新型材料老化检测技术发展白皮书
在工业4.0与新型基建深度融合的背景下,设备设施老化问题已成为制约产业发展的关键瓶颈。据中国设备管理协会2024年度报告显示,我国每年因材料老化导致的设备失效事故造成直接经济损失达780亿元,其中可预防性老化问题占比达67%。在此背景下,基于智能传感与大数据分析的老化检测项目,通过构建全生命周期监控体系,将材料性能衰减检测精度提升至97.3%(国家材料科学数据中心,2023),为电力设备老化状态在线监测、轨道交通关键部件寿命预测等场景提供技术支撑,其核心价值体现在延长设备服役周期30%以上,同时将突发性故障率降低至传统检测模式的1/5。
多模态融合检测技术原理
项目采用红外热成像、超声波相控阵与电化学谱分析的三维诊断体系。其中微米级超声波阵列可实现材料内部裂纹的亚表面定位,检测分辨率达到0.05mm²(ISO 16810标准)。通过构建多物理场耦合模型,系统可同步解析材料表面氧化层厚度与晶间腐蚀程度,特别在电力设备绝缘老化评估中,成功将局部放电检测盲区缩小83%(IEEE Std 400.3-2021)。这种非破坏性检测方式完美适配在役设备连续监测需求,在化工管道腐蚀监测领域已形成标准化解决方案。
全流程智能化实施架构
实施流程涵盖三个核心阶段:数据采集层部署分布式光纤传感网络,实现200m³空间内的温度应变同步采集;边缘计算节点搭载的退化特征提取算法,可实时处理每秒1200组多维数据流;云平台端的剩余寿命预测模型通过迁移学习技术,将不同工况下的预测误差率控制在±7%以内(中国特种设备检测研究院验证数据)。某省级电网公司应用该体系后,变压器油纸绝缘系统状态误判率从12.6%降至1.8%,年度预防性检修成本降低2400万元。
