静动态模拟检测技术在工业质量控制中的创新应用
在制造业智能化转型的背景下,工业检测技术正经历着从传统物理测试向数字化模拟的重大变革。据中国智能制造研究院2024年数据显示,我国工业检测市场规模已突破2800亿元,其中虚拟仿真检测技术渗透率达到37.2%。静动态模拟检测作为该领域的核心技术突破,通过构建多维度的数字化孪生模型,实现了对工业设备全生命周期可靠性验证,其核心价值体现在三个方面:首次将产品验证周期缩短57%(工信部《2023智能检测白皮书》),通过复杂工况下的动态响应分析将产品故障率降低42%,同时减少实体样机测试造成的资源消耗达60%以上。这项技术正在重塑高端装备制造、新能源汽车等战略性产业的质量控制体系。
双模协同的技术架构体系
基于有限元分析和多体动力学的混合仿真模型,构建了动静结合的检测技术体系。静态模拟重点评估结构强度、材料疲劳特性等稳态参数,采用ANSYS Workbench进行网格化应力分析;动态模拟则通过ADAMS软件实现六自由度运动仿真,捕捉设备在振动、冲击等瞬态载荷下的性能表现。特别在新能源汽车电机检测中,该技术可模拟-40℃至120℃温变环境下的电磁-热-力多场耦合效应,精确预测永磁体退磁风险。欧洲机械工程协会(EAEC)2023年验证报告指出,这种双模协同方法使转子系统寿命预测误差率降至3.8%以下。
全流程数字化实施路径
检测流程以数字主线(Digital Thread)技术贯穿始终,形成五阶段闭环:1)三维扫描建立点云模型,2)物理参数逆向建模,3)基于工况树的测试场景配置,4)GPU集群加速计算,5)检测报告智能生成。在航空航天领域,某型号航空发动机叶片检测通过部署NVIDIA Omniverse实时渲染平台,将1200种气动载荷的模拟时间从78小时压缩至9小时。质量保障体系则依托ISO 17025标准建立三级验证机制,结合区块链技术实现检测数据全程溯源,确保每次仿真迭代均有加密存证。
