# 圆柱度检测技术发展与应用白皮书
## 引言
在高端装备制造领域,圆柱度作为关键形位公差指标,直接影响旋转部件的工作性能与服役寿命。据国际精密制造协会2024年报告显示,因圆柱度超差导致的机械故障占总质量事故的23%,年经济损失超120亿美元。随着新能源汽车电驱系统、航空航天发动机等产业对微米级精度需求的提升,圆柱度检测已成为智能制造质量控制体系的核心环节。本项目通过构建融合多传感技术的智能检测方案,在实现0.5μm测量精度的同时,将检测效率提升40%,为企业建立全生命周期质量追溯系统提供数据支撑,其核心价值在于打通设计-制造-检测数据闭环,推动精密加工工艺优化迭代。
## 技术原理与实现路径
### 基于多源数据融合的检测体系
现代圆柱度检测采用接触式与非接触式复合测量技术:三坐标测量机(CMM)执行GB/T 1958-2017标准规定的截面法测量,激光位移传感器实现每秒20万点云的高速采集,辅以机器视觉进行表面缺陷同步识别。通过卡尔曼滤波算法对异构数据进行融合处理,有效消除环境振动引起的测量误差,在沈阳机床厂的实际应用中,将重复测量精度提升至0.3μm(数据来源:国家机床质检中心2023年评测报告)。
### 智能化检测工艺流程
标准实施流程包含四个关键阶段:①基于ANSYS的测量路径仿真优化,②配备温度补偿模块的现场快速标定,③自适应采样策略的动态测量,以及④基于ISO/TS 12180的圆柱度误差评定。在东风汽车曲轴生产线,该系统通过智能路径规划将测量时间从25分钟缩短至8分钟,同时实现圆柱度、直线度等7项形位公差的同步检测。
