推力关节轴承检测的重要性与技术要求
推力关节轴承作为机械传动系统中的核心部件,广泛应用于风电设备、工程机械、航空航天等领域。其功能是在承受轴向载荷的同时实现旋转运动,对设备运行稳定性、传动效率和使用寿命具有决定性作用。由于长期处于高速、重载、高低温交变等复杂工况下,推力关节轴承的检测工作成为保障设备安全运行的重要环节。根据GB/T 307.1-2017《滚动轴承 向心轴承公差》及ISO 76:2006等相关标准要求,必须建立包括几何尺寸、材料性能、动态承载能力在内的18项关键检测指标体系。
核心检测项目分类
1. 尺寸精度检测
采用三坐标测量仪对轴承内径、外径、滚道圆度进行0.001mm级精密测量,重点检测滚道工作面与基准面的垂直度误差。按照DIN 620-2标准,推力球轴承的轴向游隙应控制在0.02-0.05mm范围内,使用专用塞规进行多点位检测。
2. 表面质量评估
通过三维表面轮廓仪对滚道表面粗糙度进行Ra≤0.2μm级的检测,配合金相显微镜观察表面是否存在微观裂纹、剥落等缺陷。根据ASTM E45标准,硬质层厚度需达到0.3-0.5mm,维氏硬度应稳定在HV700-900区间。
3. 材料性能测试
采用光谱分析仪对材料成分进行定量检测,确保GCR15钢的碳含量(0.95-1.05%)、铬含量(1.30-1.65%)符合YB9-68标准。冲击试验需满足-40℃环境下≥30J的冲击功要求,晶粒度应达到ASTM 8级以上。
4. 动态性能测试
