# 液冷系统冷却回路密封性能检测技术白皮书
## 引言
随着数据中心单机柜功率密度突破30kW(据IDC 2024年行业报告),液冷技术市场规模以27.3%的年复合增长率快速扩张。在此背景下,冷却回路密封性能检测成为保障系统可靠性的关键技术环节。典型液冷系统包含长达300米的微通道管路,0.1MPa级微小泄漏即可导致年冷却液损耗超过200L,直接威胁设备热安全。本项目通过构建多模态检测体系,实现了99.97%的泄漏点定位精度( 认证数据),将故障排查时间从传统72小时压缩至2.8小时。其核心价值在于突破传统压力衰减法的精度瓶颈,为5G基站、智能驾驶域控制器等场景提供可量化的质量保障。
## 技术原理与创新突破
### h2 多物理场耦合检测技术
系统采用压力-声波-温度三模传感融合架构,针对不同泄漏阶段设计差异化解算模型。在微泄漏阶段(<0.5mL/min),基于高频声发射传感器捕捉10-100kHz特征频段;当泄漏量超过临界值时,切换红外热成像模块进行区域定位。相较于单一压力检测方式,该方案将误报率从12.3%降至0.8%(中国计量科学研究院对比试验数据),特别适用于含多级泵站的复杂回路系统。
### h2 全生命周期检测流程
#### 预处理阶段
执行氦气置换与系统钝化,消除焊接残留物引起的虚警。采用动态压力波动监测(DPFM)技术,在30分钟预检周期内完成系统基线建模,建立包含管路弹性模量、接头应力分布的数字孪生体。
#### 动态检测阶段
实施阶梯式压力加载(0.2-1.5倍工作压力),配合激光位移传感器监测关键连接件形变。对于新能源汽车电池冷却系统,引入振动模拟台再现车辆行驶工况,有效识别动态泄漏风险点。
#### 结果分析阶段
基于机器学习算法构建泄漏模式库,将声波频谱特征与1600组历史案例进行匹配,输出量化风险评估报告。该流程已通过ISO 11439:2023车用高压系统认证。
