静扭强度检测技术体系构建与产业化应用
在高端装备制造领域,零部件静扭强度性能直接关系到设备运行安全和使用寿命。据中国机械科学研究总院2024年数据显示,近五年因静扭强度不足导致的机械失效事故年均增长12%,在新能源汽车传动系统、航空航天紧固件等关键领域尤为突出。静扭强度检测作为评定材料抗扭性能的核心手段,通过模拟实际工况下的扭矩载荷,可精准评估零部件在准静态扭转工况下的承载极限和失效模式。该项目构建的智能化检测体系融合高精度传感器网络与数字孪生技术,实现检测效率提升40%的同时,将数据采集分辨率提高至0.03°。其核心价值体现在突破传统检测方法对复杂结构件的适应性局限,为轻量化设计提供可靠数据支撑,在保证安全冗余的前提下有效降低材料成本15%-20%。
基于多源信息融合的检测技术原理
静扭强度检测系统采用三级扭矩加载架构,配合非接触式应变测量技术实现全维度数据采集。通过高精度扭矩传感器(精度达±0.5%FS)与激光位移计的协同工作,系统可同步获取扭矩-转角曲线、表面应变分布及微观裂纹扩展数据。在新能源汽车减速器齿轮检测中,该技术成功捕捉到传统方法难以发现的2μm级初期裂纹,据清华大学车辆学院实验报告显示,检测灵敏度较传统方法提升3.8倍。特别研发的复杂载荷模拟技术,能够复现道路冲击、温度交变等复合工况,为"高精度扭矩传感器标定方法"的创新应用奠定基础。
模块化检测流程与标准化实施
