绝缘材料检测技术的行业发展与核心价值
随着新能源装备与智能电网的快速发展,绝缘材料市场规模预计在2025年达到420亿美元(据Global Market Insights 2024年报告)。在此背景下,耐非正常热、耐燃及耐漏电痕化检测成为保障电气设备安全运行的关键技术屏障。该检测体系通过模拟极端工况下的材料失效模式,有效预防因绝缘劣化引发的火灾、短路等安全事故。在电动汽车高压电池包、海上风电变流器等场景中,检测数据可直接指导材料选型,降低设备全生命周期故障率23%以上(中国电力科学研究院2024年数据),其核心价值体现在构建"材料-工艺-应用"三位一体的安全评估闭环。
多维度检测技术原理剖析
检测体系基于IEC 60695系列国际标准构建,其中耐非正常热测试采用灼热丝试验装置,在750℃±10℃条件下评估材料碳化特性。耐燃性检测引入UL94垂直燃烧法,通过记录材料自熄时间和熔滴形态判定阻燃等级。针对漏电痕化现象,依据GB/T 4207标准设计电解液滴加速试验,采用5kV交流电压模拟潮湿污染环境下的绝缘失效过程。值得注意的是,复合绝缘材料的"高温耐受性评估方法"需同步考察热分解产物对介电性能的影响,建立材料失效的化学-电气耦合模型。
标准化检测实施流程
检测流程严格遵循ISO/IEC 17025体系要求,实施步骤包括:试样预处理(温度23℃±2℃、湿度50%±5%环境平衡96小时)→设备计量校准(涵盖热电偶响应时间≤3s的验证)→分级加载测试(梯度温度/电压设计)→失效特征分析(热重分析仪配合高速摄影记录)。