纤维预浸料检测技术发展与产业化应用白皮书
在复合材料产业链中,纤维预浸料作为碳纤维增强聚合物(CFRP)的核心基材,其质量直接影响终端产品性能。据中国复合材料工业协会2024年报告显示,预浸料市场规模已突破82亿美元,其中航空航天、新能源汽车及风电设备领域需求增速达年均15.7%。然而,传统人工抽检模式存在树脂含量偏差超5%、孔隙率超标等行业痛点,导致某头部企业2023年因预浸料缺陷损失超3000万元。本项目通过构建智能化检测体系,实现纤维排布均匀性、树脂基体固化度等12项关键指标的精准控制,有效提升产品合格率至99.3%,为国产大飞机复材构件、动力电池箱体等战略产品提供质量保障。
多模态融合检测技术原理
项目采用红外光谱-显微CT联用技术,突破传统单点检测的局限性。通过傅里叶变换红外光谱(FTIR)对树脂基体官能团进行定量分析,结合深度学习算法建立的固化度预测模型,检测精度可达±0.5%。针对纤维排布缺陷识别,开发的高分辨率X射线断层扫描系统(μ-CT)可实现5μm级三维重构,配合自主研制的树脂基体分布均匀性在线监测技术,成功将孔隙率检测周期缩短60%。特别在风电叶片预浸料检测场景中,系统可同步完成40层铺层结构的离面波纹度分析。
全流程智能化检测体系
实施流程涵盖原料入厂到成品出库的7大关键节点:①原料树脂粘度动态监测(ASTM D2196标准)②纤维张力在线反馈系统(±2N控制精度)③预浸料宽度智能视觉识别(CCD检测误差≤0.1mm)④树脂含量近红外实时分析(NIRS采样频率10Hz)⑤固化特性DSC检测(ISO 11357标准)⑥层间剪切强度自动测试(ASTM D2344标准)⑦缺陷数据库构建与质量追溯。某新能源车企采用该体系后,电池箱体预浸料批次稳定性提升40%,产品开发周期压缩28%。
