成型胶合板检测的重要性
成型胶合板作为一种广泛应用于建筑、家具、包装等领域的重要材料,其质量直接影响产品的安全性和使用寿命。成型胶合板通过将多层薄木片或纤维材料胶合压制而成,需具备高强度、耐候性、环保性等特性。然而,生产过程中可能因原材料质量、胶黏剂配比、工艺参数等环节的偏差导致产品缺陷。因此,严格的检测项目是确保其符合国家标准(如GB/T 9846、GB/T 17657)及行业规范的核心手段。
成型胶合板检测的核心项目
1. 物理性能检测
物理性能是衡量成型胶合板质量的基础指标,主要包括: - 密度与含水率:通过称重法和干燥法测定,确保板材密度均匀且含水率符合标准(通常≤14%); - 抗弯强度与弹性模量:利用万能试验机进行三点弯曲测试,评估其承重能力; - 胶合强度:通过剥离试验检查层间粘合是否牢固,避免分层问题。
2. 化学安全指标检测
环保性是现代胶合板的核心要求,重点检测项目包括: - 甲醛释放量:采用气候箱法或穿孔萃取法,确保符合E0/E1级标准; - 重金属含量:使用原子吸收光谱法检测铅、镉等有害物质; - VOCs(挥发性有机物):通过气相色谱-质谱联用分析,避免室内空气污染。
3. 耐久性检测
针对不同使用环境,需进行以下专项测试: - 耐水性:浸泡或沸水处理后观察板材膨胀率及强度变化; - 抗霉变与防虫性:模拟湿热环境,检验防霉剂和防腐剂的有效性; - 耐候性:通过紫外线加速老化试验,评估长期使用后的性能稳定性。
4. 外观与尺寸检测
包括表面平整度、翘曲度、边缘缺损等目测检查,以及长度、厚度、对角线偏差的精密测量,确保加工精度和外观质量。
检测流程与质量控制
成型胶合板的检测需遵循“抽样-实验室分析-结果判定”的标准化流程,并结合生产线的实时监控数据。企业应建立完善的质量管理体系,定期校准检测设备,培训专业人员,以降低批次不合格风险。同时,针对出口产品还需符合国际标准(如EN 13986、JIS A 5908),通过第三方认证提升市场竞争力。
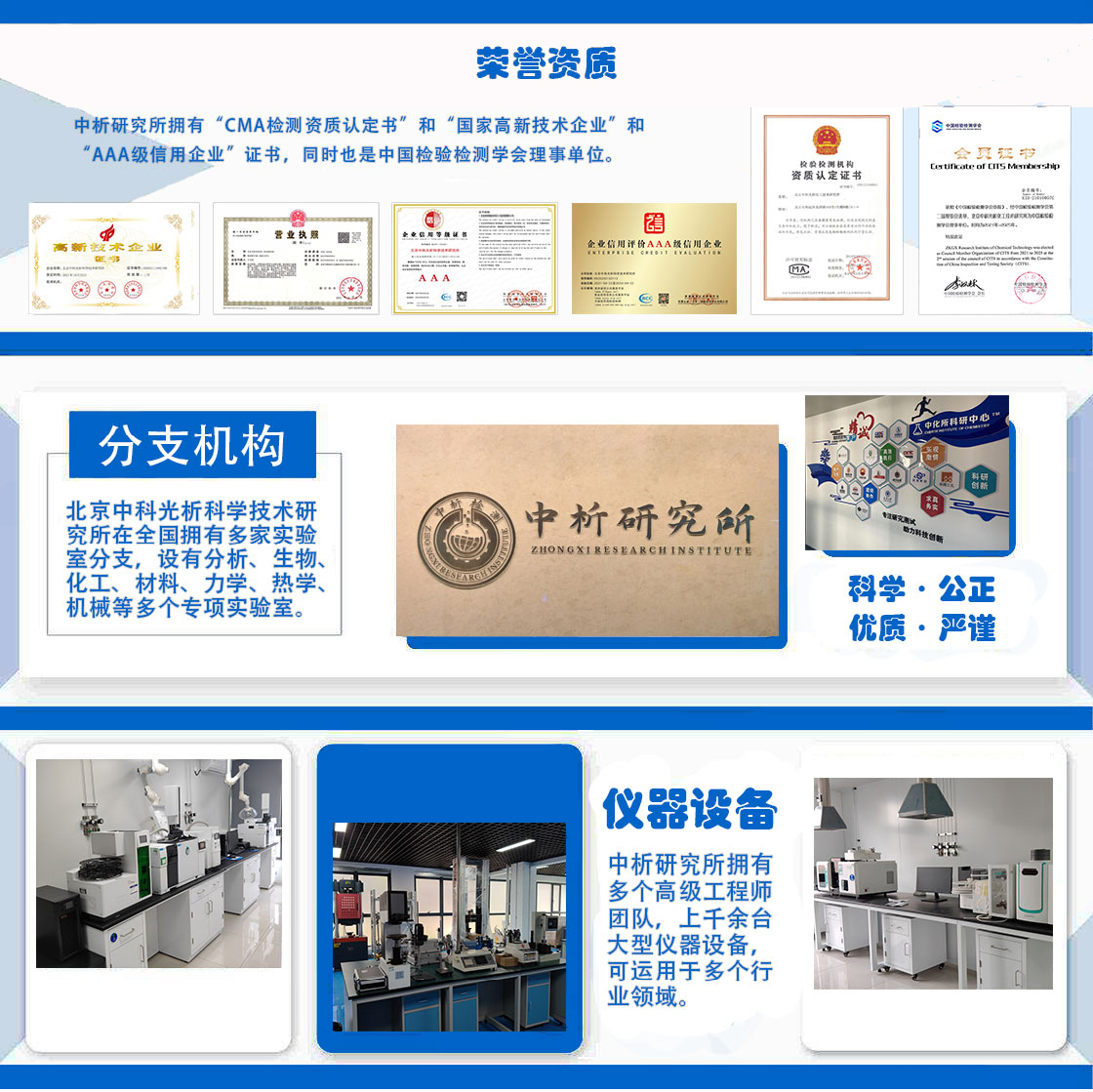
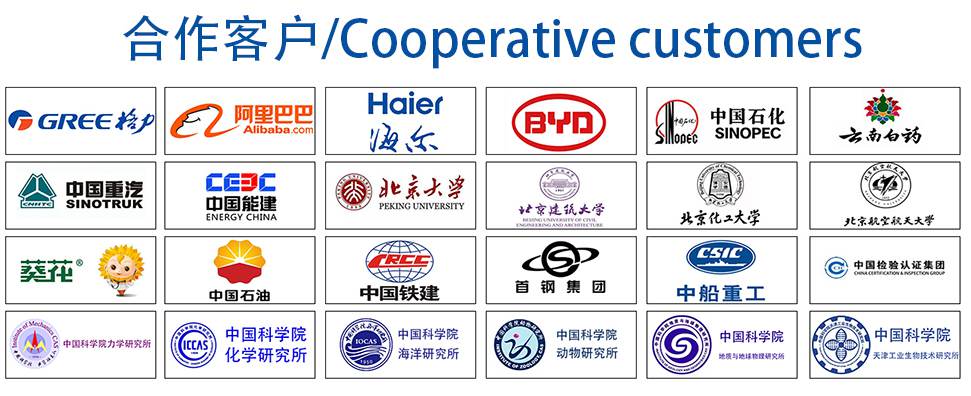