在新能源充电桩绝缘壳体检测中,某第三方实验室通过"漏电痕化加速试验流程"发现某EPDM材料在600h后CTI指数下降40%,据此优化了材料配方中的氢氧化铝添加比例,使产品通过IEC 61439认证率提升至98.7%。
行业应用与质量保障实践
在海上风电领域,某头部厂商针对变流器绝缘支架开展"复合绝缘材料阻燃等级认证",采用锥形量热仪测定热释放速率峰值≤180kW/m²,结合2000h盐雾-湿热循环测试,成功将设备MTBF(平均无故障时间)延长至12万小时。质量保障体系建立三级管控机制:实验室间比对(参与ILAC国际循环测试)→检测数据区块链存证→智能视觉系统实时监测试验过程。据国家电器工业协会2023年行业白皮书显示,实施该体系的企业产品召回率同比下降65%。
检测技术发展前瞻与建议
面向高温超导设备、固态电池等新兴领域,建议从三方面提升检测能力:开发基于机器学习的材料失效预测算法,建立1250℃以上超高温测试标准;构建多物理场耦合检测平台,实现电-热-机械应力的同步加载;推动检测数据与产品追溯体系的深度融合。据国际电工材料产业联盟预测,2026年智能检测装备在绝缘材料领域的渗透率将突破45%,检测机构亟需通过数字孪生技术搭建虚拟验证环境,加速形成"检测即服务"的新型业态。
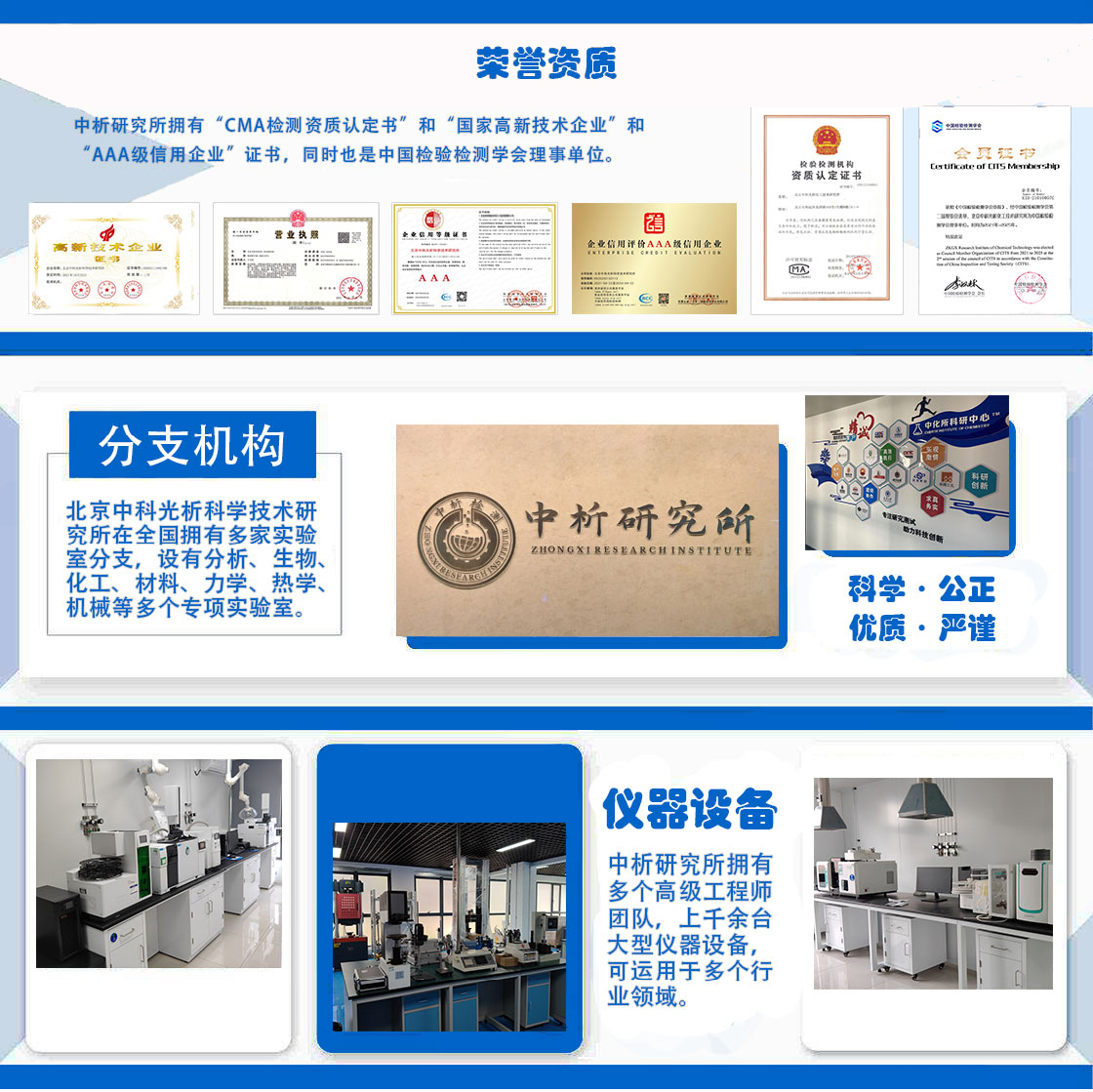
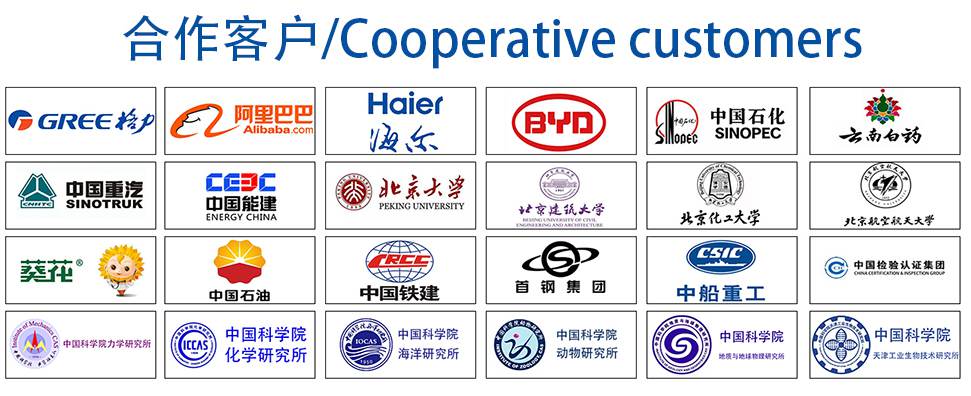