石油钻机用绞车检测的重要性及核心内容
石油钻机用绞车是钻井作业中的核心设备之一,承担着提升、下放钻具、套管以及控制钻压等关键任务。由于其在高压、高负荷及复杂工况下长期运行,绞车的性能稳定性直接关系到钻井效率和作业安全。为确保绞车的高效性与可靠性,定期开展系统性检测至关重要。通过科学严谨的检测,能够及时发现潜在故障隐患,避免因设备失效导致的停工、经济损失甚至安全事故。检测过程需严格遵循行业标准(如API规范),涵盖结构完整性、动力系统、制动性能等多个维度。
石油钻机用绞车检测的核心项目
1. 结构与外观检查
检测人员需对绞车整体结构进行目视和仪器检查,重点关注焊接部位是否开裂、基座是否存在变形、齿轮箱密封性是否达标。同时检查钢丝绳滚筒的磨损程度、绳槽完整性以及固定螺栓的紧固状态,确保无松动或腐蚀现象。
2. 动力系统与传动机构检测
通过振动分析仪和红外热像仪对电机、减速箱等动力单元进行测试,评估轴承温度、齿轮啮合精度及链条张紧度。需验证离合器接合/分离的响应时间是否在0.5秒以内,并检查液压系统是否存在泄漏或压力波动异常。
3. 制动性能测试
采用动态载荷模拟装置对刹车系统进行全工况测试,包括紧急制动和渐进制动两种模式。要求制动器在额定载荷下的响应时间不超过2秒,且刹车片摩擦系数需≥0.4。同时检测液压盘刹的油压稳定性,确保重复制动时性能无明显衰减。
