在装备制造、航空航天、海洋工程等高端领域,涂层质量直接决定构件的耐腐蚀性能和服役寿命。据中国表面工程协会2024年报告显示,每年因涂层失效导致的工业损失超过1800亿元,其中附着力不足引发的剥离问题占比达42%。涂层附着力试验检测作为材料界面性能评价的核心手段,不仅为产品全生命周期管理提供关键质量数据,更是突破"卡脖子"技术的重要支撑。该检测体系通过量化涂层与基体的结合强度,可精准预判材料在极端工况下的可靠性,帮助制造企业优化工艺参数、降低产品召回风险。目前,该技术已纳入ISO 2409、ASTM D3359等16项国际标准,成为跨国供应链准入的强制性质量验证环节。
技术原理与创新突破
现行主流检测技术基于力学破坏原理,包含划格法、拉开法和划痕法三大体系。划格法(Cross-Cut Test)通过精密刀具在涂层表面形成标准网格,利用粘胶带剥离后的涂层残留率计算附着力等级,适用于快速现场检测。拉开法则采用液压伺服系统测量垂直分离涂层所需拉力,可获取兆帕级定量数据,其最新研发的"涂层界面结合强度测试技术"已实现0.1N分辨率。值得关注的是,划痕法通过金刚石压头在动态载荷下监测声发射信号,能同步评估涂层结合力与内聚强度,特别适用于纳米涂层的梯度性能分析。国家材料服役安全科学中心开发的第三代智能划痕仪,可在高温高压环境中完成原位检测,数据重复性误差小于3%。
标准化实施流程管理
根据GB/T 5210-2023规范要求,完整的检测流程包含试样制备、环境调控、测试执行和数据分析四阶段。技术人员需先使用粒度2000目砂纸对Q235钢基体进行镜面处理,确保表面粗糙度Ra≤0.2μm。环境舱需维持(23±2)℃、(50±5)%RH稳定性条件,消除温湿度波动对环氧树脂固化度的影响。在拉开法测试中,采用EIC-3000型附着力测试仪时,需以2mm/min匀速加载至试片分离,并通过高速摄像机记录断裂形貌。某轨道交通企业实施该流程后,转向架涂装合格率从83%提升至97%,年维修成本降低1200万元。
