浮子检测项目与技术要点解析
浮子作为液位测量、流量控制及安全防护系统的核心组件,其性能可靠性直接关系到工业设备、汽车油箱、供水系统等领域的运行安全。随着自动化程度的提升和工艺要求的精细化,浮子检测已发展成为涵盖材料特性、结构完整性、功能稳定性等多维度的系统性质量验证过程。本文针对浮子检测的关键项目展开技术解析,建立从基础参数到动态性能的完整检测体系。
1. 外观与尺寸检测
通过数字影像测量仪与三维扫描技术,精确检测浮子的直径、壁厚、接缝平整度等几何参数,误差控制需达到±0.05mm级别。同步进行表面缺陷检测,利用高倍显微镜识别裂纹、气泡、毛刺等微观瑕疵,确保浮子结构完整性。
2. 密封性能测试
采用氦质谱检漏法或压力衰减法,对浮子进行0.2-0.5MPa的加压测试,历时30分钟观察泄漏率变化。重点检测焊接部位、注塑接合处等易泄露区域,泄漏速率需控制在1×10⁻⁶ mbar·L/s以下。
3. 浮力特性验证
建立密度梯度测试系统,使用高精度电子天平配合液体密度计,测量浮子在标准液体(水/油)中的浮重比。要求有效浮力值达到设计标准的105%-110%,并验证不同倾斜角度下的浮子姿态稳定性。
4. 材料特性分析
通过光谱仪进行材质成分验证,结合差示扫描量热法(DSC)检测高分子材料的玻璃化转变温度。进行盐雾试验(ASTM B117标准)和应力开裂测试,评估材料的耐腐蚀性和抗老化性能。
