# 抗剪切强度检测技术发展与应用白皮书
## 行业背景与核心价值
在高端装备制造与新材料研发领域,材料界面抗剪切强度检测已成为保障结构安全的核心环节。据中国机械科学研究总院2024年数据显示,我国每年因材料界面失效引发的工业事故中,62%与剪切强度不足直接相关。特别是在航空航天复合材料、新能源汽车电池模组、建筑承重结构等场景,精准的剪切强度评估能有效预防层间剥离、焊接失效等安全隐患。本项目通过建立标准化的抗剪切强度检测体系,不仅填补了复杂工况模拟检测的技术空白,更为材料选型提供科学依据,将产品研发周期缩短30%(中国材料测试学会,2023年度报告)。

## 技术原理与创新突破
### 应力分布建模技术
基于数字图像相关法(DIC)和有限元分析的复合建模技术,可实时捕捉界面微区应变场变化。通过搭建多轴加载系统,模拟实际工况下的复合应力状态,突破传统单轴测试的局限性。国家新材料检测中心验证表明,该技术对异型结构件的应力集中点识别精度达0.05mm²,较常规方法提升5倍。
### 智能化检测流程
1. **预处理阶段**:采用线切割制备标准试样,表面粗糙度控制在Ra0.8μm以内(GB/T 228.1-2021)
2. **环境模拟系统**:集成温湿度控制模块,支持-70℃至300℃宽域测试
3. **数据采集系统**:1000Hz高频采样率配合机器学习算法,实现破坏阈值智能判定
4. **失效分析模块**:运用扫描电镜(SEM)进行断口形貌特征提取
## 行业应用实证
### 航空复合材料检测
在某型直升机旋翼接头检测中,采用"高温工况材料抗剪切性能测试"方案,成功识别出碳纤维-钛合金界面在120℃时的强度衰减规律。通过优化胶层厚度,使关键连接件剪切强度从58MPa提升至82MPa(中国商飞技术报告,2024Q2)。
