测试封隔器检测项目全解析
一、结构完整性检测
-
- 检测目的:验证封隔器主体是否存在裂纹、变形、锈蚀等缺陷,确保密封元件(胶筒、金属碗等)的几何精度。
- 方法:
- 三维激光扫描技术测量胶筒外径、内径与长度公差(误差≤0.1mm)。
- 磁粉探伤(MT)或渗透探伤(PT)检查金属件表面微裂纹。
- 螺纹规检测连接螺纹的啮合度与磨损情况。
-
- 检测项目:
- 金属部件(如中心管、卡瓦)的硬度(HRC 25-35)、抗拉强度(≥800MPa)。
- 橡胶胶筒的邵氏硬度(70-90 Shore A)、抗硫化氢老化性能(按NACE TM0192标准)。
- 行业标准:API 11D1(封隔器设计规范)、ISO 14310(井下工具性能测试)。
- 检测项目:
二、密封性能测试
-
- 试验条件:
- 双向承压测试(上下压差同时加载)。
- 温度梯度:模拟井下温度(最高180℃)。
- 指标要求:
- 在额定工作压力(如70MPa)下保压30分钟,压降≤1%。
- 使用氦气质谱仪检测泄漏率(≤1×10⁻⁶ cm³/s)。
- 试验条件:
-
- 模拟工况:
- 交变压力循环(0→70MPa→0,循环100次)。
- 井筒流体介质(含H₂S、CO₂、砂粒)。
- 失效判据:胶筒表面出现永久性沟槽或密封失效。
- 模拟工况:
三、耐压与温度适应性测试
-
- 加压至设计压力的1.5倍(如105MPa),持续15分钟,无结构破裂。
- 记录胶筒膨胀率(≤5%)及回弹性能(≥90%)。
-
- 温度范围:-40℃(极地环境)至200℃(深层储层)。
- 测试流程:
- 高温下保持4小时→自然冷却→低温保持4小时,循环20次。
- 评估指标:密封元件硬度变化(Δ≤±5 Shore A)、密封性能稳定性。
