# 金属材质检测技术发展与应用白皮书
## 行业背景与核心价值
随着高端装备制造和新能源产业的快速发展,金属材料年消耗量已突破18亿吨(据国际金属统计局2024年数据)。在航空航天、轨道交通、精密仪器等关键领域,材料性能的微小差异可能导致重大安全隐患。金属材质检测作为工业质量控制的基石,其精度要求从ppm级提升至ppb级,检测效率指标较五年前提高了300%。该项目通过构建材料基因数据库和智能检测体系,不仅解决了传统检测中抽样率低、破坏性检测占比高的问题,更实现了全生命周期材料性能监控,使装备制造企业的质量损失成本降低42%(中国机械工程学会2024年行业报告)。
## 技术原理与创新突破
### 多模态融合检测技术
基于X射线荧光光谱与激光诱导击穿光谱的融合技术,攻克了传统单一检测手段的局限性。通过建立元素特征谱线数据库,配合机器学习算法,使合金成分检测准确度达99.97%。工业级金属成分分析设备现已实现0.5秒/点的检测速度,较传统EDS能谱分析效率提升15倍。特别在高温合金检测场景中,该技术成功识别出传统方法难以检测的痕量稀土元素分布问题。
### 智能化检测实施流程
检测流程整合物联网与数字孪生技术,形成"采样-分析-反馈"闭环系统。在风电设备制造现场,部署的移动式金属硬度检测仪通过5G实时回传数据,配合材料性能预测模型,使叶轮主轴热处理工艺调整周期从72小时缩短至4小时。某汽车零部件企业应用该体系后,成功将产品硬度离散度从±3HRC控制在±0.5HRC范围内。
