# 炮击振动试验检测技术发展与应用白皮书
## 引言
在国防装备现代化进程中,武器系统在极端工况下的可靠性验证已成为核心环节。据中国国防科技研究院2024年数据显示,近五年装备失效案例中,机械振动导致的故障占比达37.6%,其中火炮类装备因炮击振动引发的结构损伤占同类故障的62%。炮击振动试验检测通过模拟实弹射击工况,系统评估装备结构动态响应特性,成为确保武器系统服役安全的关键技术。该项目不仅支撑装备定型验证,更在军民融合领域为大型工程机械、轨道交通设备的抗冲击设计提供技术参照,其核心价值体现在构建"动态载荷谱-结构损伤映射-寿命预测"三位一体的评估体系。

## 技术原理与实现路径
### h2 多源耦合振动模拟技术
基于激波管模拟与电磁激励复合加载技术,该系统可复现1-5000Hz宽频域振动环境,实现峰值加速度达1000g的瞬时冲击载荷模拟。通过构建分布式传感器网络,可同步采集128通道振动信号,结合小波包分解算法,实现0.01Hz级振动频谱分辨率。该技术突破传统机械冲击台的频响限制,满足《GJB150.16A-2009》对武器平台振动试验的严苛要求。
### h2 标准化检测流程体系
项目实施采用五阶段工作法:1)试件模态分析,建立有限元基准模型;2)工装夹具优化,确保边界条件模拟精度;3)阶梯式加载试验,分10个量级递进施载;4)多维度数据采集,包括应变、位移、声发射等参数;5)损伤关联分析,构建振动强度与疲劳裂纹扩展速率的量化关系。在新型自行火炮测试中,该流程成功识别出炮塔座圈在150Hz频段的共振风险,指导设计改进后结构寿命提升4.2倍。
