压力控制阀检测项目及技术要求
压力控制阀作为液压系统、气动系统及工业设备中调节压力的核心组件,其性能稳定性直接影响设备运行安全与效率。为确保阀门在高压、频繁启闭等工况下的可靠性,需通过系统化的检测项目验证其密封性、响应速度、疲劳寿命等关键指标。根据GB/T 8105-2017《液压阀试验方法》及行业规范,压力控制阀的全面检测通常包含以下核心内容:
1. 密封性能检测
采用氮气或液体介质在1.1倍标称压力下进行保压测试,观察30分钟内压降是否≤3%。重点检查阀体结合面、活塞杆密封处及焊缝泄漏情况,需通过荧光检漏或气泡法判定微渗漏等级,要求达到ISO 15848-1 CLASS B级密封标准。
2. 启闭动作响应测试
利用高速压力传感器记录阀门从关闭到完全开启的时间,标准要求响应时间≤0.5秒。同步监测压力震荡幅度,在阶跃压力变化时震荡衰减时间应控制在2秒内,确保阀门动态稳定性符合ASME B16.34规范。
3. 压力-流量特性验证
在流量试验台上模拟不同开度工况,绘制压差-流量曲线。要求阀门在80%额定流量时压降≤0.2MPa,且线性度偏差不超过±5%。需特别验证低压差(0.05MPa)条件下的最小可控流量值。
4. 疲劳寿命试验
执行连续5000次全行程循环测试,每1000次循环后进行性能复测。试验后泄漏量增加值不得超过初始值的20%,阀芯表面磨损深度需≤0.02mm,弹簧刚度变化控制在±5%范围内。
5. 环境适应性检测
包括高温(120℃×24h)、低温(-40℃×24h)交变试验,以及盐雾(5%NaCl溶液×96h)腐蚀测试。要求试验后动作阻力变化≤15%,密封件硬度变化不超过邵氏5度,金属部件无可见点蚀现象。
通过上述检测体系可全面评估压力控制阀的综合性能,建议建立每8000工作小时或12个月的定期检测机制。对核电站、石化装置等关键场景,还应增加振动频谱分析及应力腐蚀开裂(SCC)专项检测,确保阀门在全生命周期内保持精准的压力调控能力。
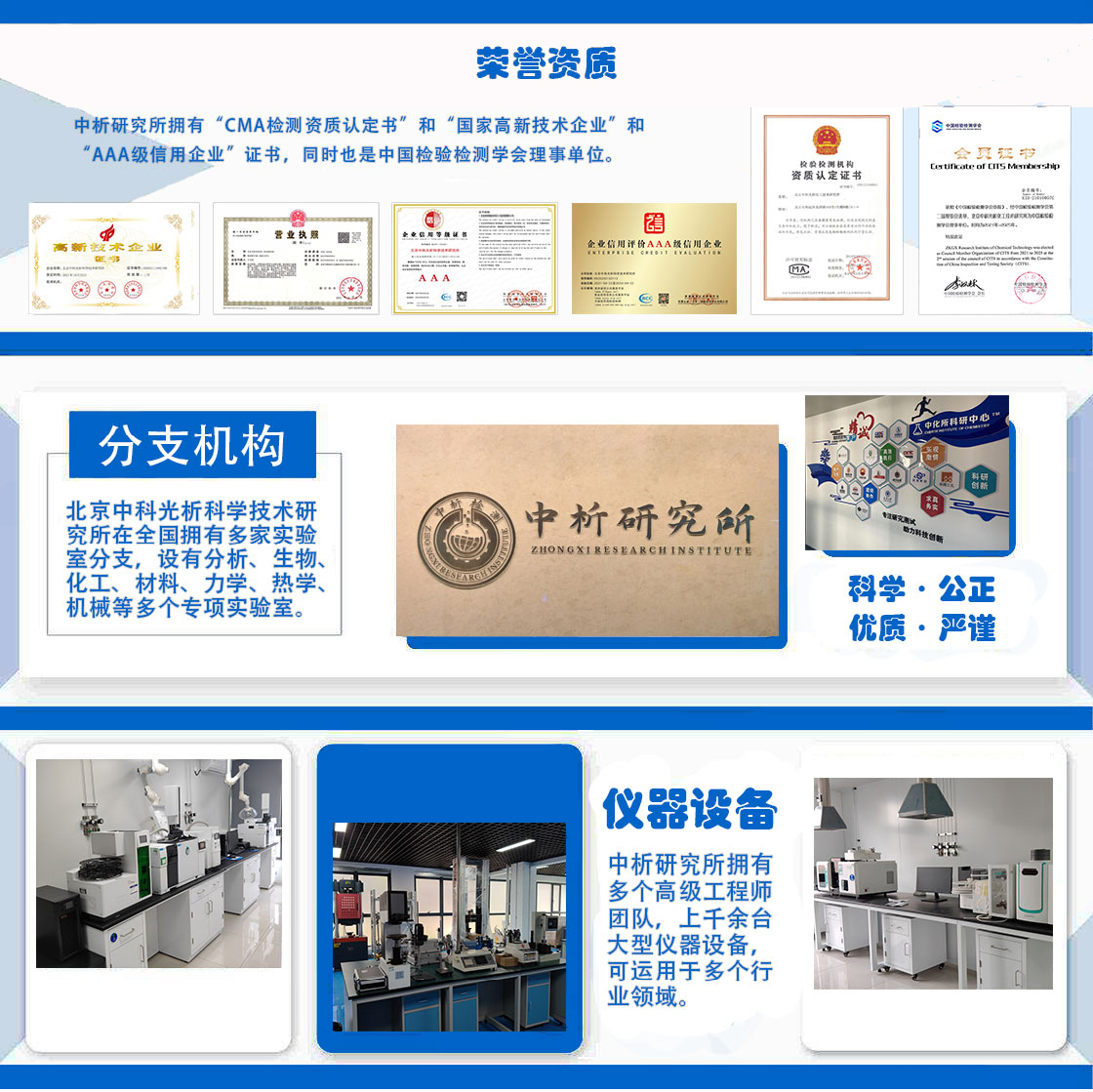
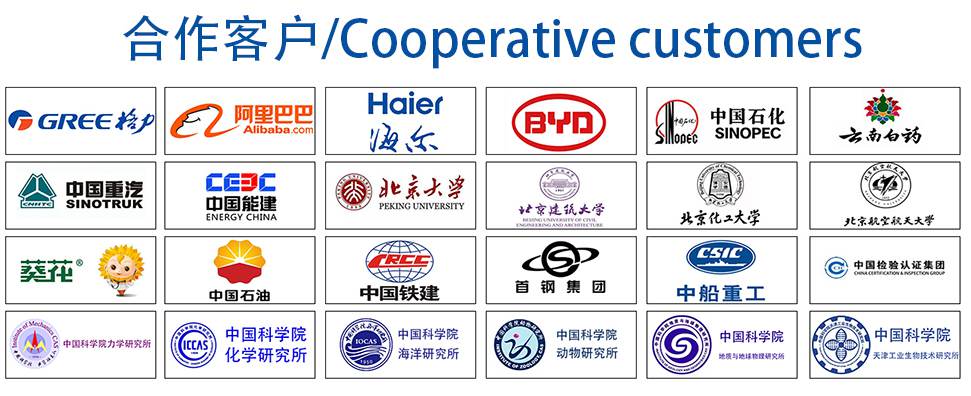