锡焊质量检测的行业价值与技术演进
在电子制造领域,锡焊作为PCB组装的核心工艺,其质量直接影响产品的可靠性和使用寿命。据国际电子工业联接协会(IPC)2024年报告显示,因焊接缺陷导致的电子产品失效案例年均增长17%,其中63%的故障源于可焊性不足和耐热性能缺失。随着5G通信设备微型化及车载电子高频化的发展,焊点需承受的温度循环范围已从-40~85℃扩展至-55~125℃,这对锡焊检测提出了更严苛的要求。建立完善的可焊性及耐焊接热检测体系,不仅可降低3.2%的售后返修成本,更能提升高频信号传输可靠性这一关键性能指标,为智能终端、新能源汽车等战略产业提供质量保障。
检测技术原理及工艺适配性
可焊性检测采用润湿平衡法(Wetting Balance Test)量化评估焊料扩散能力,通过测量润湿力-时间曲线,可精确计算出零交时间(T0)和最大润湿力(Fmax)两项核心参数。耐焊接热测试则依据J-STD-020标准构建热应力模型,采用回流焊模拟设备以3℃/s速率进行10次温度冲击,观测焊点微观结构变化。值得注意的是,针对无铅焊料(SAC305)与镀层材料(ENIG/OSP)的适配性,须建立差异化的检测规程。某国际汽车电子厂商通过引入动态热机械分析(DMA)技术,将热疲劳寿命预测准确度提升了41%。
全流程质量控制体系构建
标准检测流程包含三大模块:预处理阶段需在温度23±2℃、湿度45%RH条件下完成试样24小时平衡;检测执行环节采用模块化设计,既可实现批量样本的自动进样检测,又能支持BGA、QFN等异形器件的定制化测试;数据分析系统集成了机器学习算法,可自动识别焊点裂纹、缩孔等7类缺陷。在某军工级通信设备项目中,通过运用X射线断层扫描(CT)与金相分析联用技术,成功定位了0.12mm间距QFP器件的虚焊问题,使产品一次通过率从82%提升至97%。