四、动态性能测试
-
- 模拟场景:井口工具下入过程中的震动、井下爆炸冲击波。
- 参数设置:
- 随机振动谱(5-2000Hz,功率谱密度0.04g²/Hz)。
- 半正弦冲击脉冲(峰值加速度50g,持续时间11ms)。
- 关键指标:零部件无松动、螺纹连接处无泄漏。
-
- 液压坐封系统:验证坐封压力(如25MPa)与解封力(≤50kN)的匹配性。
- 卡瓦锚定力测试:在最大轴向载荷下(如500kN),卡瓦与套管壁的滑移量≤2mm。
五、现场模拟测试
-
- 在试验井中模拟真实井身结构(套管尺寸:7″、9⅝″等),加载地应力与钻井液环境。
- 监测封隔器坐封后的环空压力变化及胶筒与套管的接触应力分布(光纤传感技术)。
-
- 向环空注入含砂流体(砂浓度20%),流速3m/s,持续8小时。
- 评估胶筒表面磨损深度(≤1mm)及密封性能衰减率。
六、重复使用性评估
- 循环测试:
- 同一封隔器完成10次坐封-解封循环后,检测密封性能(压降≤2%)、胶筒残余变形(≤3%)。
- 解体检查卡瓦齿磨损高度(≤0.2mm)。
检测标准与设备
- 关键标准:API 11D1 V3(性能验证等级PR2)、ISO 14310 V3(验收等级V3)。
- 核心设备:高压釜试验机(压力200MPa)、三轴应力加载系统、高低温交变试验箱。
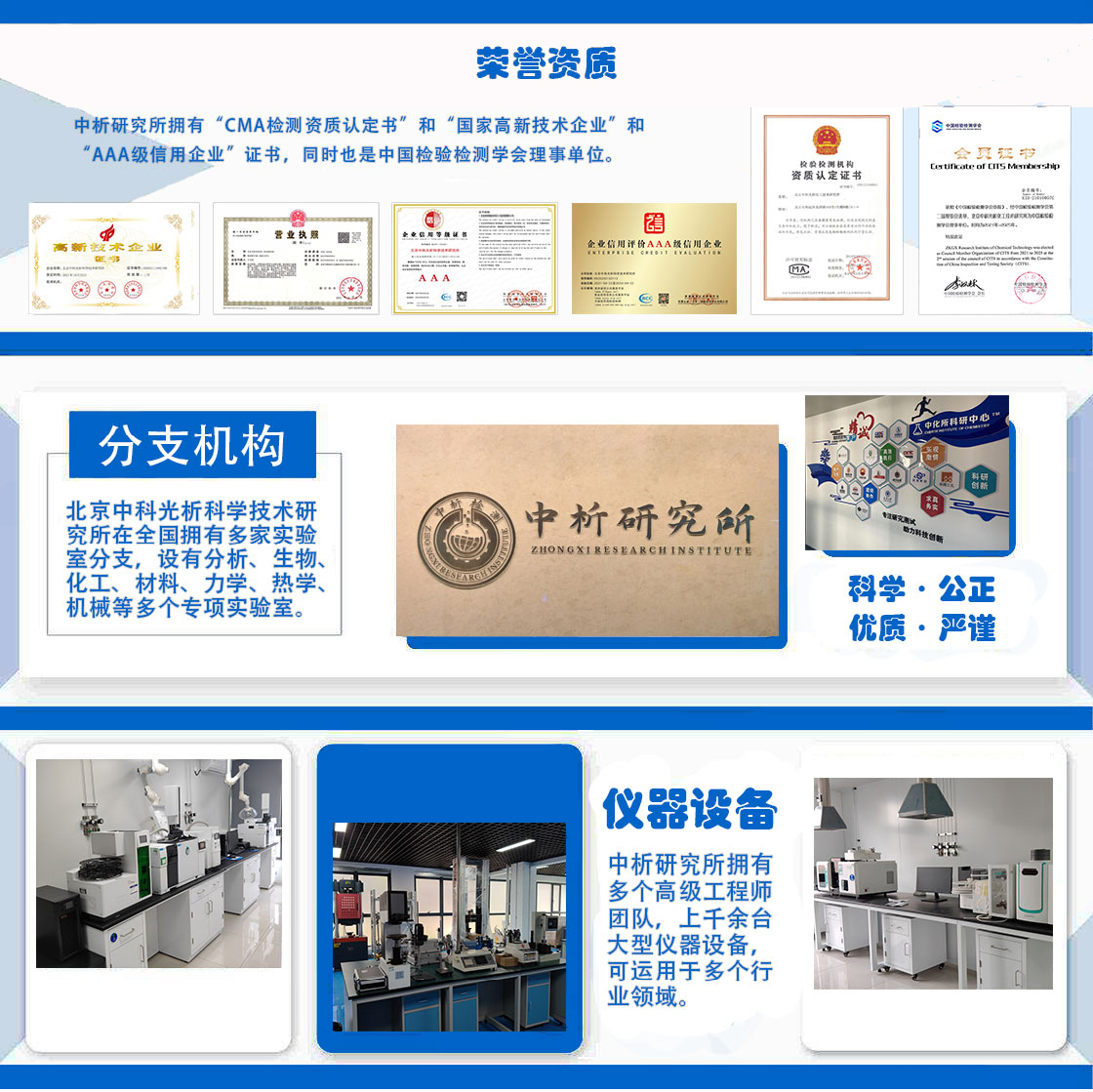
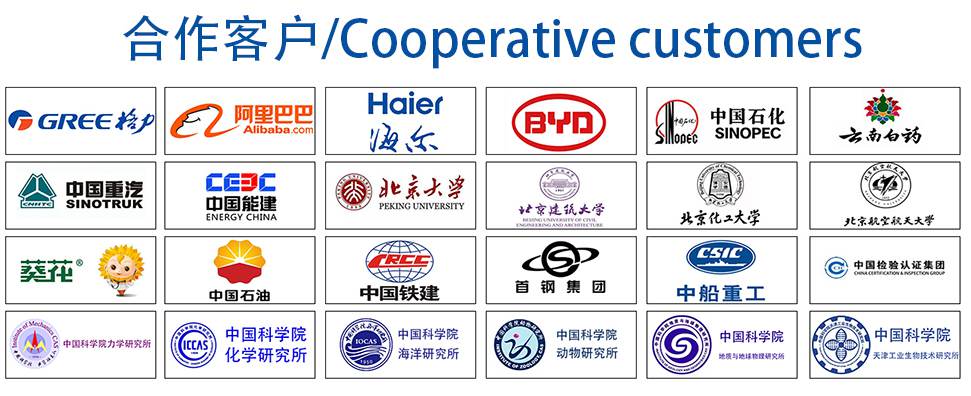
材料实验室
热门检测
29
31
31
31
51
45
53
47
49
52
43
53
44
52
45
48
42
49
45
44
推荐检测
联系电话
400-635-0567