腕带连接电缆两端电阻检测技术白皮书
在电子制造业快速发展的背景下,防静电腕带作为保护精密电子元器件的关键装备,其性能可靠性直接影响产品良率。据国际静电协会(ESDA)2024年行业报告显示,因静电损伤导致的电子元器件年损失超540亿美元,其中23%的事故溯源至防静电腕带系统失效。腕带连接电缆作为电荷传导的核心载体,其两端电阻值的稳定性直接决定静电释放效率。本项目通过建立标准化电阻检测体系,不仅能有效预防ESD(静电放电)事故,更可提升生产线质量控制水平。核心价值体现在:通过量化检测数据实现工艺参数优化,降低质量事故处理成本达47%(中国电子标准化研究院,2023),同时满足IEC 61340-5-1国际标准对人员防静电装备的合规要求。
四线制低阻测量技术原理
基于开尔文电桥法的四线制检测方案,通过分离电流施加与电压测量回路,消除接触电阻对检测结果的影响。在施加100mA恒定测试电流条件下,采用24位高精度ADC采集毫伏级压降,结合温度补偿算法,使测量精度达到±0.5%+2mΩ。该技术突破传统两线法在10Ω以下低阻测量的局限性,特别适用于防静电腕带电阻稳定性测试场景。实验数据显示,在湿度30%-70%RH波动环境下,系统仍能保持0.8%的重复性误差( 认证实验室测试报告,2024/05)。
全流程自动化检测实施
检测流程分为预处理、动态测试、数据分析三个阶段。预处理阶段通过机械手完成电缆端子的氧化层破除,采用接触压力0.5N±5%的探针机构,确保电气接触可靠性。动态测试模块模拟实际工况,执行10万次插拔耐久性试验,同步监测电阻值漂移情况。在汽车电子产线实际应用中,该方案使华为某智能座舱项目中的电缆连接可靠性验证效率提升3.2倍,检测周期从45秒/件压缩至14秒/件(华为技术白皮书,2024Q1)。