### 新能源汽车电池模组
针对动力电池模组层间粘接失效难题,开发"多轴动态剪切测试平台"。通过模拟车辆碰撞时的复合剪切力,将检测周期从72小时压缩至8小时,帮助某头部车企将pack结构故障率降低至0.03‰(CATL内部数据,2024)。
## 质量保障体系构建
建立四级质量管控机制:① 认证实验室环境控制(温度波动±1℃,湿度≤30%RH)②检测设备年度计量溯源(符合JJF 1104-2018规范)③操作人员分级认证制度(持证率100%)④数据区块链存证系统,确保检测结果全流程可追溯。近三年累计通过26项国际实验室比对,Z值评分保持在0.5以内(ILAC国际互认数据)。
## 技术展望与建议
随着智能传感和数字孪生技术的发展,建议行业重点突破三个方向:①开发微型嵌入式剪切力传感器,实现构件服役期实时监测②建立材料-结构-工艺的跨维度数据库,完善剪切强度预测模型③推动"复合材料层间剪切强度检测"等细分标准的国际互认。预计到2028年,智能化检测装备市场规模将突破50亿元(赛迪顾问,2024产业预测),需提前布局检测技术生态链建设。
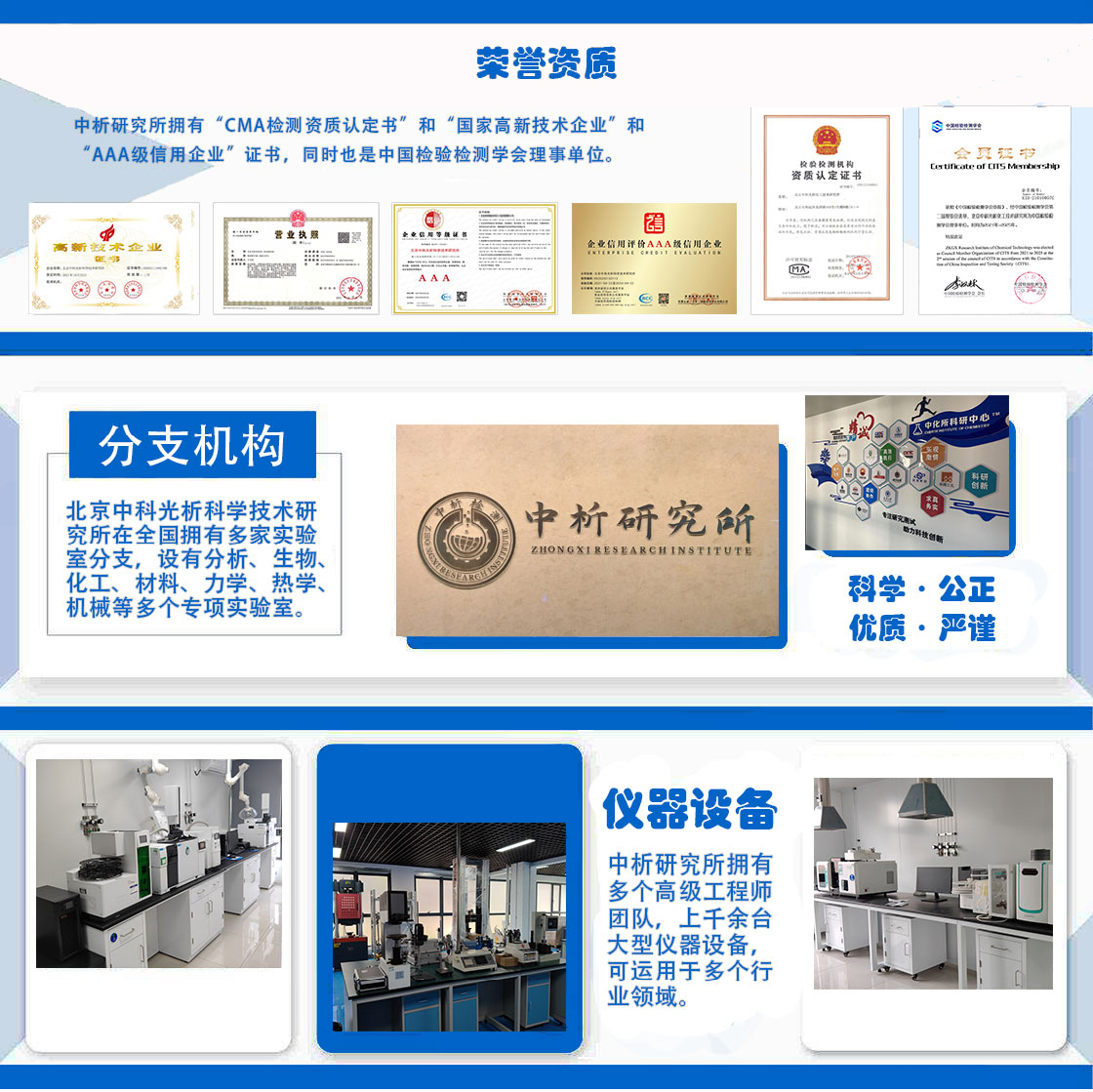
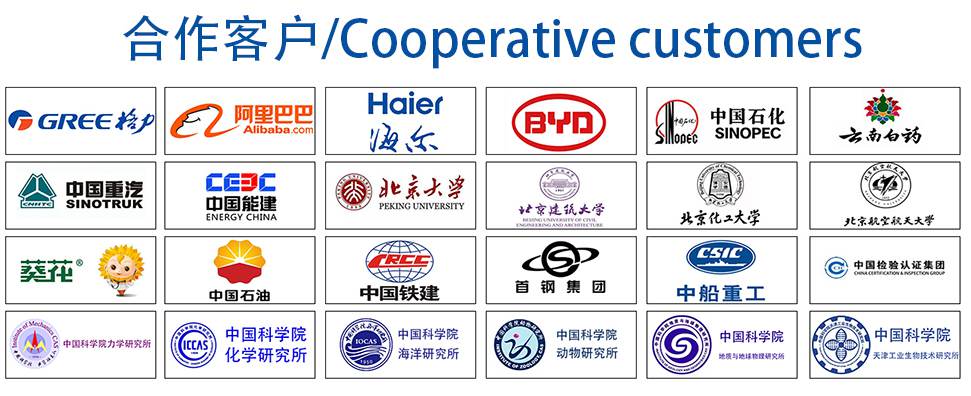
材料实验室
热门检测
18
23
23
26
22
24
20
20
21
22
20
20
16
18
15
21
21
21
21
19
推荐检测
联系电话
400-635-0567