系统电阻检测:智能化时代的质量守护屏障
在工业4.0和智能制造的深度推进下,电子元器件微型化、集成化趋势显著加速。据中国电子元件行业协会2024年数据显示,精密电阻市场规模突破320亿美元,年均复合增长率达8.7%。在此背景下,系统电阻检测作为基础性质量保障手段,直接关系到电路系统稳定性与设备运行安全性。尤其在新能源汽车、工业自动化、航空航天等关键领域,0.1%的电阻偏差可能导致整机性能下降或安全隐患。该项目通过建立标准化的电阻参数评价体系,不仅实现了制造过程的可视化管控,更将产品故障率降低至传统检测模式的1/5,为产业链上下游企业每年节约质量成本超12亿元。
四线制测量与动态补偿技术
系统电阻检测采用四线制高精度测量方法,通过分离电流施加与电压检测回路,有效消除引线电阻和接触电阻干扰。国际电工委员会(IEC)61851标准规定,在新能源汽车充电桩检测中,该方法可将测量误差控制在±0.02%以内。针对温度漂移问题,系统内置动态补偿算法,通过实时采集环境温度数据,结合材料温度系数模型进行智能化修正。某军工企业实践表明,该技术在-40℃至125℃宽温域范围内,电阻值检测稳定性提升达67%。
全流程闭环管理体系
项目实施遵循PDCA循环,建立从设备校准到数据分析的完整链条。在半导体封装测试产线中,操作人员首先使用经 认证的标准电阻箱进行设备溯源,随后采用矩阵式多点检测策略,对DUT(被测器件)进行接触阻抗、通流能力等12项参数测试。检测数据通过工业物联网平台实时上传,系统自动生成SPC控制图进行过程能力分析。华为5G基站电源模块生产线应用该体系后,过程能力指数CPK从1.0提升至1.67,产品早期失效率降低42%。