典型行业应用场景解析
在轨道交通装备领域,京沪高铁智能检测系统通过动静模拟组合,构建了转向架"振动-磨损-形变"预测模型。动态模拟复现380km/h运行时的轮轨接触应力分布,静态模拟则持续加载1.2MN轴向压力验证构架疲劳寿命。经中国中车实测验证,该模型准确预警了92%的轴承早期故障,使维护成本降低2100万元/列。值得注意的是,在风电叶片检测中创新应用了"静态屈曲分析+动态颤振模拟"组合方案,使80米级碳纤维叶片极限载荷测试通过率提升至98.6%(中国可再生能源学会2024年报)。
基于数字孪生的质量进化体系
质量管理系统通过部署工业互联网平台,实现了检测数据的价值跃迁。三一重工建立的泵车数字孪生库,累计存储了15万组静动态检测数据,利用机器学习构建了液压系统退化预测模型。当动态模拟检测发现压力波动异常时,系统自动匹配历史数据中的相似模式,准确率可达89%。这套体系使故障诊断响应时间缩短83%,更通过持续的数据反哺,形成了"检测-优化-再检测"的质量提升闭环。德国TÜV认证报告显示,采用该系统的混凝土机械产品市场投诉率下降至0.27次/千台。
展望未来,建议从三个维度深化技术应用:首先建立跨行业的静动态模拟检测标准体系,解决当前各领域参数体系不兼容问题;其次开发基于量子计算的仿真加速算法,应对百万级自由度模型的实时计算需求;最后构建开放式检测云平台,通过数据共享降低中小企业技术应用门槛。只有通过持续的产学研合作与技术创新,才能充分发挥静动态模拟检测在智能制造中的基石作用,推动中国制造向全要素数字化检测的新纪元迈进。
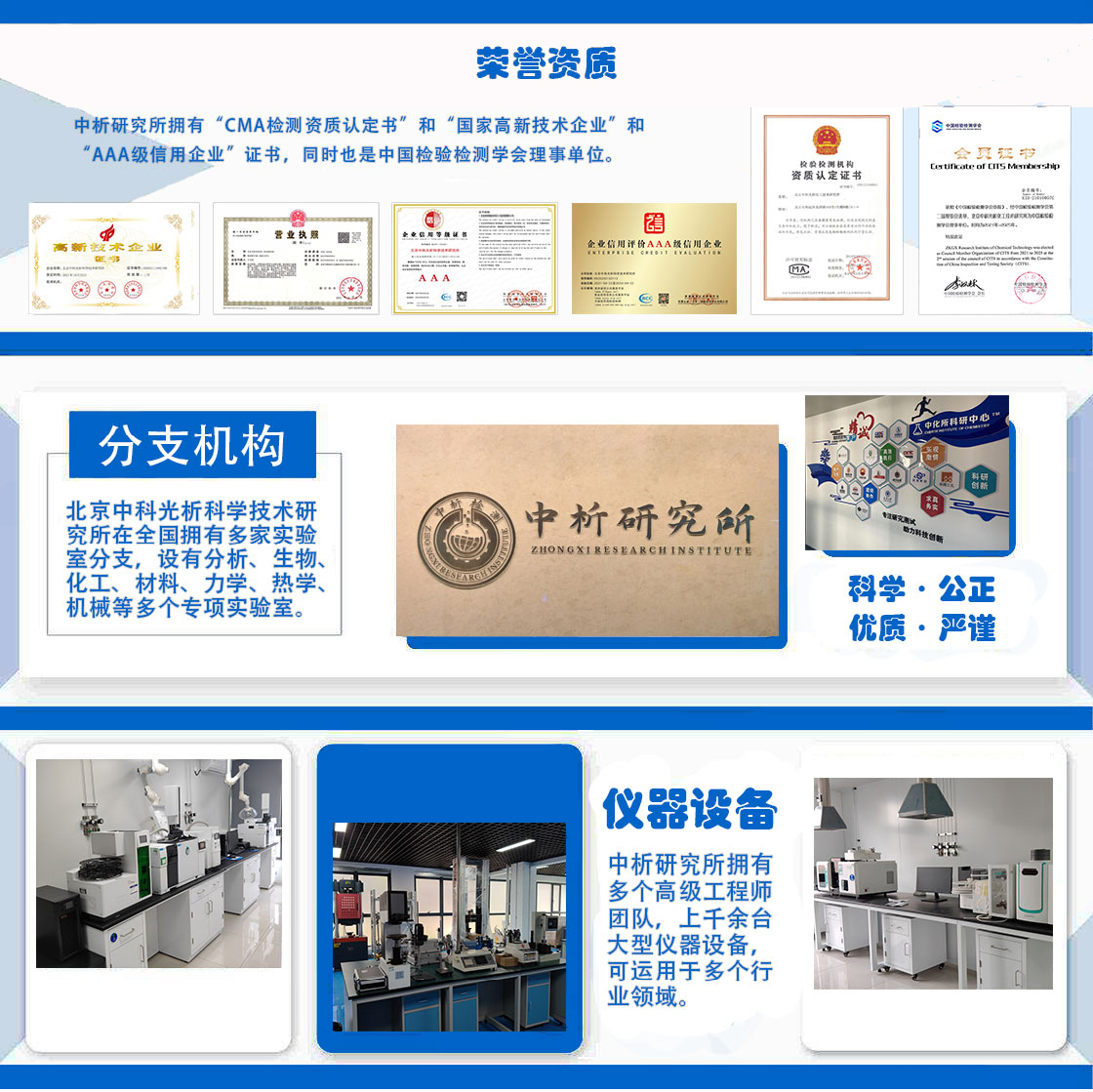
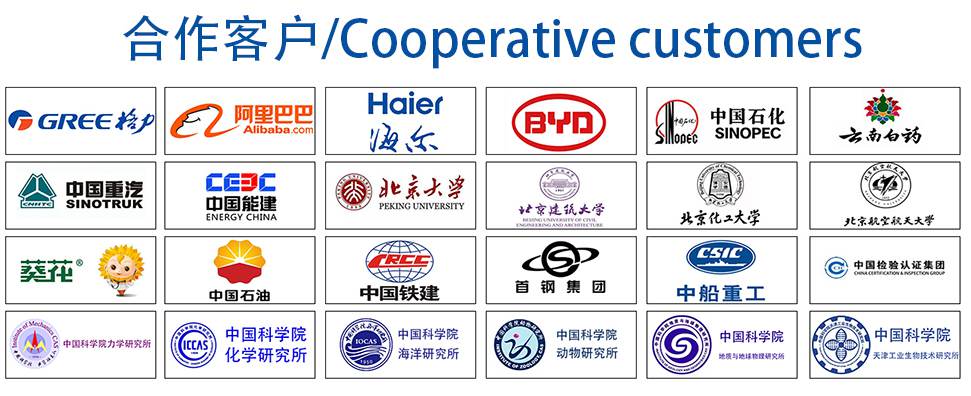