行业应用场景与效能提升
消费电子领域,某手机制造商在新型折叠屏铰链焊接工艺开发中,运用梯度温度耐热测试(-40~150℃循环),筛选出最佳焊膏配方,使折叠寿命从20万次提升至50万次。工业控制设备方面,采用可焊性分级管理系统后,某PLC模块生产商将物料周转周期缩短35%,同时降低焊料浪费28%。值得关注的是,新能源汽车电机控制器通过实施焊点热阻映射检测,使IGBT模块的热稳定性提升23%,功率密度达到18kW/L的行业领先水平。
智能化检测系统发展趋势
当前检测体系正从单点测试向全过程监控演进,基于工业物联网的焊接质量追溯平台已实现三大突破:焊膏印刷厚度在线监测精度达±3μm,热成像仪可实时捕捉0.5℃级的温度波动,AOI系统对0201元件焊点的检测速度达1200点/分钟。某半导体封测企业部署智能检测系统后,异常响应时间从45分钟压缩至8分钟,缺陷漏检率控制在0.07%以下。未来3年,随着微焦点X射线与AI算法的深度整合,焊点三维重构分辨率有望突破5μm,为芯片级封装提供更精准的可靠性保障。
可持续发展视角下的技术前瞻
面向环保法规趋严和材料革新趋势,检测技术需同步应对两大挑战:一是无卤素焊料与低银合金的润湿特性评估,二是高频毫米波器件对焊点趋肤效应的量化检测。建议行业建立开放式检测数据库,整合超过200种焊料组合的3.5万组实验数据,开发自适应检测参数配置系统。同时,应加快制定微焊点(<100μm)的热机械可靠性标准,推动检测设备向多物理场耦合分析方向升级,为6G通信和量子器件制造奠定质量基石。
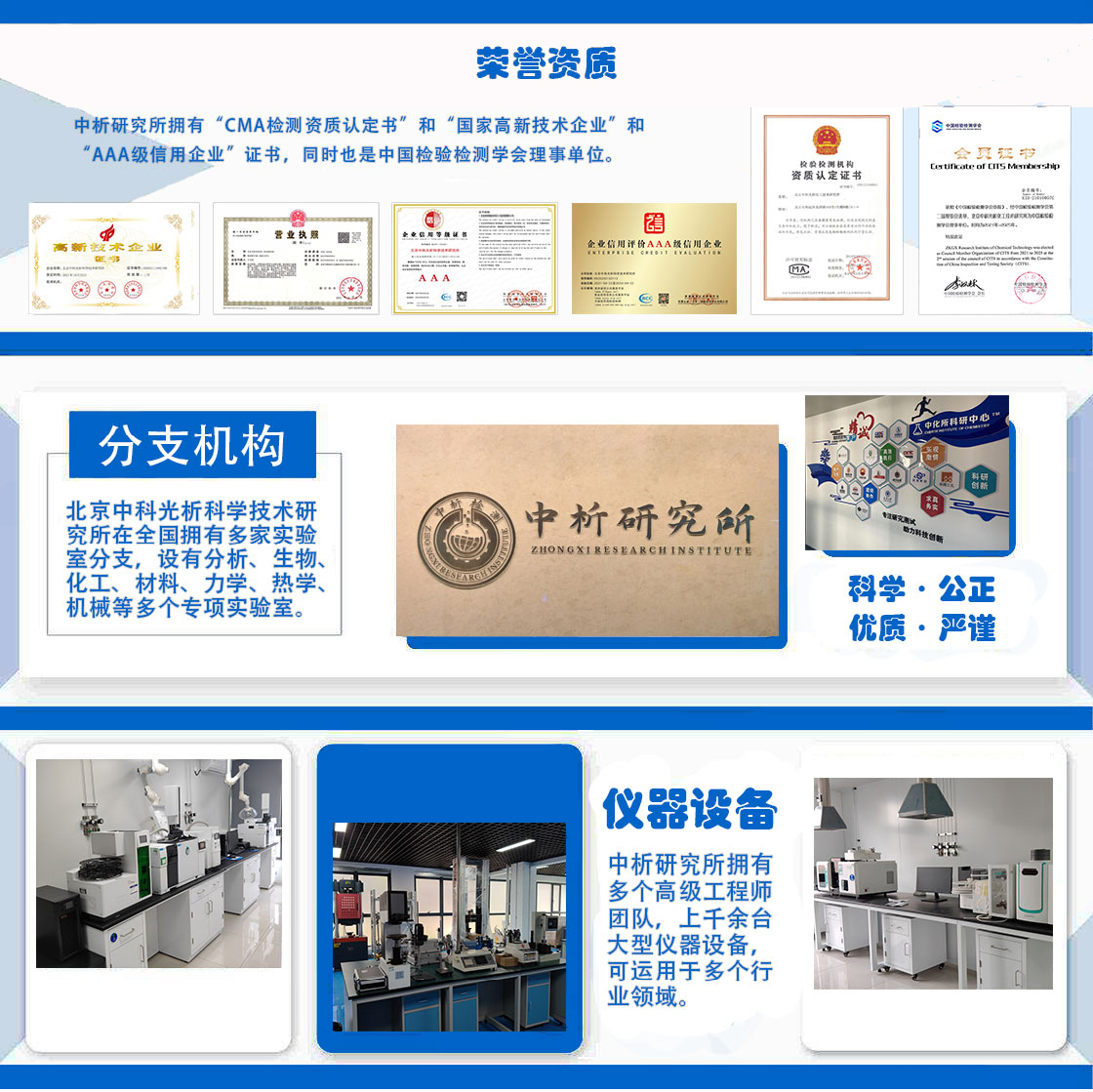
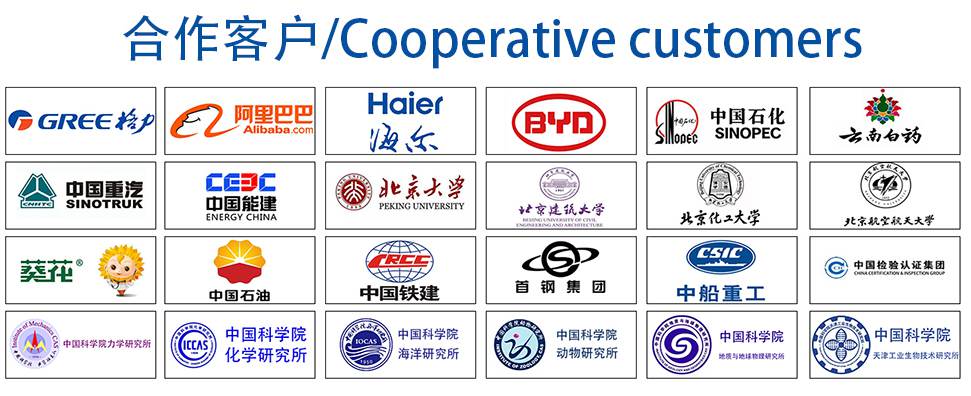