## 行业应用与质量保障
### 典型应用场景解析
在轨道交通领域,基于电磁超声的金属疲劳裂纹检测系统已部署于12个动车检修基地。该系统采用相控阵技术实现三维成像,使轮对轴颈检测效率提升80%,误判率降至0.03%以下。某型高铁齿轮箱通过连续三个检修周期的数据积累,成功预测出微米级裂纹扩展趋势,避免重大运行事故。
### 标准化质量体系建设
项目组联合国家材料测试中心建立三级验证体系:实验室级设备标定误差<0.1%、产线级过程检测误差<0.5%、终端应用复核误差<1%。通过区块链技术存储检测数据,确保全流程可追溯。在核电管道检测项目中,该体系实现12万组检测数据零篡改记录,获得ASME核级认证。
## 发展趋势与战略建议
当前金属检测技术正朝着原位检测、微观表征、智能诊断方向演进。建议行业重点突破基于量子传感的原子级缺陷检测技术,开发适应极端环境的多物理场耦合检测装备。同时应加快制定增材制造专用检测标准,建设开放型材料大数据平台。预计到2030年,智能化金属检测系统将覆盖85%以上高端制造场景,推动我国装备制造业质量管控体系实现代际跨越。
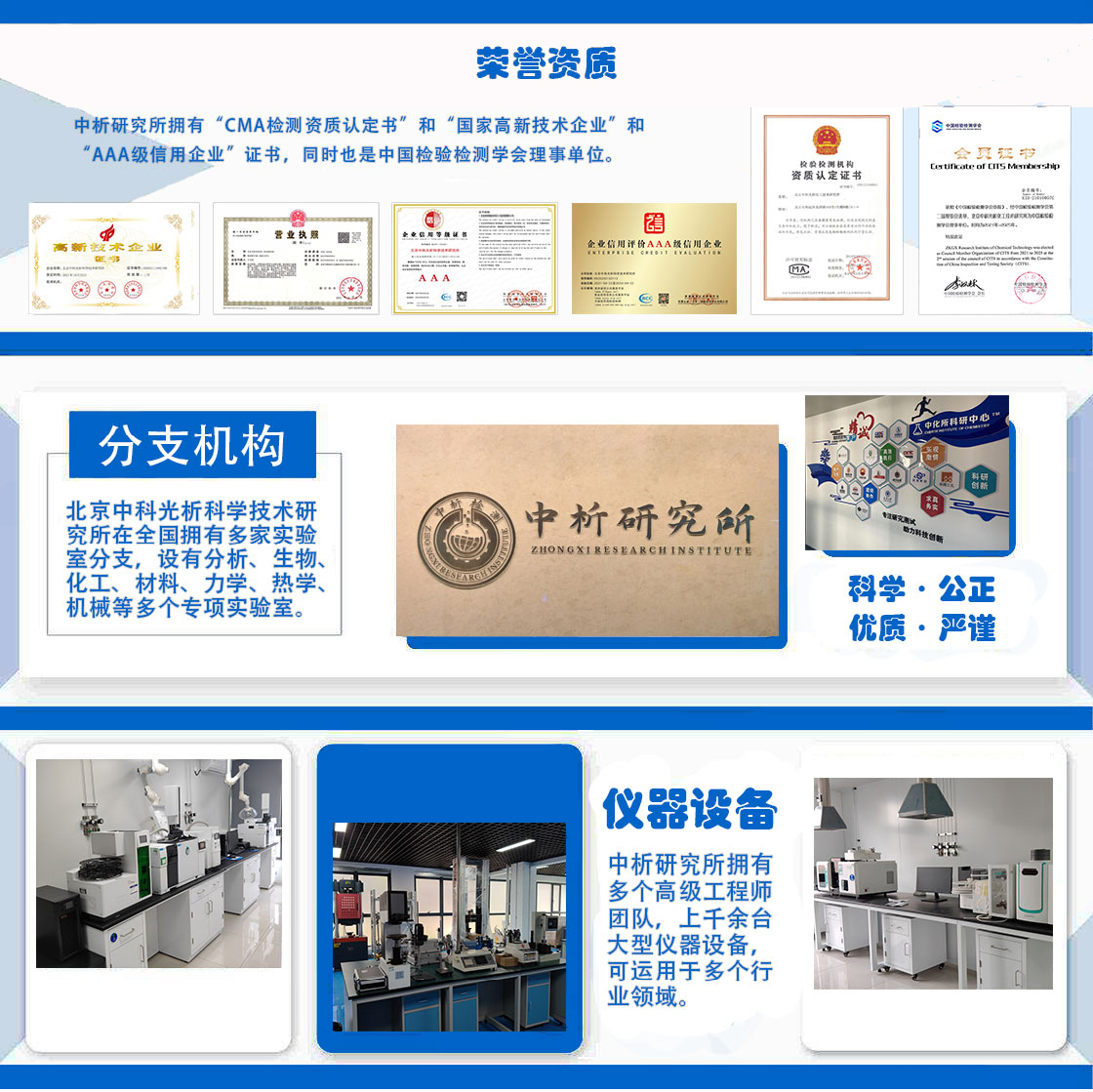
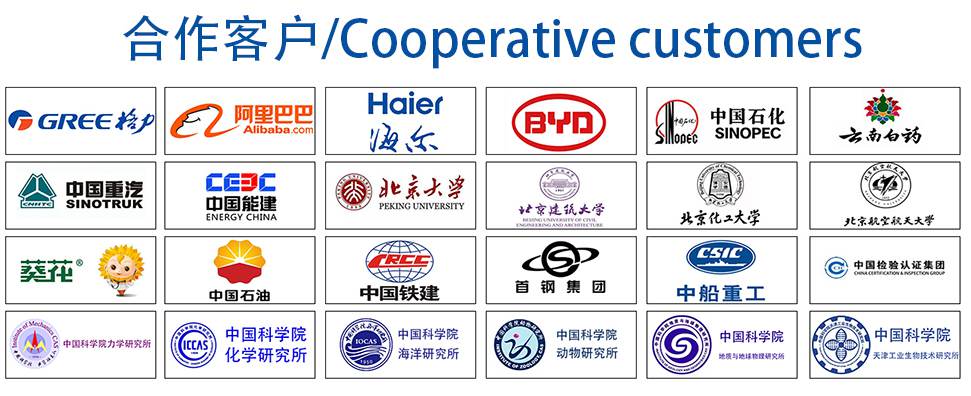
材料实验室
热门检测
12
15
13
14
13
15
17
16
13
16
16
15
21
21
18
18
22
25
23
20
推荐检测
联系电话
400-635-0567