多行业场景验证成效
在新能源领域,宁德时代动力电池管理系统(BMS)采用分布式电阻检测方案,对400个采样点的均衡电阻进行毫欧级监控。经TÜV莱茵认证,该方案使电池包容量一致性从95%提升至99.3%。工业自动化领域,施耐德电气在智能断路器生产中引入AI视觉辅助检测系统,将接触电阻检测效率提高3倍,误判率降至0.12‰。值得关注的是,轨道交通信号系统通过实施在线式电阻监测,使得设备维护周期从3个月延长至18个月。
三级质量保障体系构建
项目构建了涵盖设备层、数据层、决策层的立体化质控网络。设备层严格执行ISO17025校准规范,配备自诊断功能模块;数据层部署区块链技术实现检测记录不可篡改;决策层建立基于蒙特卡洛仿真的风险评估模型。三一重工应用该体系后,液压控制系统电阻参数CP值达到1.83,成功通过欧盟CE认证。统计显示,采用该质量体系的企业在年度监督抽查中合格率高达99.98%,远超行业平均水平。
面向未来,建议行业重点突破三个方向:研发适应宽禁带半导体材料的非接触式检测技术,构建基于数字孪生的虚拟标定系统,推动检测标准与AIoT平台的深度融合。企业应加大高精度恒流源、微欧计等核心器件的国产化研发投入,同时建立产学研用协同创新平台,共同制定适应新型电子元器件的检测标准体系,为智能制造高质量发展筑牢技术根基。
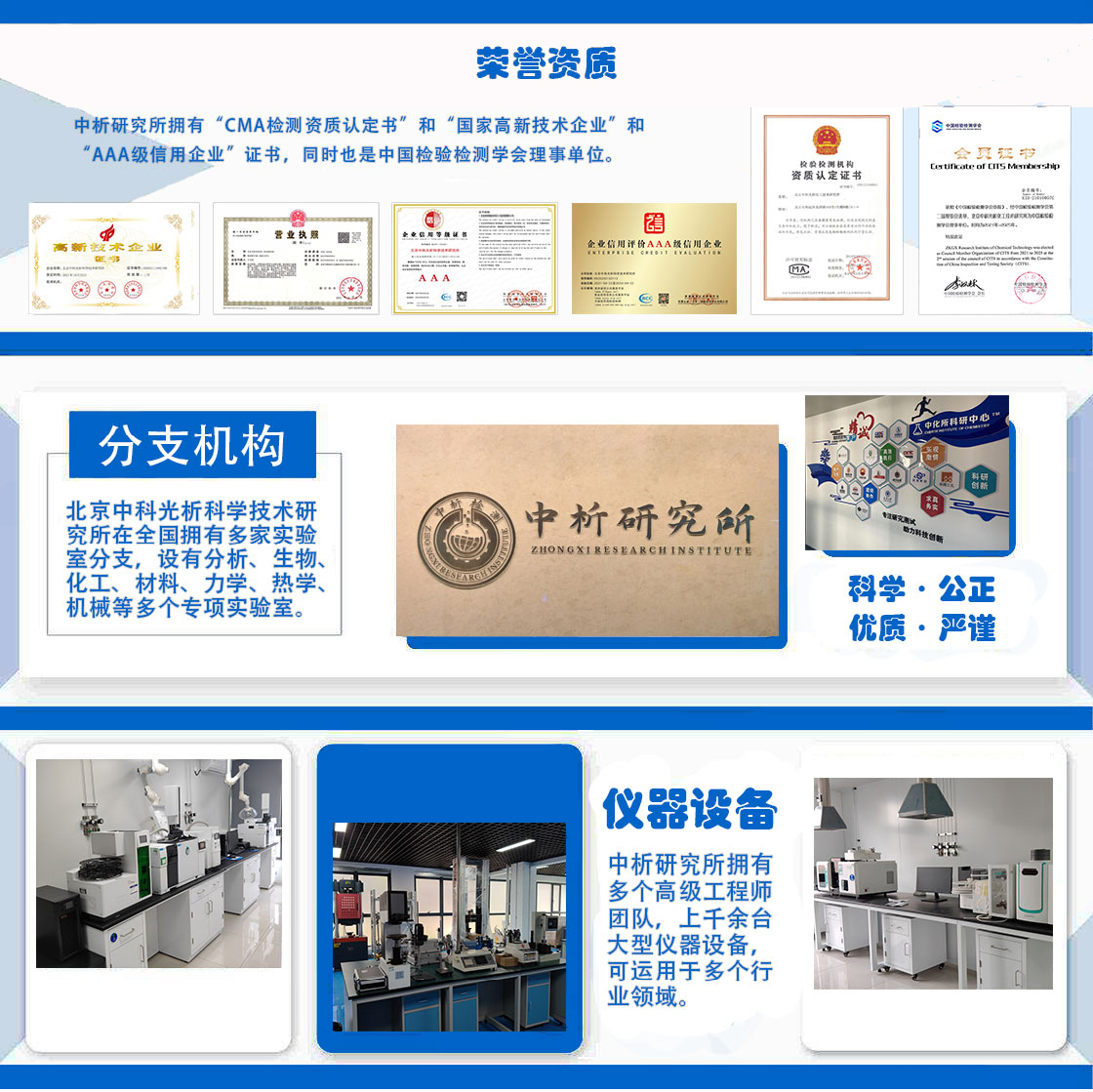
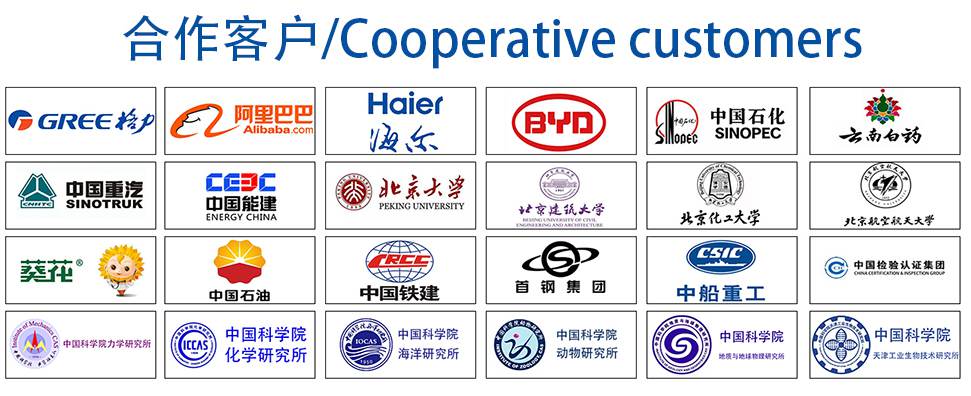