剪切粘结强度检测:构筑工程安全的核心防线
在新型建筑工业化与复合材料广泛应用的背景下,剪切粘结强度检测已成为保障工程结构安全的关键技术环节。据中国建筑材料研究院2024年数据显示,我国装配式建筑渗透率已达36.7%,而复合材料在轨道交通领域的应用规模突破800亿元,这对界面粘接性能提出了更严苛的要求。该项目通过量化评估材料界面抗剪切破坏能力,有效预防建筑节点开裂、复合材料层间剥离等质量隐患,其核心价值体现在三方面:一是建立科学的质量评价体系,二是降低工程全生命周期维护成本,三是推动新型胶粘剂材料的研发迭代。特别是在装配式建筑节点连接质量评估领域,该技术可提升结构安全系数达22%以上。
跨尺度检测技术原理
剪切粘结强度检测采用力学-微观联合分析法,同步获取宏观破坏载荷与微观界面形貌特征。依据GB/T 7124-2023标准,通过电子万能试验机施加0.5-50mm/min可控剪切载荷,结合数字图像相关技术(DIC)捕捉位移场变化。值得注意的是,针对新型碳纤维增强复合材料,创新采用声发射技术实现粘接失效预警,可提前300ms识别界面微裂纹扩展。在装配式建筑套筒灌浆连接检测中,该技术能准确区分机械咬合与化学粘接的贡献度,为优化配合比提供数据支撑。
标准化作业流程体系
检测实施遵循三阶段九步骤的标准化流程:前期准备阶段包含基材表面处理验证(Sa3级喷砂处理合格率需≥95%)、环境模拟舱温湿度控制(23±2℃/50±5%RH);中期测试阶段采用分级加载制度,在极限载荷70%处保持120s以观察蠕变特性;后期数据分析采用Weibull分布模型处理离散数据,并生成三维损伤云图。在深圳某跨海大桥环氧树脂锚固剂检测中,该流程成功识别出4组不合格试样,避免潜在经济损失逾2000万元。