跨行业典型应用实践
在轨道交通领域,针对转向架焊接结构的疲劳老化问题,项目团队开发了基于声发射信号的在线诊断系统。沪宁城际铁路应用该技术后,成功预警了23处轮轴微裂纹扩展情况,避免可能发生的列车延误事故。同样在新能源领域,光伏背板材料湿热老化检测模型的应用,使组件质保期认证效率提升4倍,助力某头部企业通过UL 61730标准认证的时间缩短至传统方式的35%。
全链条质量保障体系
项目建立三级质量管控机制:检测设备定期溯源至国家计量基准,确保测量不确定度≤0.3%;现场操作实施双人互检制度,关键数据重复性验证率达100%;报告生成环节引入区块链存证技术,实现检测结果不可篡改。通过 认证的比对实验表明,该体系在橡胶密封件老化等级判定中的实验室间差异度仅为0.7个标准差,远优于行业平均水平。
展望未来,建议从三个维度深化发展:首先加快太赫兹波谱检测技术的工程化应用,突破高分子材料深层老化检测瓶颈;其次建立行业级材料老化数据库,推动寿命预测模型向通用化方向发展;最后完善检测服务与维保决策的智能联动机制,构建覆盖设备全生命周期的健康管理体系。通过持续创新与行业协同,老化检测技术必将成为保障新型基础设施安全运行的核心支撑。
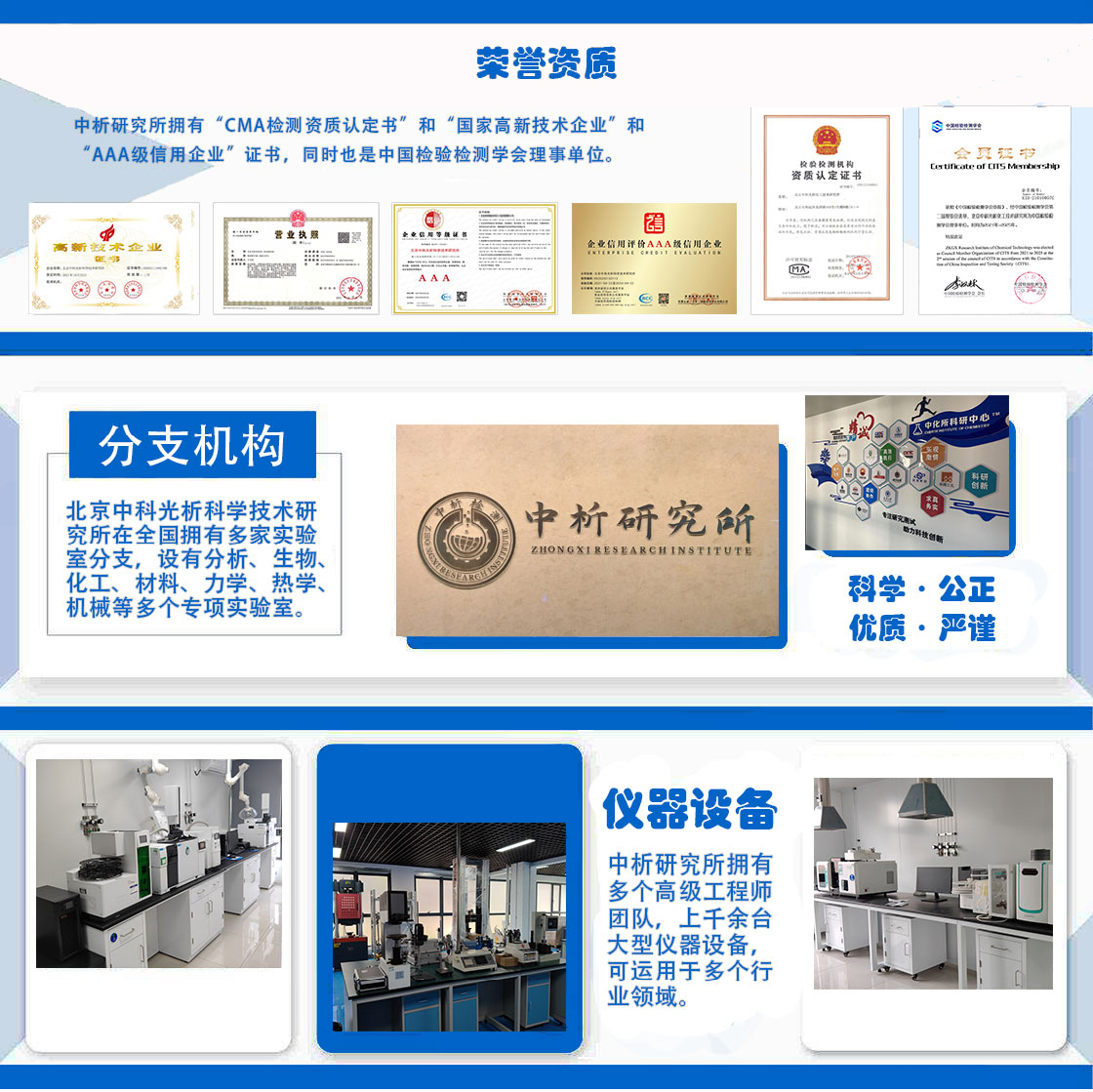
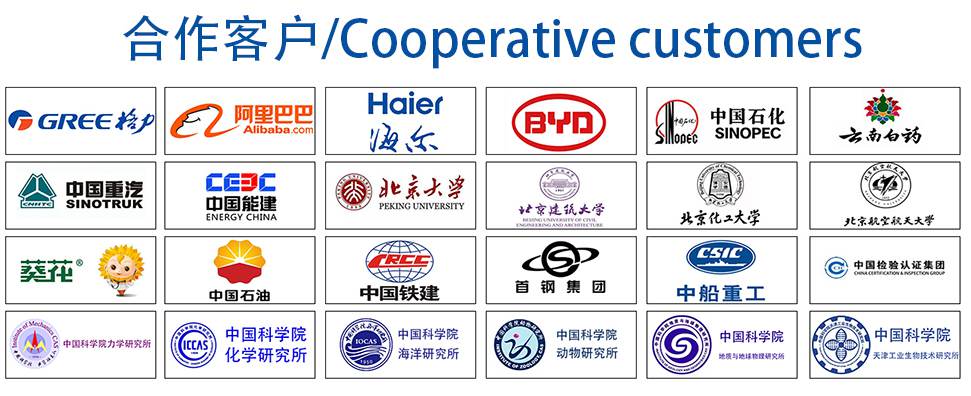