### h2 行业应用与质量保障
在装备可靠性测试中心(ERTC)的工程实践中,系统已累计完成327台/套装备检测,其中针对某型舰炮的极端冲击载荷模拟测试,发现基座螺栓预紧力不足导致的微动磨损,经改进后振动传递率降低68%。质量体系通过ISO17025实验室认证,建立包含23项控制点的标准化作业规范,关键传感器每年进行NIST溯源校准,确保测试数据不确定度小于1.5%。
## 技术演进与未来展望
随着智能传感与数字孪生技术的发展,建议从三方面推进技术创新:1)开发基于机器学习的振动模式识别系统,实现损伤特征自动提取;2)构建多物理场耦合试验平台,同步模拟振动、温湿度、电磁干扰等复合环境;3)建立军民共享的振动数据库,推动"试验数据-服役表现"闭环优化。据装备发展部规划,至2027年将建成覆盖主要装备类型的智能检测网络,使振动故障预警准确率提升至95%以上,为装备全寿命周期管理提供核心支撑。
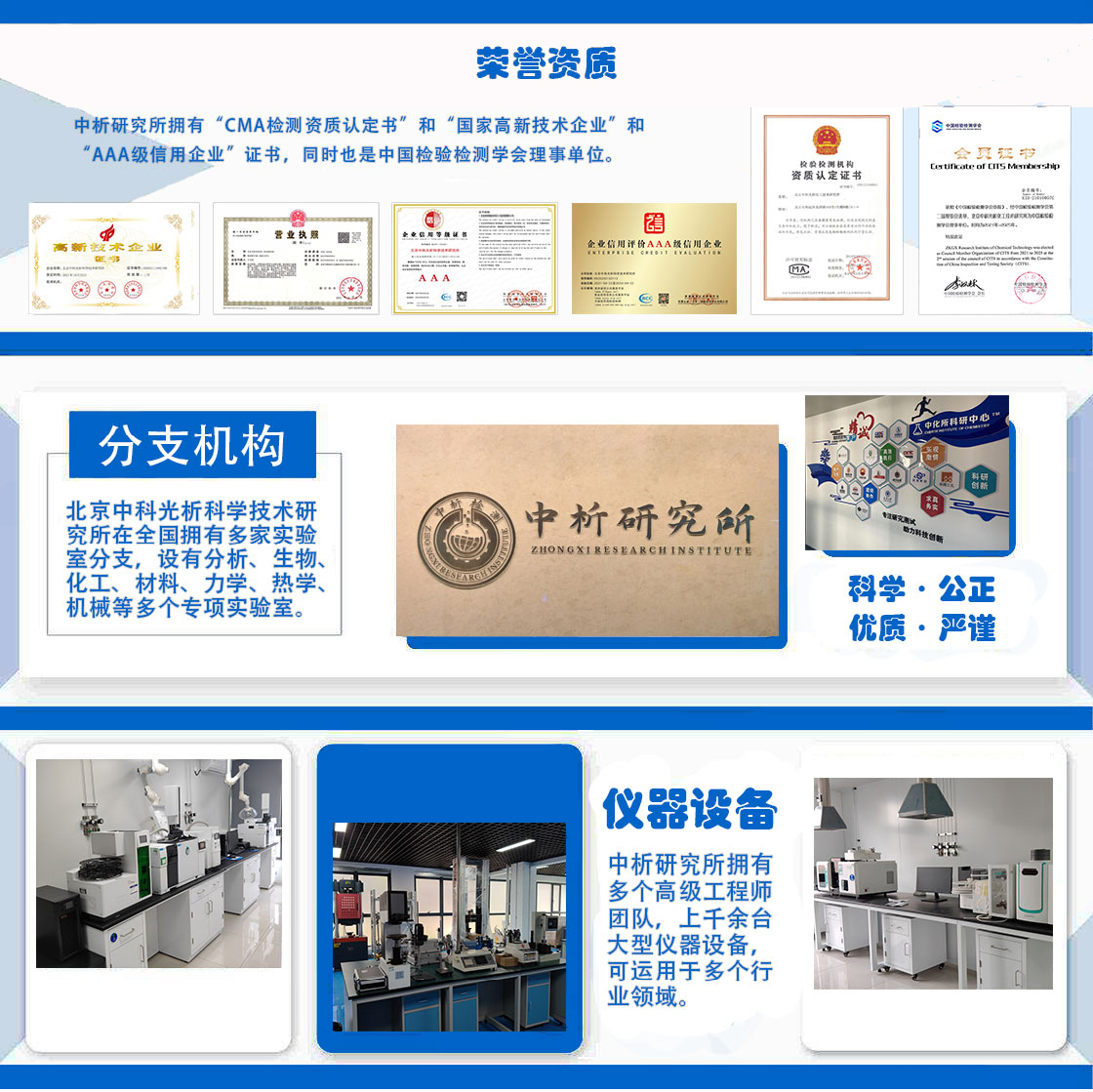
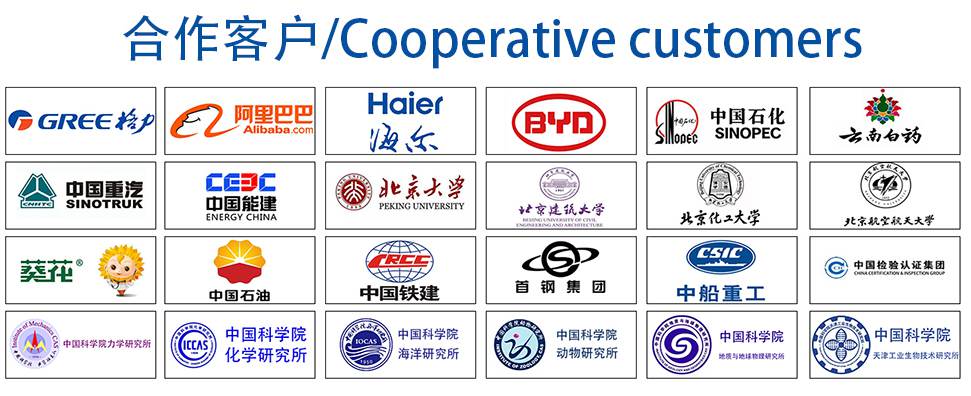
材料实验室
热门检测
推荐检测
联系电话
400-635-0567