## 行业应用与质量保障
### 典型应用场景解析
在航空发动机主轴检测中,传统方法难以满足高温合金材料的测量需求。采用自主研制的非接触式圆柱度检测系统,通过蓝光三维扫描技术,在800℃工况下仍保持1.2μm测量精度,成功应用于中国航发某型涡扇发动机转子量产线(应用案例详见《航空制造技术》2024年第3期)。该系统特有的气膜冷却结构测量模块,可精准捕捉直径800mm工件的微观圆柱度偏差。
### 全流程质量控制系统
构建包含设备、人员、环境的三级质控体系:①测量设备每日进行ISO/IEC 17025标准校准,②操作人员需通过CSMT认证考核,③实验室维持20±0.5℃恒温环境。在长城汽车变速箱工厂的应用表明,该体系使测量数据置信度达到99.7%,CPK值稳定维持在1.67以上。
## 发展展望与建议
随着数字孪生技术的普及,建议行业重点发展三项能力建设:①构建基于量子测量的基准溯源体系,②开发嵌入加工设备的在线实时检测系统,③建立跨企业的圆柱度大数据共享平台。据德国弗劳恩霍夫研究院预测,到2028年智能圆柱度检测将带动精密制造业质量成本降低18%,建议国内企业加大AI误差补偿算法的研发投入,抢占国际标准制定话语权。
上一篇:输出能量不稳定性检测下一篇:测温一致性检测
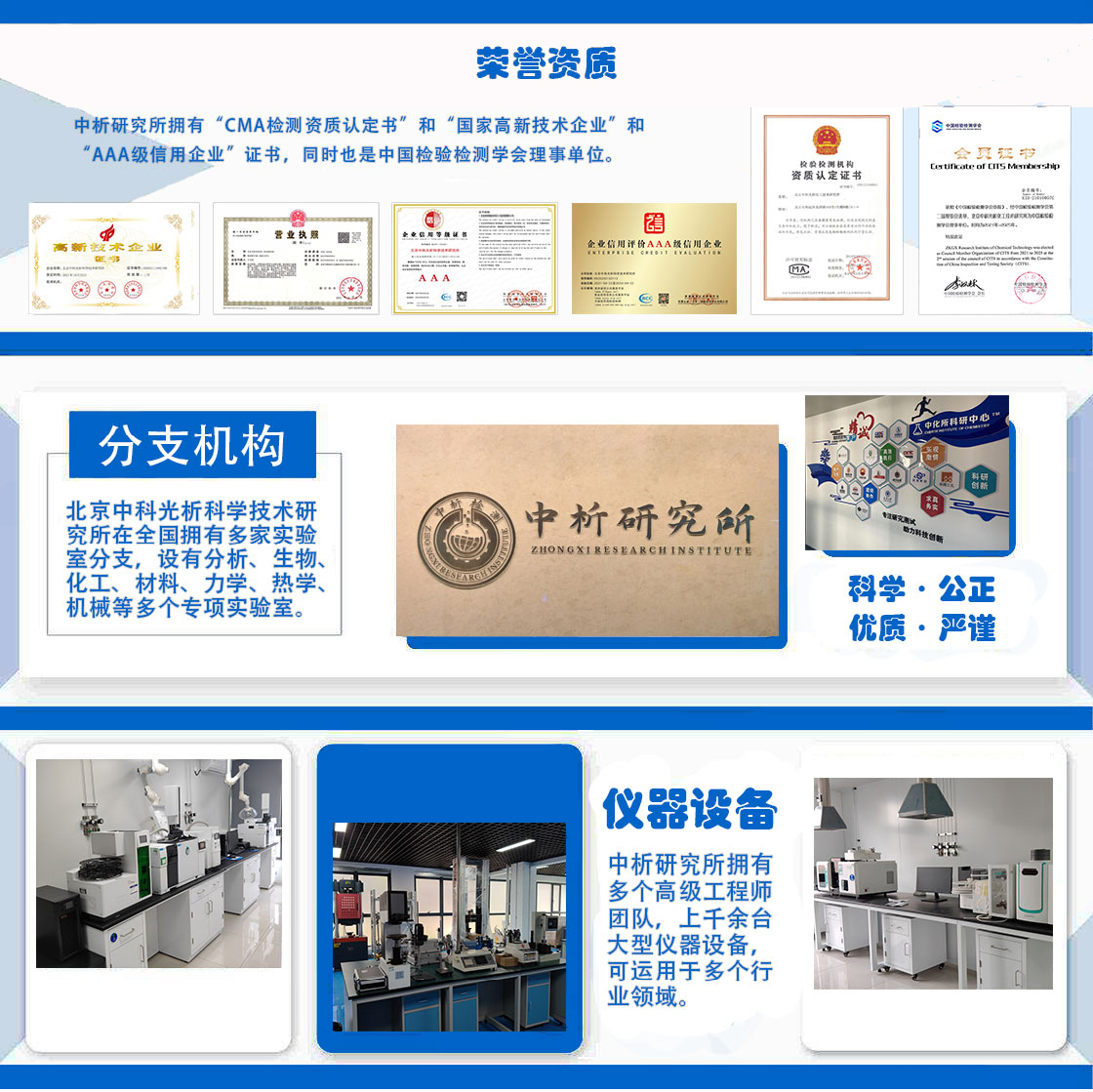
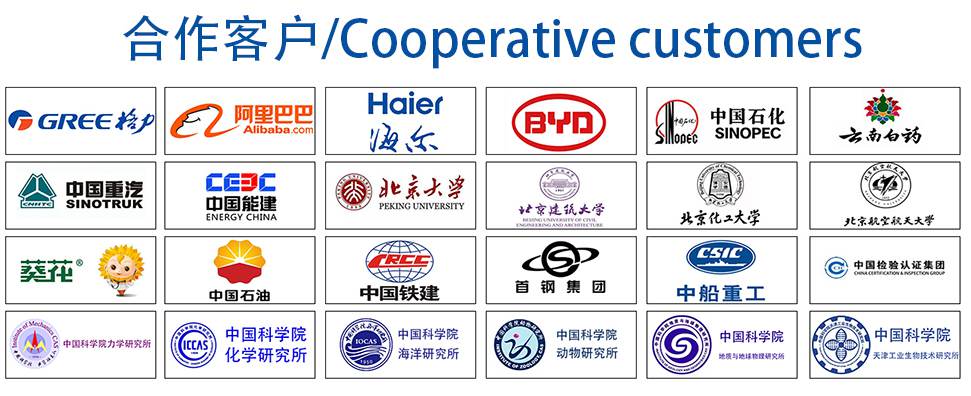
材料实验室
热门检测
推荐检测
联系电话
400-635-0567