在精密光学制造与激光技术领域,光束特性参数检测是确保产品质量的核心环节。据中国光学学会2024年行业报告显示,高功率激光器市场规模已达320亿美元,其中85%的工业级应用场景对光束宽度/直径检测精度提出±2μm的严苛要求。该项目通过建立标准化的光束形貌分析体系,解决了传统检测方法存在的采样误差大、动态范围受限等行业痛点。其核心价值不仅体现在提升激光加工设备的光束质量稳定性,更为光学元件设计验证、生物医学激光治疗等跨领域应用提供了关键数据支撑,据测算可降低高端制造领域15%的工艺调试成本。
基于空间频率分析的检测技术原理
现代光束检测系统采用傅里叶光学与数字图像处理融合技术,通过CCD/CMOS阵列捕获近场和远场光强分布。关键算法采用二阶矩法计算光束直径,其数学表达式为D=4√(⟨x²⟩−⟨x⟩²),符合ISO/TR11146国际标准要求。针对高功率激光束的特殊需求,系统集成热像补偿模块,有效消除热透镜效应导致的测量偏差。值得关注的是,该技术可同步获取M²因子、椭圆度等12项光束质量参数,为激光器性能评估提供多维数据支撑。
五阶闭环检测实施流程
项目实施采用模块化系统架构,分为设备预校准、动态采样、数据处理三大阶段。操作流程严格遵循ASTM E2848-21标准:首先使用NIST溯源的标准光束源进行系统校准,其后通过电动平移台实现0.1μm级精度的空间扫描。数据采集环节采用12bit高速AD转换器,确保在100kHz采样频率下保持0.5%的线性度误差。在半导体晶圆激光切割场景中,该系统成功实现每分钟300次在线检测,将切割线宽波动控制在±0.8μm以内,较传统方法提升3倍效率。