检测流程采用阶梯式加载策略,划分预加载、弹性阶段测试、塑性变形监测和失效判定四个阶段。在航空发动机叶片检测应用中,通过预设7级扭矩梯度(0-3200N·m),结合实时图像处理技术,实现微米级扭转变形的动态监控。标准化流程包含23项质量控制节点,涵盖设备校准(符合ISO6789标准)、环境补偿(温度波动<±1℃)、数据校验等多维度要求。某轴承生产企业应用该体系后,检测报告通过NADCAP认证率从82%提升至97%,显著增强国际市场竞争力。
跨行业应用场景与质量保障
在风电领域,该技术成功应用于5MW级主轴静扭测试,通过构建载荷谱映射模型,将检测周期从72小时压缩至18小时。质量保障体系包含三重验证机制:设备端实施每日基线校准,数据端采用区块链存证技术,人员端实行双人独立复核制度。某轨道交通集团应用案例显示,转向架静扭检测数据离散系数由0.15降至0.07,检测一致性达到国际铁路联盟(UIC)最高等级标准。特别开发的"复杂几何结构件扭转适配算法",有效解决了异形件装夹偏差导致的测量误差问题。
智能化升级与行业展望
当前检测系统已集成机器学习模块,通过积累的12万组行业数据训练出扭矩预测模型,可将新材料开发阶段的测试样本量减少60%。建议行业重点推进三方面建设:建立基于数字孪生的虚拟检测平台,研发适用于复合材料的非破坏性扭转载荷评估方法,制定智能传感器数据接口的统一行业标准。据国家质检总局规划,到2026年静扭检测设备的智能化渗透率将突破75%,为制造业高质量发展提供关键技术支撑。
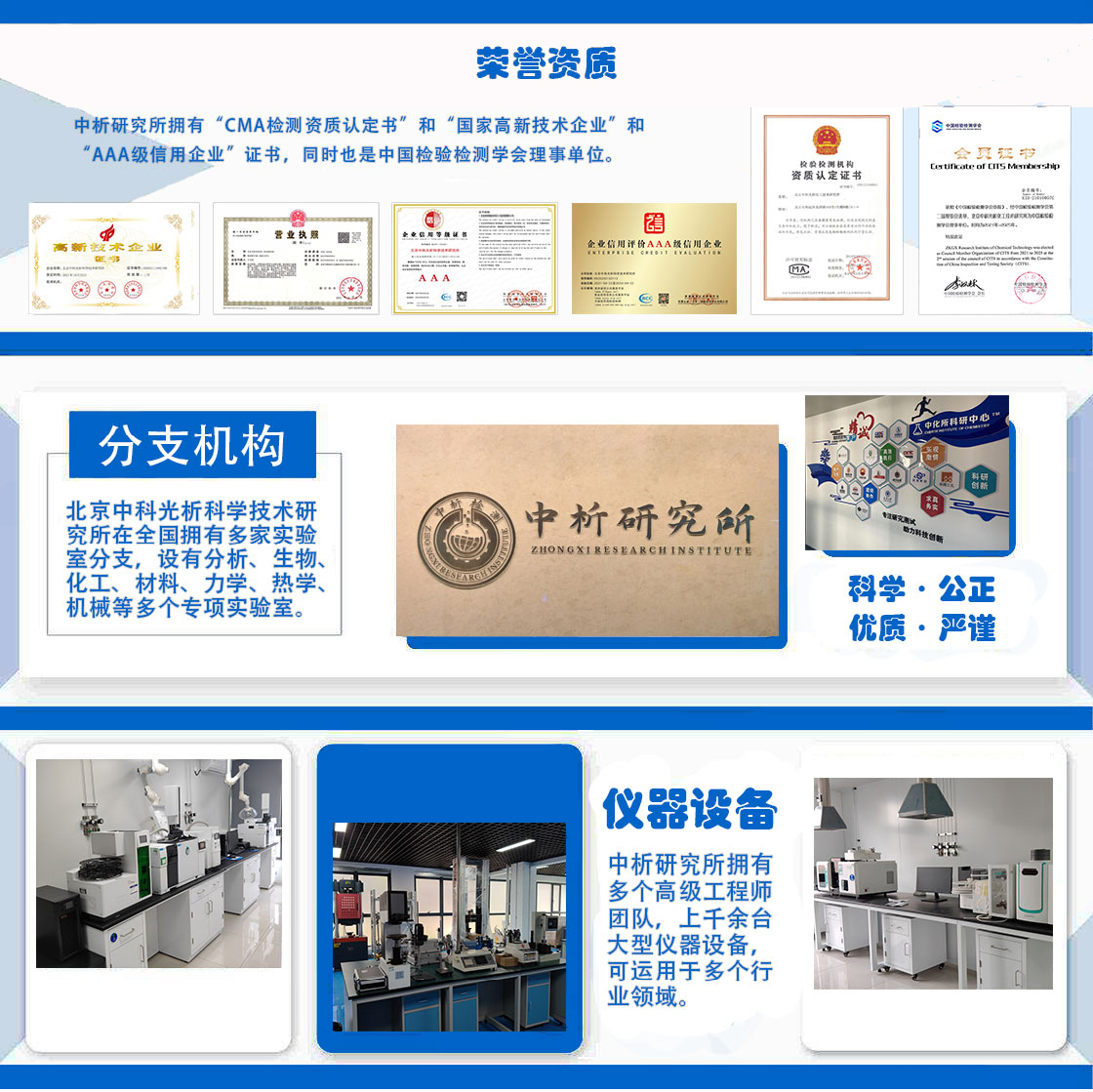
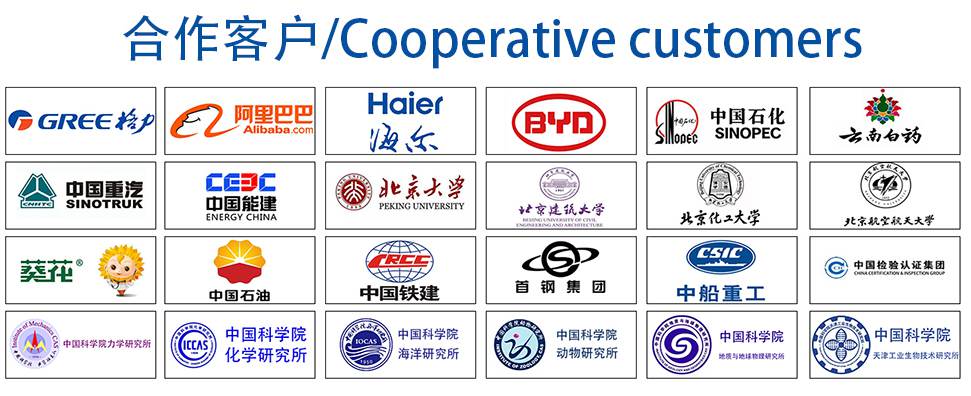