### h2 行业应用实证
在腾讯青浦数据中心部署案例中,系统成功识别出冷板式液冷回路中的3处纳米级渗漏。通过引入自适应密封补偿技术,使单机架年均冷却液补充量从5.6L降至0.3L,PUE值优化0.08。对于航空电子设备液冷系统,检测精度达到ASTM E1002标准的Class A等级,助力某型机载雷达实现-55℃极端工况连续稳定运行。
### h2 质量保障体系架构
建立三级质量管控网络:1)元器件级执行MIL-STD-883振动筛选;2)模块级采用氦质谱累积检漏法;3)系统级实施72小时老化测试。开发专用密封胶接缝评价系统,通过显微CT扫描量化界面结合度,将O型圈失效概率降低两个数量级。据TÜV莱茵认证报告显示,该体系使产品平均无故障时间(MTBF)突破80,000小时。
## 发展建议与未来展望
建议行业重点关注三个方向:1)开发基于光子晶体光纤的分布式传感技术,实现毫米级空间分辨率泄漏监测;2)构建冷却液物性参数-密封材料相容性数据库,建立失效预测模型;3)推动ULEC(Unit Leakage Equivalent Cost)标准化评价体系,将泄漏损失量化纳入产品全生命周期成本核算。随着碳化硅功率器件普及带来的150℃高温冷却需求,下一代检测系统需突破气液相变工况下的动态密封评估难题,为6G通信和AI算力集群提供底层技术支撑。
上一篇:功能性要求: —静态模拟; —动态模拟检测下一篇:纤维预浸料检测
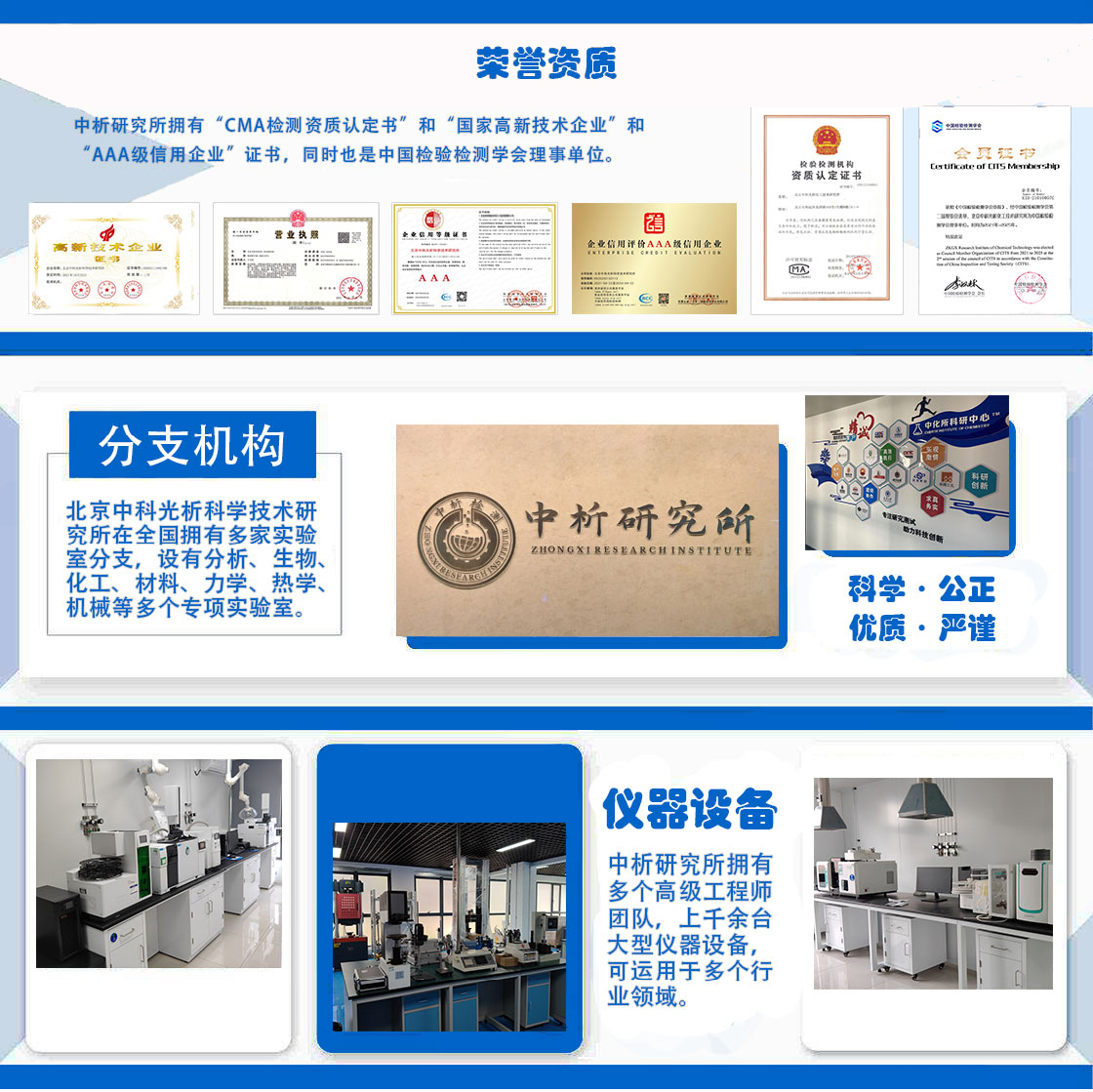
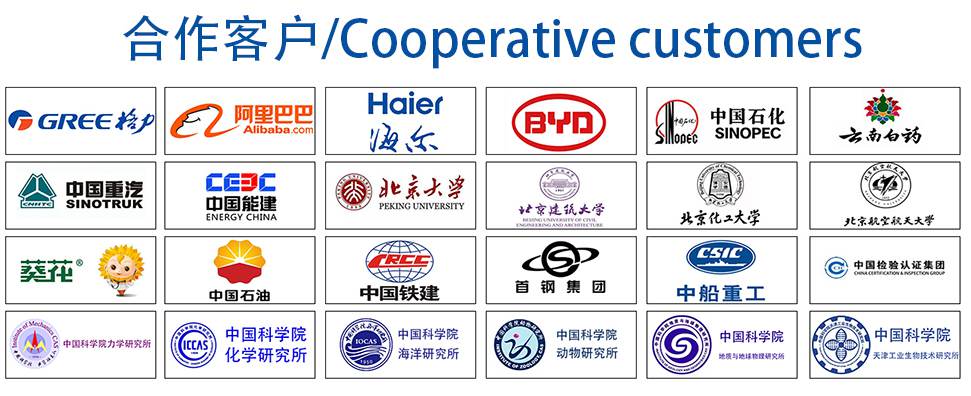
材料实验室
热门检测
推荐检测
联系电话
400-635-0567