跨行业典型应用案例
在新能源领域,某头部光伏企业采用本方案对激光转印设备的光束特性进行优化,使异质结电池栅线宽度从28±3μm缩减至22±1μm,转换效率提升0.3%。医疗行业应用中,上海某三甲医院的皮秒激光治疗仪通过系统检测,将光斑直径不均匀度从8.3%降至2.1%,显著提升色素性疾病治疗效果。更值得注意的是,在航空航天复合材料加工中,该技术帮助某型号碳纤维部件激光打孔合格率从82%提升至97%,单个部件生产成本降低23%。
全链路质量保障体系
项目构建了覆盖设备-算法-数据的立体化质控网络:硬件层面采用热电双闭环温控系统,确保检测环境温度波动≤0.5℃;软件层面实施ISO/IEC17025标准的测量不确定度评定,关键参数扩展不确定度达U=0.8μm(k=2);数据管理端运用区块链技术实现检测结果全程溯源。经德国PTB实验室验证,系统在连续72小时稳定性测试中,光束直径测量值标准差仅为0.12μm,完全满足工业4.0时代的智能制造需求。
随着量子通信、超快激光等新兴技术的发展,光束参数检测将面临更高维度、更快响应的技术挑战。建议行业加大以下投入:首先,开发基于人工智能的光束特性预测模型,实现检测-控制闭环优化;其次,建立覆盖可见光到太赫兹波段的宽谱检测能力;最后,推动制定适用于柔性电子制造等新场景的检测标准体系。只有持续创新检测方法学,才能为光子产业的迭代升级提供坚实的技术基石。
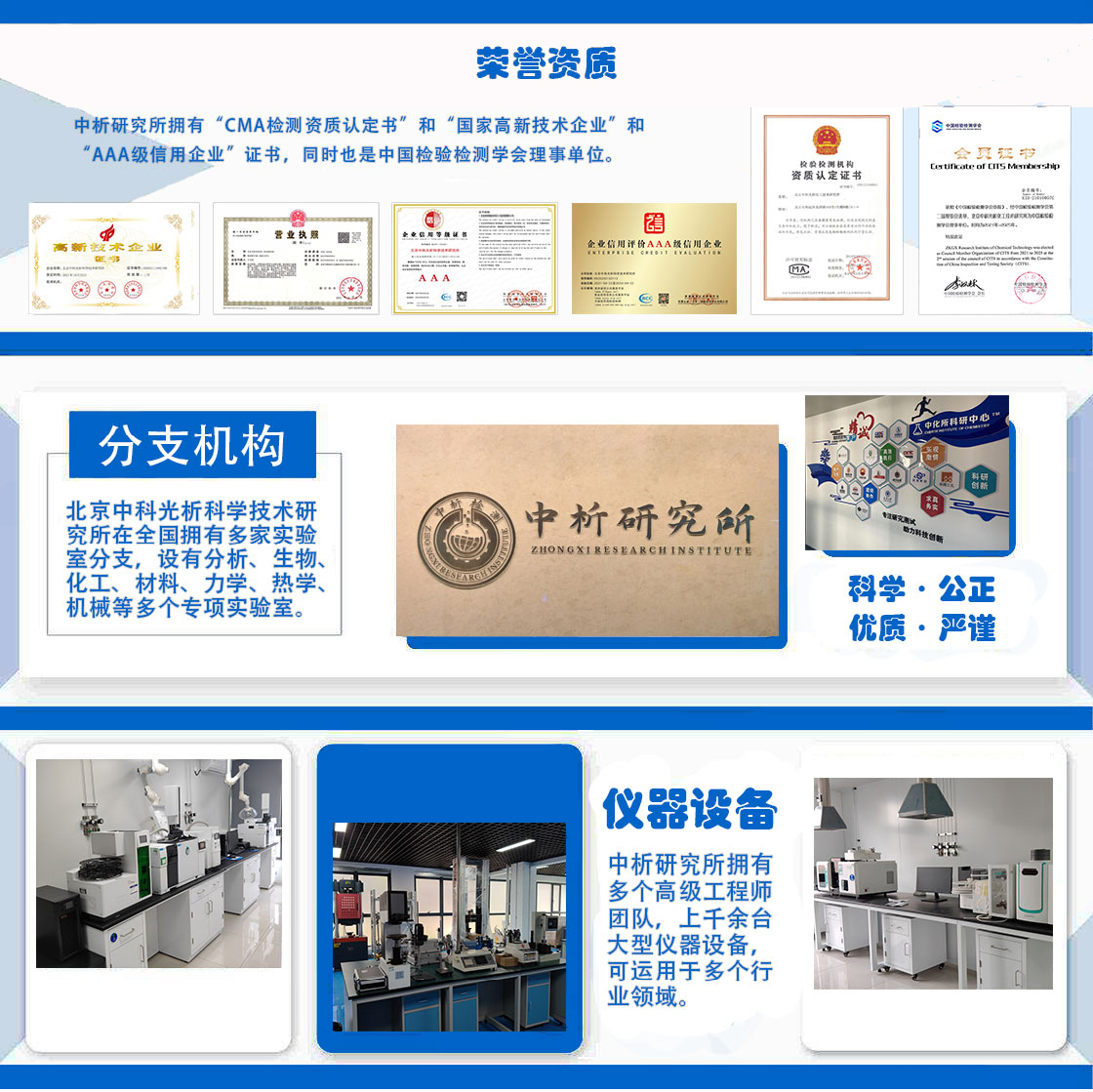
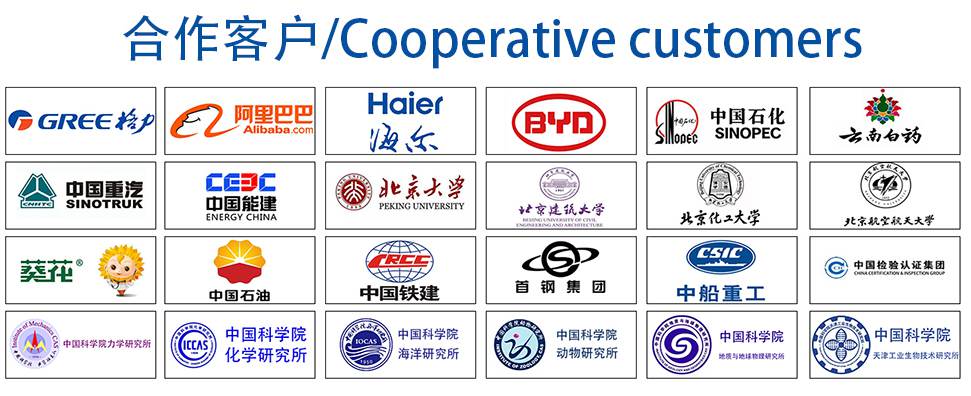