4. 润滑系统与温升监测
使用油液分析仪检测齿轮箱润滑油污染物含量(如金属颗粒≤15μm),评估油品黏度变化是否在±10%允许范围内。通过温度传感器连续监测各轴承部位运行温度,要求温升不超过环境温度45℃,且同轴多点温差应<8℃。
5. 安全装置功能性验证
逐一测试过卷保护装置、防碰天车限位器的触发灵敏度和复位功能,要求保护装置在设定高度(通常为距天车3m)能100%可靠动作。同时校验指重表、压力表等仪表的示值误差,确保其精度等级达到1.5级标准。
6. 动态载荷试验
在检测平台上进行125%额定载荷的静载试验和110%额定载荷的动载试验,持续时间均不少于10分钟。要求绞车在试验过程中无结构性形变,各部件无异常噪音,且提升速度波动范围控制在±5%以内。
检测周期与结果处理
常规检测应每3000作业小时或半年实施一次,大修后需进行全项目检测。检测报告需明确标注关键参数达标情况,对不合格项提出整改建议(如更换磨损超限的刹车片或升级润滑系统),并建立设备健康档案以实现全生命周期管理。通过规范化检测流程,可有效延长绞车使用寿命,降低非计划停机率达60%以上。
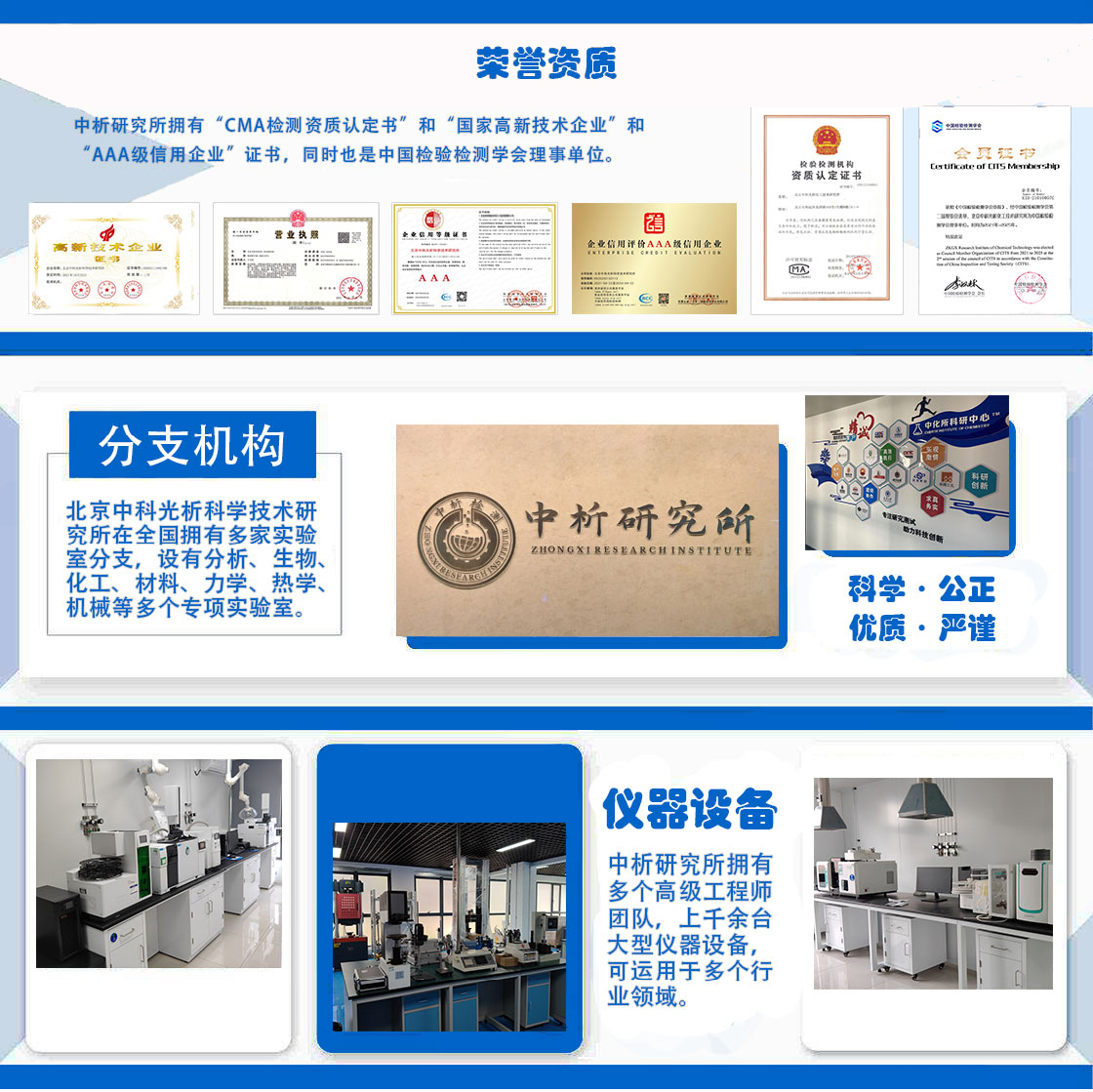
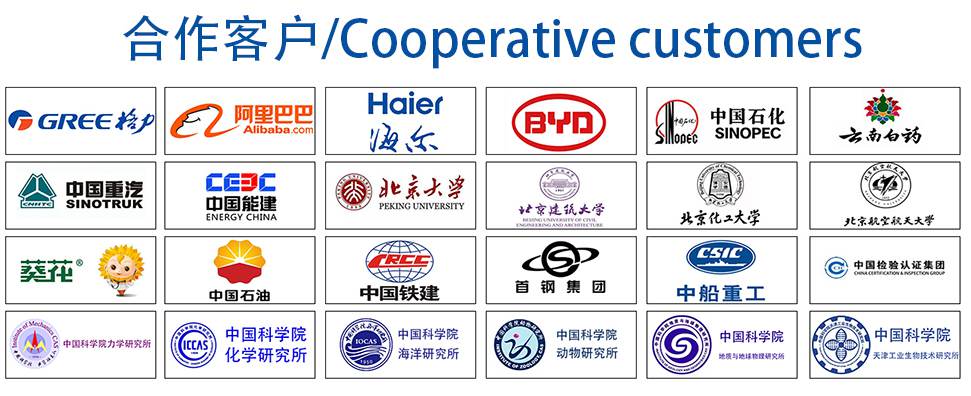