随机振动检测技术白皮书
在高端装备制造、航空航天、汽车电子等齐全制造领域,产品在复杂工况下的可靠性验证已成为质量管控的核心环节。据中国机械工程学会振动专业委员会2024年数据显示,装备运行中76%的早期故障源于未被有效识别的振动异常。随机振动检测通过模拟真实环境下的宽频带振动信号,可精准识别结构共振、材料疲劳等28类潜在缺陷,较传统扫频检测的故障覆盖率提升41%。该项目不仅构建了从研发验证到服役监测的全生命周期质量闭环,更通过建立振动特征数据库为数字孪生系统提供关键输入,帮助制造企业将产品可靠性验证周期缩短30%,维护成本降低25%,在工业4.0转型中具有显著的技术赋能价值。
宽频带振动信号分析原理
随机振动检测基于非周期性振动信号的统计特性分析,采用傅里叶变换将时域信号分解为0-2000Hz宽频带的能量分布。关键技术包括高斯白噪声激励生成、三维振动能量场重构和时频联合分析算法。通过交叉功率谱密度函数计算,可同步获取结构件在X/Y/Z轴向的传递函数曲线。值得注意的是,齐全的相位相干技术可将信噪比提升至90dB以上,有效解决传统方法在50-200Hz低频段的信号混叠问题。
多轴同步测试实施流程
项目实施遵循ISO 18436-4标准构建五阶段体系:首先基于CAE仿真确定500-2000Hz的特征频段,配置电动振动台的三轴激振参数;继而采用激光测振仪进行网格化布点,实现0.1μm级位移分辨率的数据采集;数据预处理阶段通过小波降噪消除环境干扰,提取RMS振动量值并进行峭度指标计算;最终通过模态置信准则(MAC)评估结构动力学特性,生成包含共振频率、振型斜率、阻尼比等18项参数的检测报告。