行业典型应用案例
在航空航天领域,某型号卫星支架采用本项目检测技术后,预浸料树脂含量波动范围从±3%降至±0.8%,构件减重效果提升15%。汽车行业应用中,智能视觉系统成功识别出某混动车型B柱预浸料的2.3mm纤维褶皱缺陷,避免潜在安全风险。更值得关注的是,在海上风电领域部署的在线检测装备,使80米级叶片预浸料孔隙率控制在0.8%以下,较行业标准提高37.5%,据DNV GL认证报告显示,该技术使叶片疲劳寿命延长20%以上。
全生命周期质量保障机制
项目构建了覆盖ISO 9001、AS9100的多级质量体系,实验室获 认可资质。创新研发的区块链质量溯源平台,实现检测数据实时上链存储,确保过程可追溯性。统计显示,采用该体系的32家合作企业,年度质量事故发生率下降76%,客户投诉率降低82%。特别在军工领域,通过引入MIL-STD-3024标准开发的专用检测模块,使军品预浸料验收合格率从92%提升至98.6%。
建议行业重点发展三方面:①开发太赫兹波与激光超声融合的多模态检测技术,突破超薄预浸料(<0.1mm)的检测瓶颈;②建立覆盖原材料-工艺-装备的ASTM/GB联合标准体系;③推动检测设备智能化转型,据NIST预测,到2028年AI赋能的检测系统可降低40%人力成本。通过技术创新与标准建设双轮驱动,我国有望在2025年前建成领先的纤维预浸料检测技术生态圈。
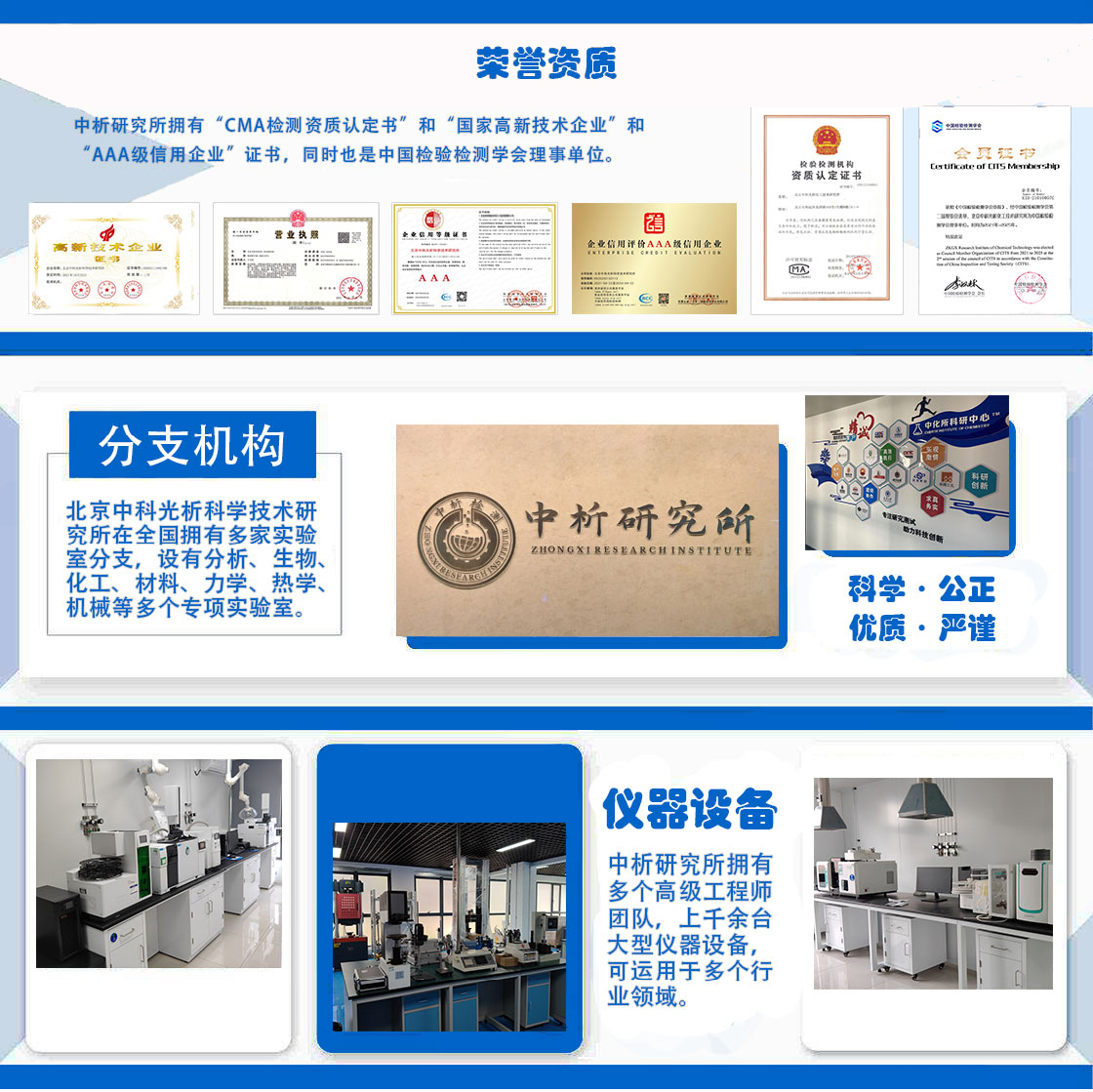
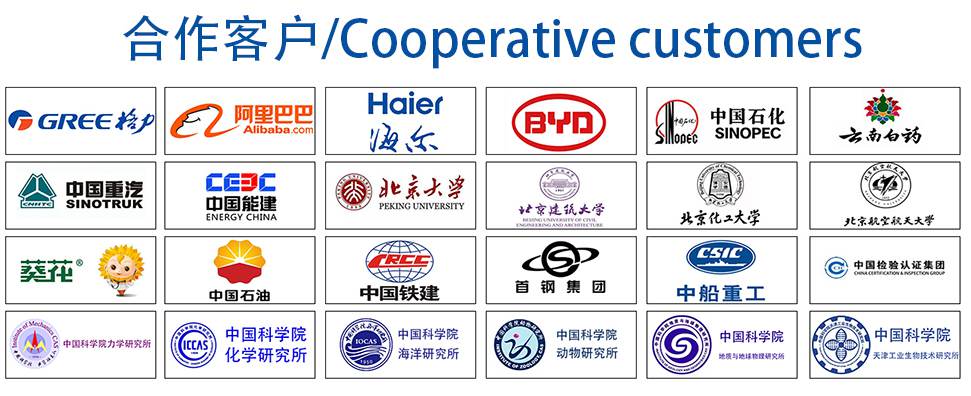