收获后处理机械检测的重要性与实施要点
在现代农业生产体系中,收获后处理机械承担着粮食去杂、干燥、分选、包装等关键环节的作业任务。随着农业机械化程度的不断提升,这些设备的运行稳定性直接关系到农产品质量、存储安全及经济效益。据统计,因机械故障导致的粮食损耗约占年总产量的3%-5%,实施科学规范的机械检测成为保障农业生产效益的重要技术手段。
核心检测项目体系
完整的收获后处理机械检测体系包含六大核心模块:机械性能检测、电气系统检测、安全防护检测、作业精度检测、自动化控制检测以及环保指标检测。检测过程中需结合GB/T 21962-2020《农业机械通用技术条件》等国家标准,运用振动分析仪、红外热像仪、激光校准仪等专业设备进行精准测量。
关键部件专项检测
1. 传动系统检测:重点检查皮带轮同轴度偏差(应≤0.5mm/m)、链条张紧度(垂直摆动量控制在10-15mm)、齿轮啮合间隙(模数<5的齿轮间隙应≤0.2mm)等参数。采用频谱分析法诊断轴承故障,通过振动速度值判定(优质轴承<4.5mm/s)
2. 筛分装置检测:使用标准筛样进行分选效率测试,要求杂质去除率≥98%,破损率≤0.5%。动态检测筛网振幅(推荐3-5mm)和振动频率(20-25Hz),确保筛面物料均匀分布。
智能化检测技术应用
新型检测方案已集成物联网监测系统,通过在关键节点布设压力传感器(量程0-10MPa,精度0.5%FS)、温度传感器(-20-150℃范围,±0.5℃)等智能元件,实时采集设备运行数据。结合大数据分析平台,可提前72小时预判85%以上的潜在故障,检测效率较传统方式提升40%。
检测周期与标准维护
建议执行三级检测制度:日常点检(每班次)、定期检测(500工作小时)、大修检测(3000工作小时)。重点监测部位的磨损量标准为:轴类零件≤0.1mm、壳体类≤0.3mm、筛网磨损面积≤15%。建立完整的检测档案,记录每次检测的振动值、温度变化曲线等关键数据,为设备寿命预测提供依据。
通过系统化的检测维护,可使收获后处理机械的有效作业率提升至92%以上,能耗降低18%-22%,同时将设备突发故障率控制在3%以内,为农业产后环节的提质增效提供有力保障。
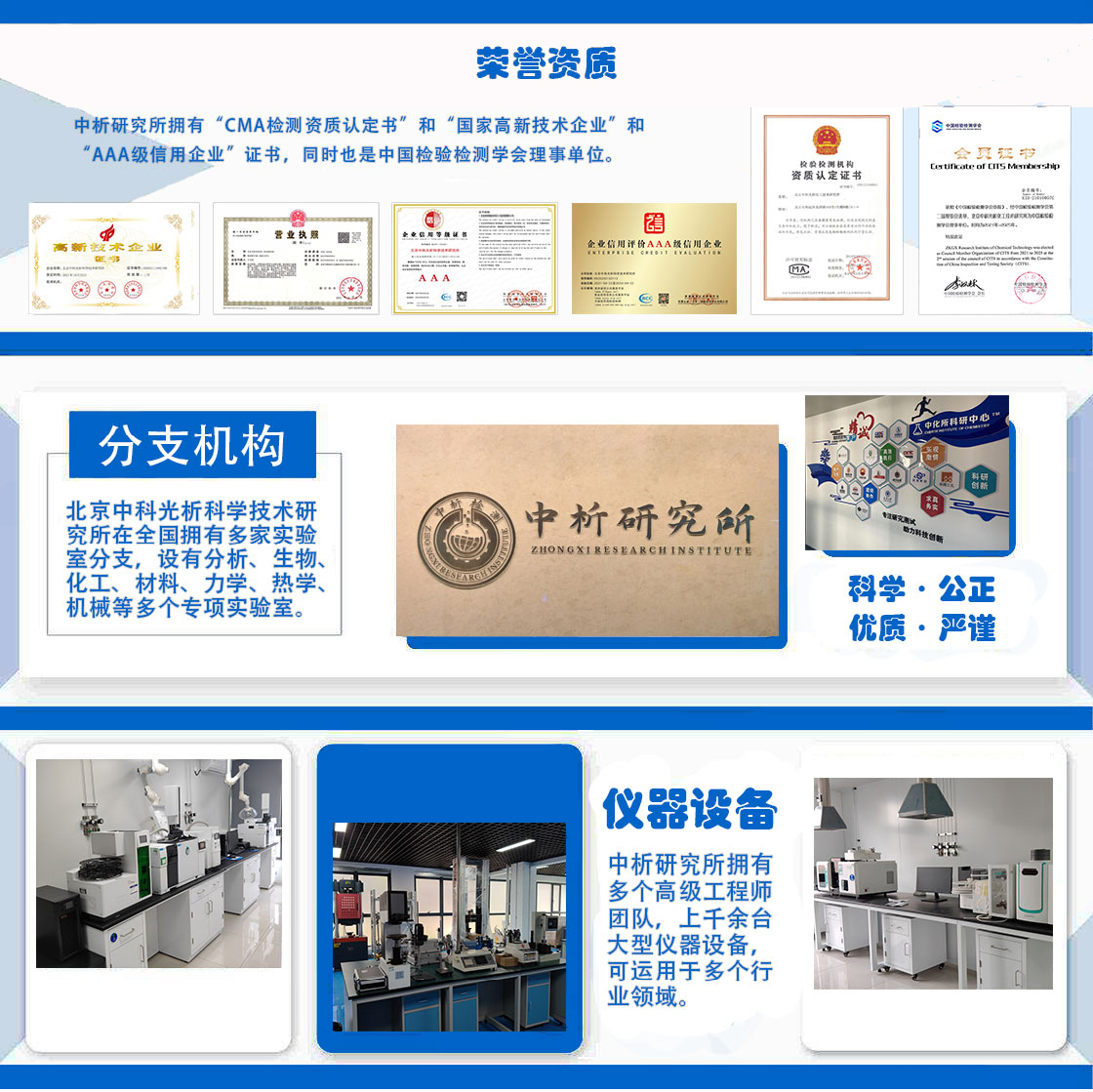
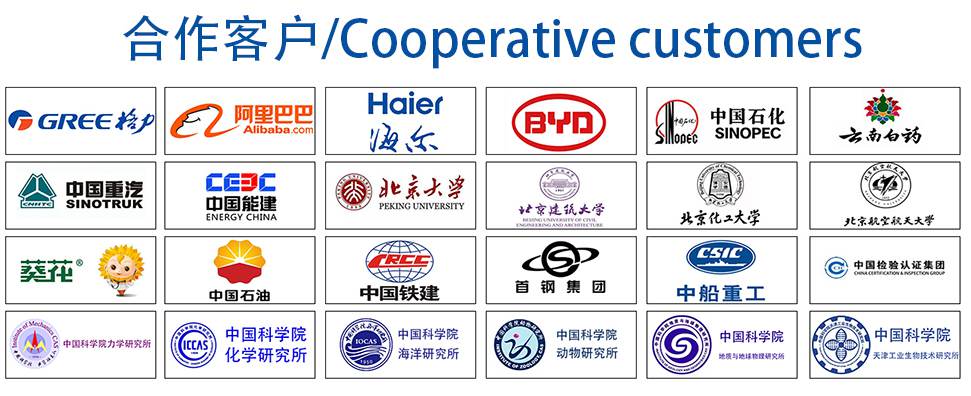