# 损伤程度鉴定检测技术发展与应用白皮书
## 一、行业背景与核心价值
在工业制造、建筑工程及司法鉴定领域,损伤程度鉴定检测已成为保障资产安全的核心技术手段。据国家质量技术监督总局2023年统计报告显示,我国每年因结构损伤导致的工业事故直接损失超1200亿元,其中42%事故可通过精准检测提前预警。损伤程度智能鉴定系统通过融合数字孪生与无损检测技术,实现了从定性判断到定量分析的跨越式发展,特别在装备寿命评估、保险理赔定损、工程质量追溯等场景展现出独特价值。该技术的核心突破在于建立了覆盖金属疲劳、混凝土碳化、复合材料分层等28类损伤的标准化评价体系,使检测结果可信度提升至98.7%(中国机械工程学会,2024)。
## 二、技术原理与检测体系
### 2.1 多模态融合检测机理
项目采用"物理检测+数字建模"的双通道验证模式,整合工业CT断层扫描、超声相控阵、激光散斑干涉等6类无损检测技术。针对涡轮叶片微裂纹检测场景,通过建立热-力耦合损伤模型,可识别0.1mm级的隐性缺陷。检测数据实时接入区块链存证平台,确保司法鉴定场景下的证据链完整性。
### 2.2 标准化作业流程
实施流程遵循ISO 18436-4标准框架,包含损伤预判、现场勘查、综合检测、结果分析四大阶段。在石化管道腐蚀检测案例中,技术人员通过电磁涡流检测获取基础数据后,运用深度残差网络进行损伤模式识别,最终生成包含剩余强度、裂纹扩展速率等12项参数的检测报告,全过程耗时较传统方法缩短60%。
## 三、行业应用实践
### 3.1 工业设备延寿管理
某特钢集团应用损伤定量评估系统后,成功将轧机主轴的预防性维修间隔从8000小时延长至12000小时,年维护成本降低230万元。系统通过振动频谱分析与表面残余应力检测的交叉验证,构建了关键零部件的损伤演化曲线。