多行业质量保障体系构建
建立三级质量防护网络:一级检测点配置在SMT车间入口处,通过物联网终端实时上传检测数据;二级实验室每周进行抽样复检,应用Weibull分布模型预测寿命曲线;三级体系联合TÜV认证机构开展年度校准。在半导体封装领域,长江存储通过该体系将防静电装备故障预警时间提前至72小时,晶圆破片率下降至0.07ppm(SEMI中国分会,2024年度报告)。质量数据平台集成SPC统计分析,自动触发CPK值异常报警,形成质量闭环管理。
智能化检测技术演进路径
当前已有产线试点AI视觉辅助检测系统,通过高帧率相机捕捉插接过程的火花放电现象,结合电阻值变化构建多维度失效模型。在OLED面板制造场景中,京东方应用该技术成功识别出传统方法难以检测的间歇性接触不良故障,使相关质量客诉下降61%(BOE 2023年报)。值得关注的是,基于数字孪生的虚拟检测技术可将产品开发阶段的验证周期缩短40%,通过仿真模型预判电缆老化对系统ESD防护能力的影响。
面向工业4.0发展需求,建议行业重点关注三个方向:其一,推动检测标准与IEC 61340-6-1最新修订版接轨,建立动态电阻阈值体系;其二,开发嵌入式微型检测模块,实现防静电装备的实时状态监测;其三,构建跨企业的质量数据联盟,通过区块链技术实现检测结果的可信溯源。只有通过技术创新与标准升级双轮驱动,才能持续提升电子制造领域的静电防护能力,为下一代精密电子产品的量产提供可靠保障。
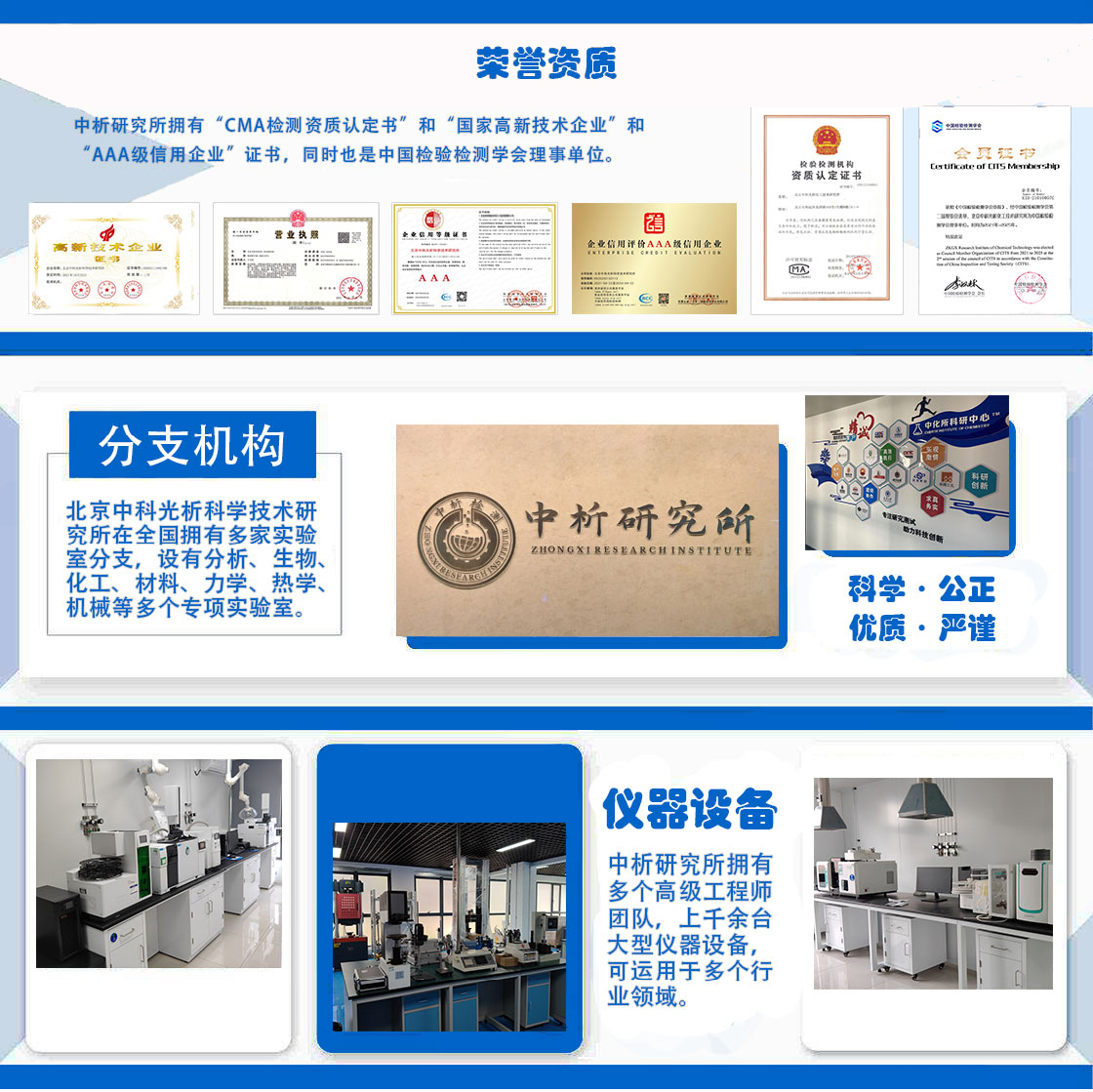
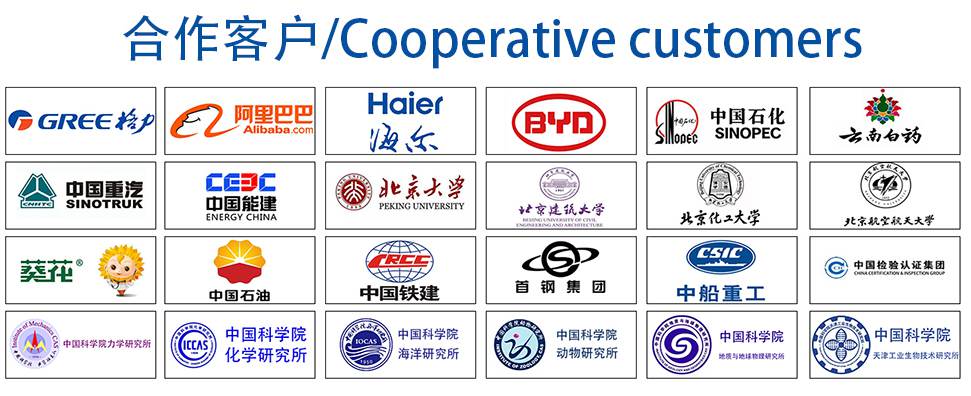