在轴向加载试验台上模拟实际工况,按照ISO 281标准进行2000小时耐久试验。检测项目包括:额定动载荷下的温升不超过45℃、振动值≤20μm、噪声等级≤65dB(A)。特殊工况轴承还需进行200万次循环的加速寿命试验。
5. 耐腐蚀性检测
依据GB/T 10125盐雾试验标准,进行480小时中性盐雾试验。表面处理后的轴承应达到9级及以上腐蚀等级,表面氧化膜厚度需保持8-12μm,且经过30次热震循环后无剥落现象。
齐全检测技术应用
当前主流检测体系已引入工业CT无损探伤、激光散斑应力分析、声发射故障预警等智能化技术。其中X射线衍射法可精确测量残余应力分布,数字图像相关技术(DIC)能实现0.5μm级的微应变监测,确保检测数据可比对、可追溯。
常见问题与解决策略
检测过程中常出现的滚道偏摆超标问题,多源于热处理畸变,建议采用分级淬火工艺。针对早期点蚀现象,应重点检测润滑剂清洁度(NAS 6级以下)和装配预紧力(控制在额定载荷的15-20%)。建立基于大数据分析的预测性维护模型,可提升故障预警准确率35%以上。
完善的推力关节轴承检测体系应涵盖材料、工艺、性能的全维度验证。建议企业建立包含22项过程控制点的质量管理流程,配备符合ISO/IEC 17025标准的检测实验室,采用自动化检测设备将单件检测时间缩短至45分钟以内,切实保障关键零部件的可靠性。
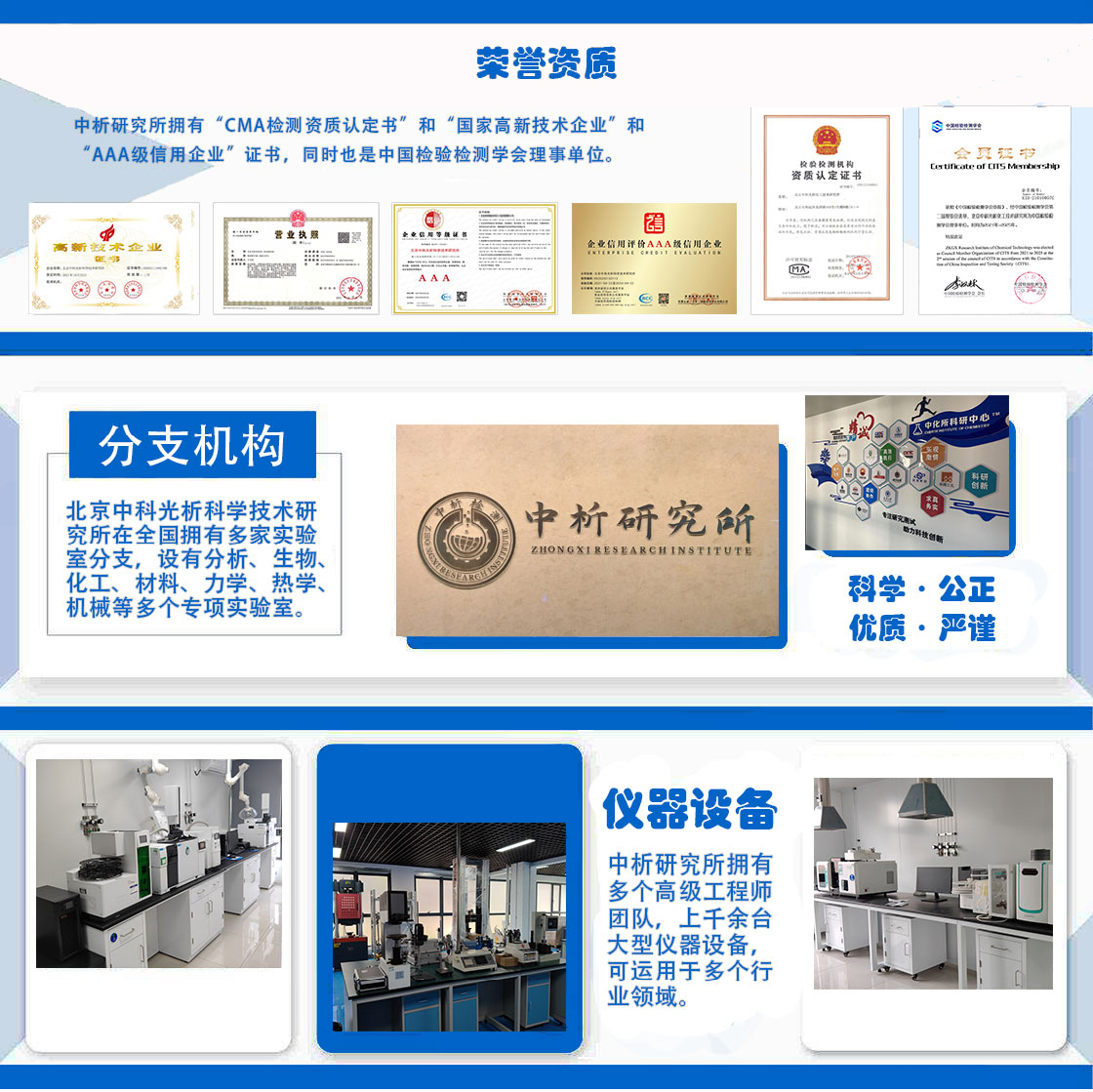
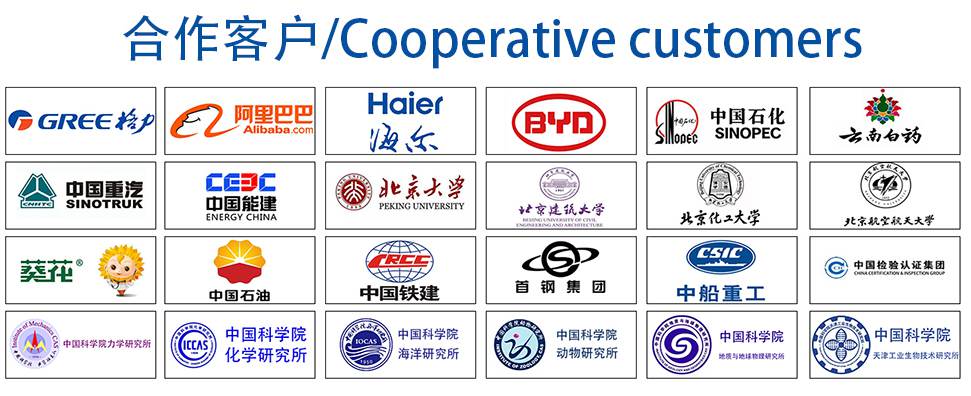