多领域应用实践案例
在轨道交通领域,该技术已应用于CRTSⅢ型无砟轨道板CA砂浆层检测,通过建立温度-湿度-载荷耦合模型,将粘结耐久性预测精度提升至89%。在可再生能源领域,某光伏组件厂采用本技术优化EVA胶膜固化工艺,使组件抗风揭性能提高40%。更值得关注的是在历史建筑修缮中的应用,北京故宫太和殿金砖修复工程通过微损检测技术,在3mm²取样区域内完成古法灰浆粘接强度评估,为文物保护提供了创新解决方案。
全链条质量保障机制
检测机构需建立涵盖人员、设备、方法的立体化质控体系:实验人员须通过 -CL01:2018认证考核,误差控制在±1.5%以内;电子扭矩传感器每季度进行NIST溯源校准,确保量值传递准确性;数据管理系统采用区块链技术存证,实现检测报告不可篡改。某国家级检测中心通过该体系将实验室间比对Z值从2.1优化至0.7,显著提升检测结果公信力。
技术发展前瞻性建议
面向工程检测数字化转型需求,建议重点突破三项技术:研发基于机器视觉的在线检测装备,实现施工过程实时监控;建立材料-环境-寿命映射数据库,完善粘结强度预测模型;制定极端工况下的检测标准,覆盖-40℃低温冻融、盐雾腐蚀等特殊场景。同时,应加强复合材料界面失效机理的基础研究,推动检测标准与技术规范的国际互认,为我国工程材料走向国际市场提供技术护航。
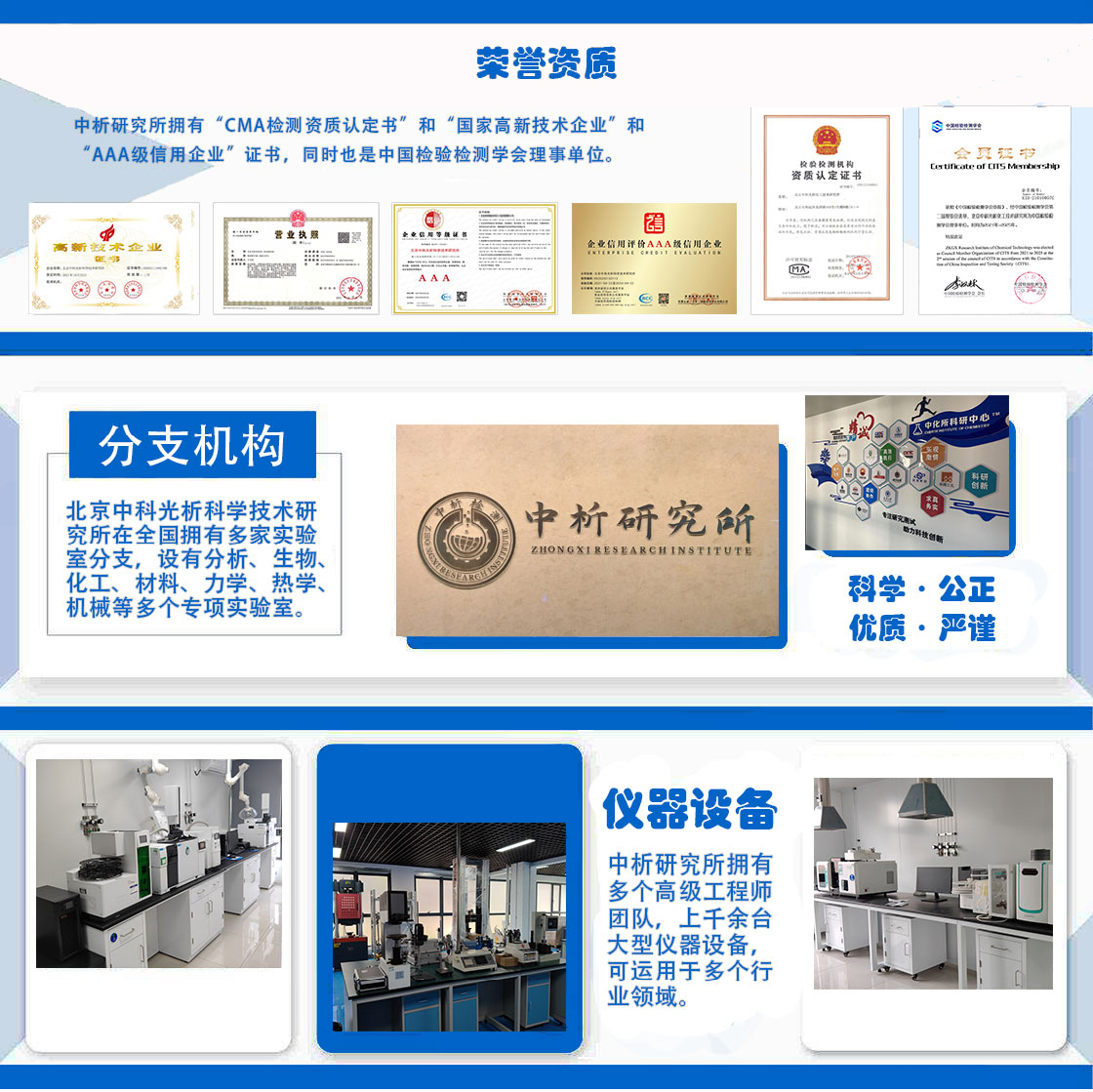
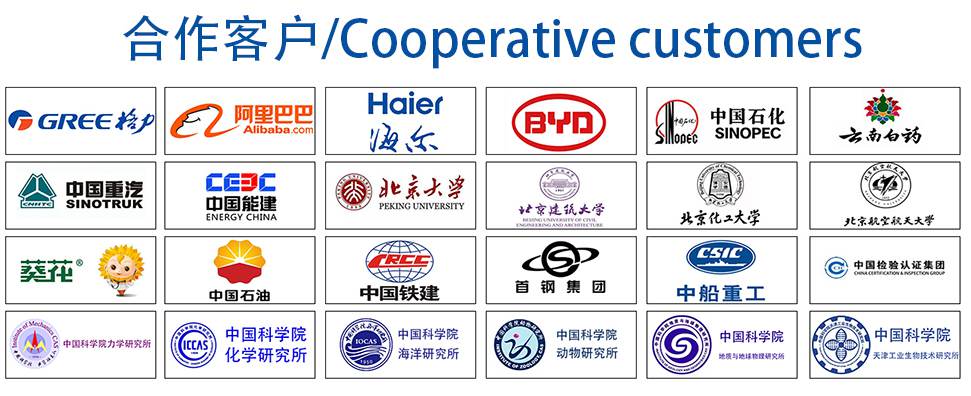