5. 动态响应测试
在模拟工况环境下,使用高速摄像系统记录浮子随液位变化的运动轨迹,测量其上升/下降响应时间。要求全量程运动误差不超过±1.5%,重复定位精度达到0.3mm,确保信号输出的实时性和准确性。
6. 环境适应性试验
进行温度循环测试(-40℃至120℃)、振动测试(频率5-2000Hz)和压力脉冲试验,模拟极端工况下的性能表现。检测项目需覆盖500次温度冲击循环和10⁷次压力脉冲,验证浮子的长期使用可靠性。
7. 电磁兼容性检测
对于带有电子元件的智能浮子,需进行辐射抗扰度(EN 61000-4-3)和静电放电(IEC 61000-4-2)测试,确保在复杂电磁环境下的信号传输稳定性,电磁干扰水平需低于-60dBm。
通过上述系统性检测流程的实施,可有效识别浮子产品的潜在缺陷,提升产品合格率约30%-45%。现代检测体系已逐步融合AI缺陷识别、物联网实时监控等齐全技术,推动浮子检测向智能化、高精度方向发展,为工业自动化和精密控制领域提供可靠的质量保障。
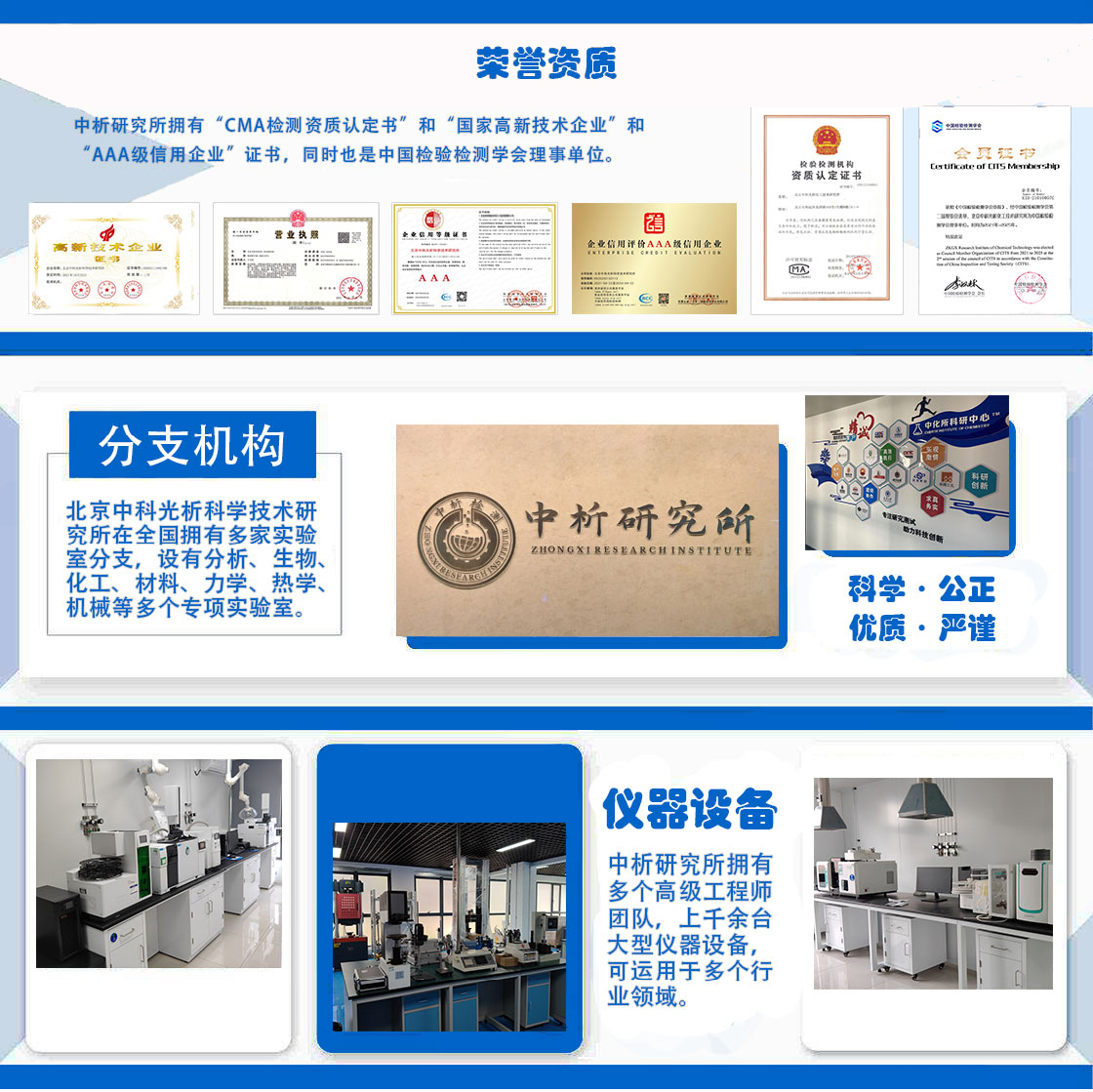
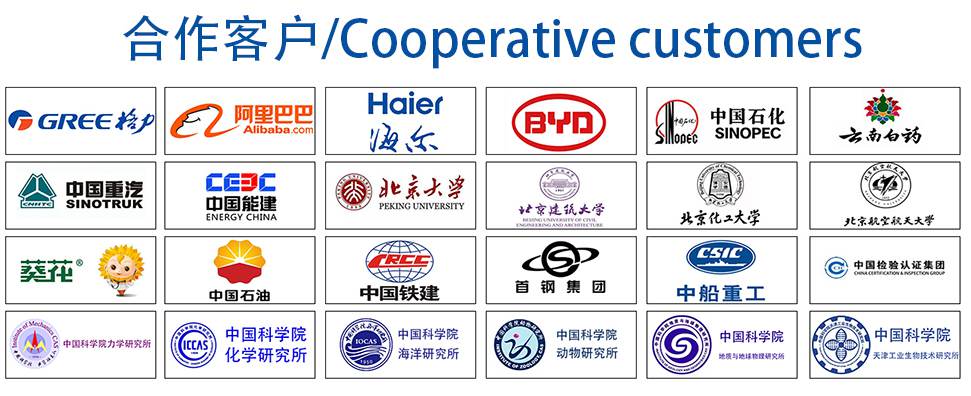