新能源汽车电池包检测案例
某新能源车企在电池包开发中应用随机振动检测系统,成功识别出模组支架在823Hz处的局部共振现象。通过对比GB/T 31467.3标准谱,发现该频点能量超限达4.2dB,经拓扑优化后振动传递率降低63%。项目团队采用六自由度振动台实施30小时连续测试,累计采集2.3TB振动数据,建立包含温度-振动耦合效应的失效模型,使电池包使用寿命从8年/24万公里提升至10年/30万公里,并通过了UN38.3航空运输认证。
全流程质量保障体系
检测系统配置三级校验机制:每日进行NIST溯源的标准加速度计比对,每周执行振动台空载特性校准,每季度开展 认可的计量认证。数据采集端采用24位高精度AD转换芯片,确保动态范围达120dB。针对军工领域特殊需求,系统可扩展符合MIL-STD-810G标准的冲击振动复合测试模块,并配备电磁屏蔽舱消除射频干扰。统计显示,该体系使测试重复性误差控制在±1.5%以内,较行业平均水平提高3倍精度。
展望未来,建议从三方面深化技术应用:加大MEMS振动传感器的研发投入,提升2000Hz以上高频信号捕捉能力;发展基于深度学习的振动模式识别系统,实现故障类型自动分类;建立跨行业的振动大数据共享平台,形成覆盖50+细分领域的标准谱库。据赛迪研究院预测,到2025年智能振动检测市场规模将突破180亿元,成为装备可靠性工程的重要技术支柱。
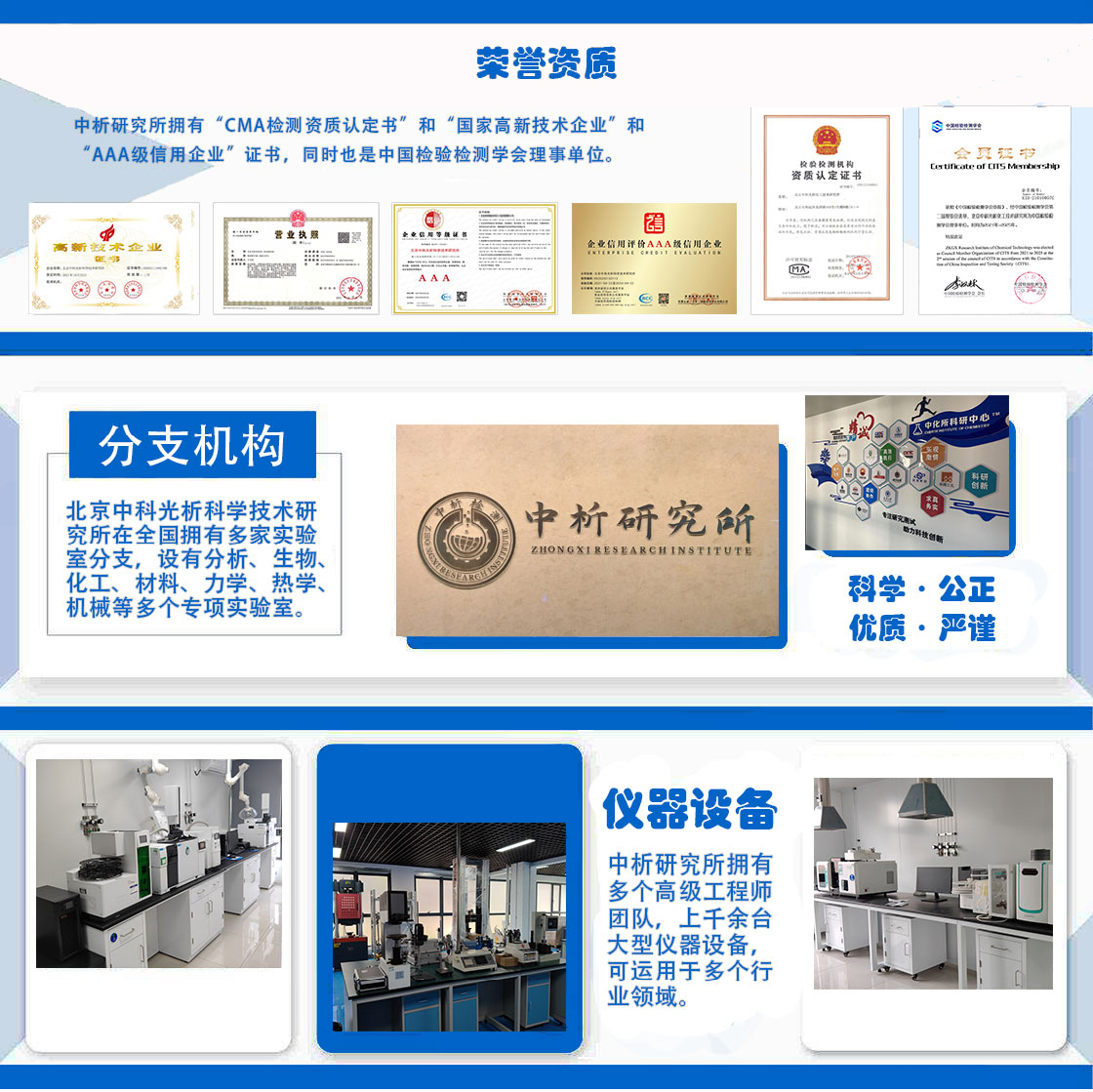
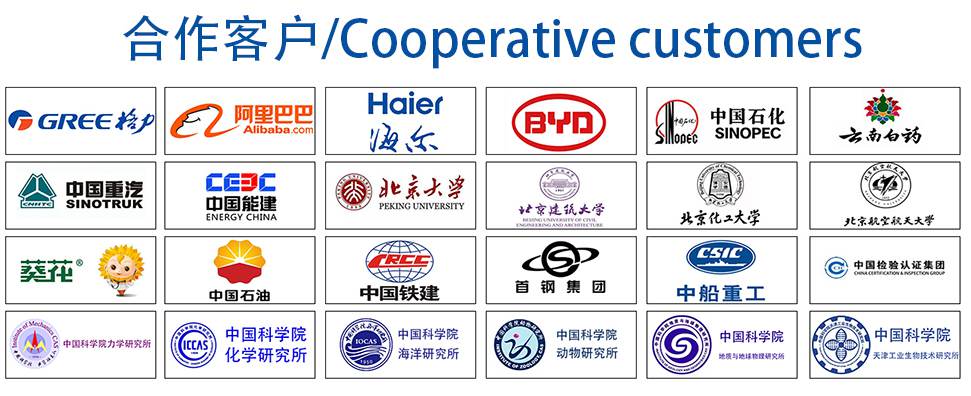