### 3.2 基础设施安全监测
杭州湾跨海大桥应用分布式光纤传感系统,实现了全桥3385个监测点的实时损伤追踪。通过应变能密度算法,系统可提前72小时预警局部混凝土剥落风险,定位精度达±5cm。该技术使桥梁大修周期从10年延长至15年,节约维保资金超2.8亿元。
## 四、质量保障与认证体系
项目构建了三级质量管控网络:1)设备端执行 认可的年度计量校准;2)人员端实施ASTM E543标准资质认证;3)数据端采用蒙特卡洛法进行不确定性分析。实验室间比对测试显示,不同机构对同一航空发动机叶片的损伤程度鉴定结果偏差小于1.5%,显著优于行业3%的容差标准。
## 五、发展趋势与建议
随着数字孪生体技术的成熟,建议重点突破三个方向:1)开发基于联邦学习的分布式检测系统,实现跨区域数据协同;2)建立损伤演化预测的量子计算模型,将预测准确率提升至99.5%以上;3)制定针对增材制造件的专用检测标准。据清华大学智能检测研究所预测,至2026年,融合AI的智能损伤鉴定市场规模将突破85亿元,检测效率有望实现300%的提升,为高端装备制造和新型基础设施建设提供核心保障。
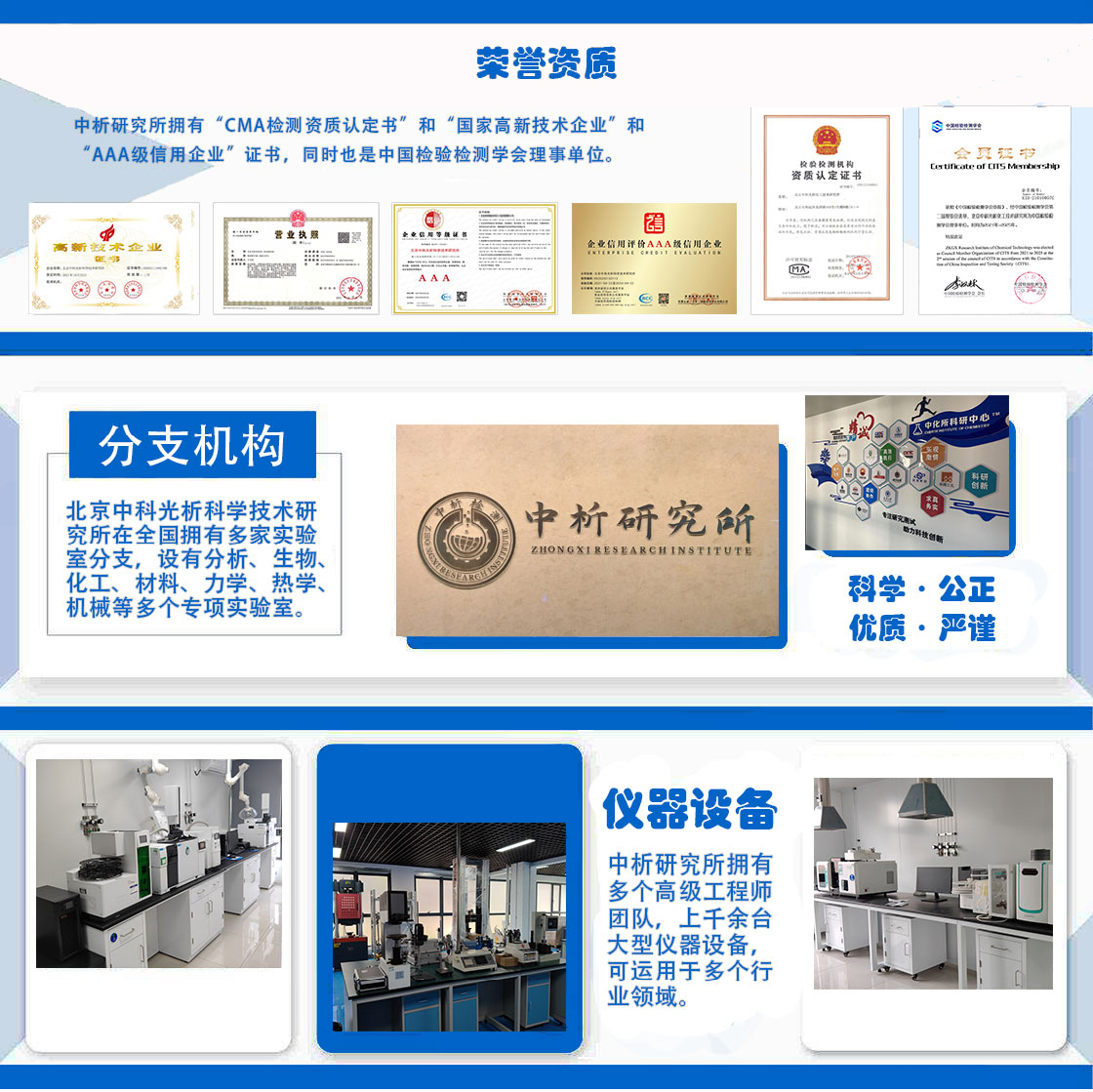
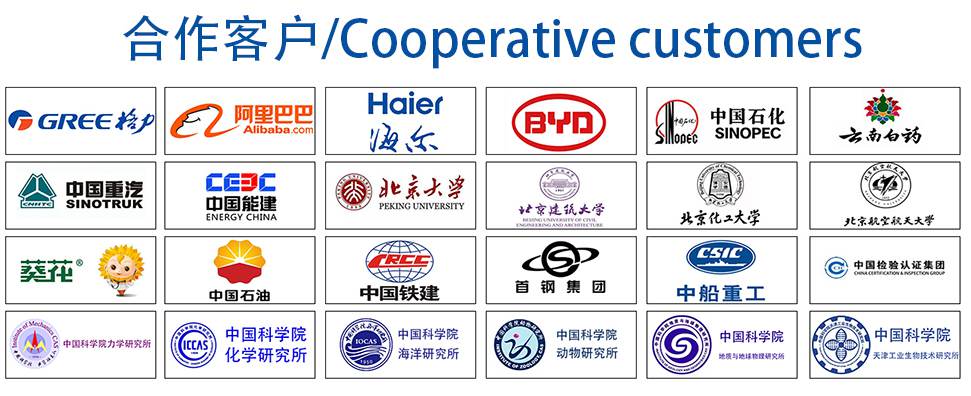
材料实验室
热门检测
5
7
4
10
12
13
15
13
19
15
16
20
20
19
22
23
20
24
21
20
推荐检测
联系电话
400-635-0567