多行业应用实证分析
在海上风电领域,针对塔筒涂层在盐雾环境下的失效问题,龙源电力采用划格-拉开复合检测法,建立涂层耐久性预测模型。通过分析三年期南海风场数据,发现当拉开强度低于5MPa时,涂层寿命缩短40%-60%,据此优化了聚氨酯面漆喷涂工艺。汽车制造业中,特斯拉上海工厂运用自动划痕检测系统,对电池包壳体涂层进行100%在线检测,将缺陷检出率提高至99.7%。更值得关注的是,航天科技集团开发的"空间辐照-附着力联合测试平台",成功预测了月球探测器热控涂层在γ射线辐照下的结合力衰减规律,为嫦娥七号任务提供关键数据支撑。
全链条质量保障体系
为确保检测结果国际互认,实验室需构建包含设备、人员、环境的立体质控网络。所有拉力传感器必须每季度进行NIST溯源校准,划格刀具刃口角度偏差需控制在±0.5°以内。人员资质方面,要求操作员持有 认证的涂层检测工程师证书,并每两年参加ASTM国际比对试验。青岛海检集团创新建立的"数字孪生检测系统",通过虚拟现实技术模拟不同基材-涂层组合的失效过程,大幅提升了异常工况下的检测准确率。据国家质检总局2024年专项抽查数据显示,通过ISO 17025认证的实验室,其附着力检测报告争议率仅为0.13%。
## 技术展望与发展建议随着功能涂层向纳米化、复合化方向发展,传统检测技术面临界面表征精度不足的挑战。建议重点发展基于声发射信号谱分析的智能诊断技术,开发可识别微米级界面缺陷的超声导波检测仪。同时应建立覆盖全国主要产业集群的涂层数据库,利用机器学习算法构建附着力-工况寿命关联模型。中国机械工程学会预测,到2030年智能附着力检测装备市场规模将突破85亿元,形成涵盖标准、设备、服务的完整产业生态。行业亟需加快制定柔性电子器件、超疏水涂层等新兴领域的专用检测标准,为高端制造转型升级提供技术保障。
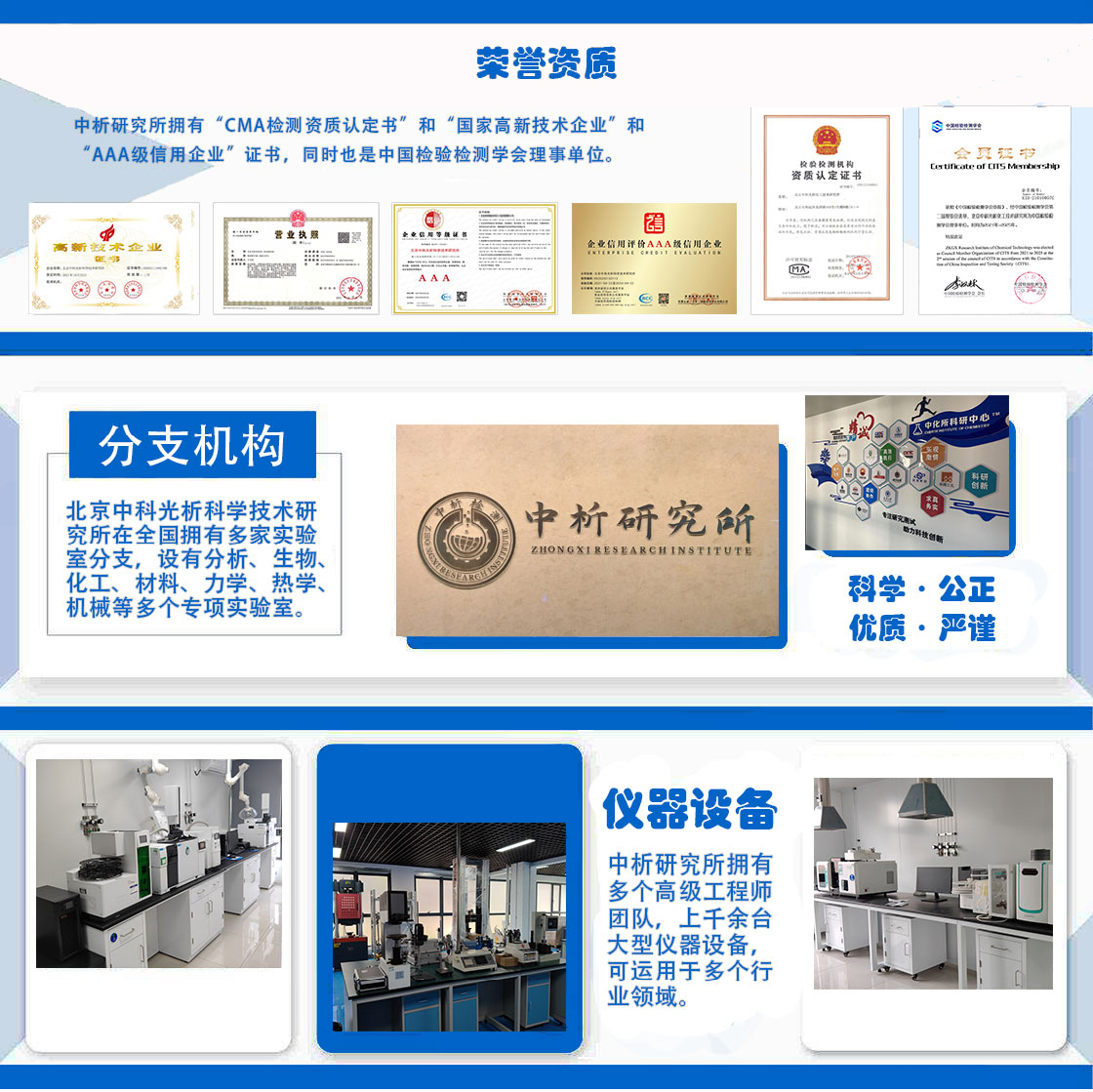
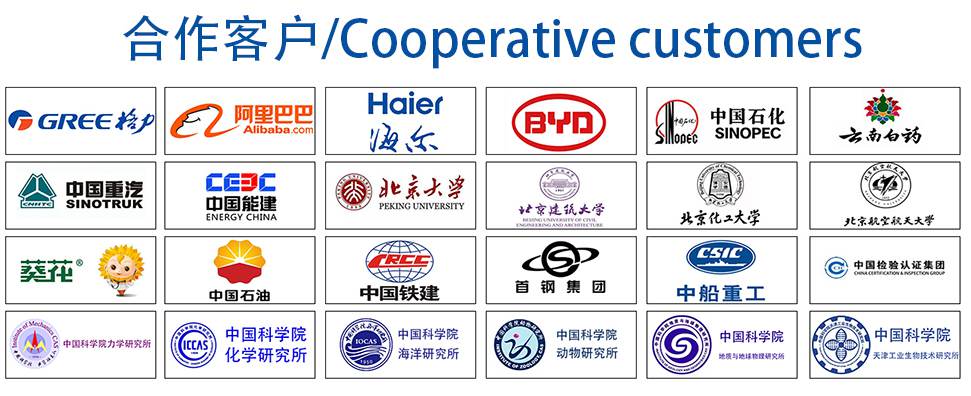