
四维质量保障系统构建
检测体系建立设备、人员、环境、数据的闭环管控机制:①计量器具执行JJF 1309校准规范,每季度进行介电参数溯源;②操作人员需通过CMA认证的混凝土检测专项考核;③试验环境温度控制在(20±2)℃,湿度≤65%RH;④运用区块链技术实现检测数据全程上链存证。某特大桥项目应用表明,该体系使检测报告通过率从82%提升至98%,数据追溯响应时间缩短83%。
技术发展趋势与行业建议
面向智能建造发展需求,建议从三方面深化技术应用:①开发集成5G传输的在线监测装置,实现搅拌站与施工现场数据互联;②建立区域性混凝土均匀性数据库,利用机器学习优化配合比设计;③推动《超高性能混凝土拌和均匀性评价规范》等标准编制。通过融合物联网与材料信息学,有望在2030年前将重大工程混凝土质量事故率控制在0.3‰以下,为新型建筑工业化提供关键技术支撑。
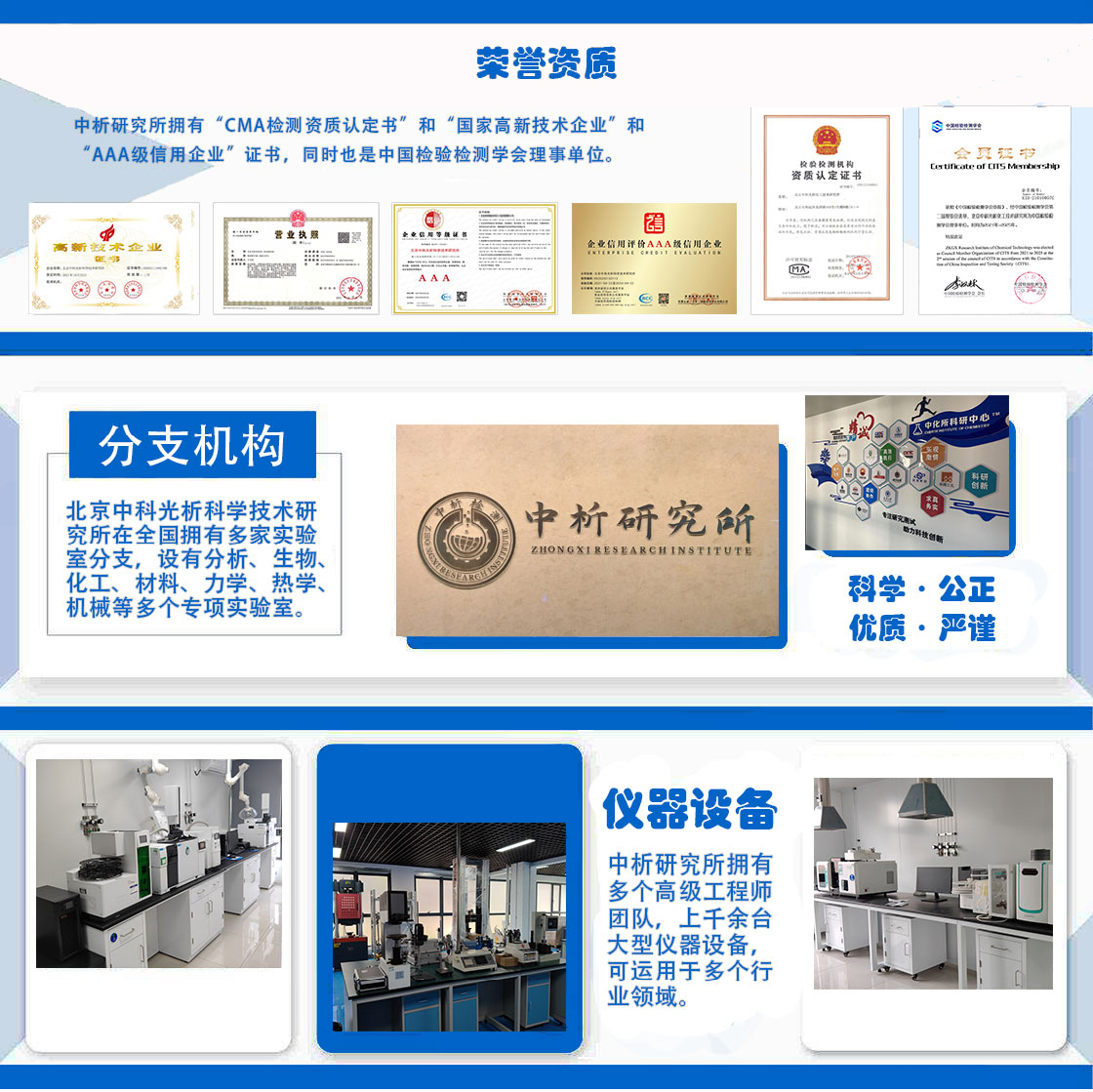
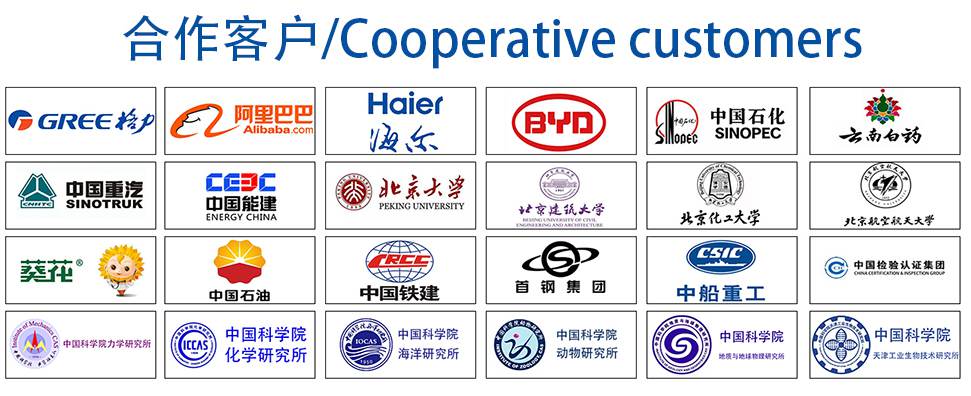