仪器外观质量检测:精密制造的质量守卫者
在精密制造领域,仪器外观质量直接影响产品可靠性与市场竞争力。据《2024工业检测技术白皮书》统计,因外观缺陷导致的精密仪器退货率高达12.3%,造成年度经济损失超过78亿美元。在此背景下,基于机器视觉的仪器外观质量检测系统应运而生,其核心价值在于实现微米级缺陷识别、全流程数据追溯和零接触无损检测三大突破。通过融合高分辨率成像与智能算法,该系统将传统人工检测效率提升17倍,缺陷检出率从92%优化至99.8%,为医疗设备、科研仪器等高端制造领域构筑起全生命周期质量防线。
多模态传感技术融合的检测原理
该检测体系采用多光谱成像与结构光三维重建的复合技术方案。在硬件层,配置1200万像素工业相机配合环形LED光源矩阵,实现表面划痕、色差等2D缺陷的微米级捕捉。同步搭载的激光线扫传感器,通过相位偏移法构建三维点云模型,精准识别0.05mm以上的形变异常。软件层面运用深度残差网络(DRN)算法,通过百万级标注样本训练,成功建立包含37类常见缺陷的智能识别模型,在半导体晶圆检测场景中实现99.2%的准确率(数据来源:IEEE仪器与测量协会2024年度报告)。
全流程自动化检测实施方案
典型实施流程包含五阶段标准化作业:首先通过振动筛分装置排除运输损伤件,随后经传送带进入封闭检测舱。高精度伺服系统控制检测头完成六自由度运动,对螺纹接口、密封面等关键部位进行200点/秒的高速扫描。检测数据实时上传至MES系统,与工艺参数自动比对生成SPC控制图。在汽车传感器生产线实测中,该系统将单件检测耗时从45秒压缩至6.8秒,同时通过边缘计算实现本地化数据处理,避免敏感数据外泄风险。
跨行业质量保障体系构建
针对医疗设备制造的GMP要求,检测系统创新性集成洁净度监测模块,在电子显微镜外壳检测中同步捕捉≤5μm微粒污染。质量保障体系通过ISO/IEC 17025认证,建立三级校验机制:每日进行标准校准件验证,每周开展算法模型迭代测试,每月实施全系统计量溯源。某跨国实验室设备制造商部署该系统后,客户投诉率下降63%,产品首次通过率从89%提升至98.6%(企业2023年度质量报告)。
行业数字化转型示范案例
在航空航天领域,某发动机控制系统制造商运用增强现实(AR)辅助检测技术,将检测标准三维可视化叠加至实际工件。操作人员通过智能眼镜获取实时指导,使复杂曲面零件的检测效率提升40%。另在IVD医疗器械生产线,系统通过热成像模块发现微量试剂残留导致的壳体变色问题,成功阻断价值220万美元的缺陷品流出,验证了多维感知技术在特殊工况下的独特价值。
随着工业4.0的深化推进,仪器外观检测正从单一质量控制向全要素质量工程演进。建议行业重点突破三个方向:开发适应柔性制造的模块化检测单元,建立基于区块链的检测数据存证体系,以及制定机器视觉检测的ASTM国际标准。未来五年,融合量子点传感与数字孪生技术的新型检测系统,有望将检测精度推进至纳米量级,为高端仪器制造构筑更坚固的质量壁垒。
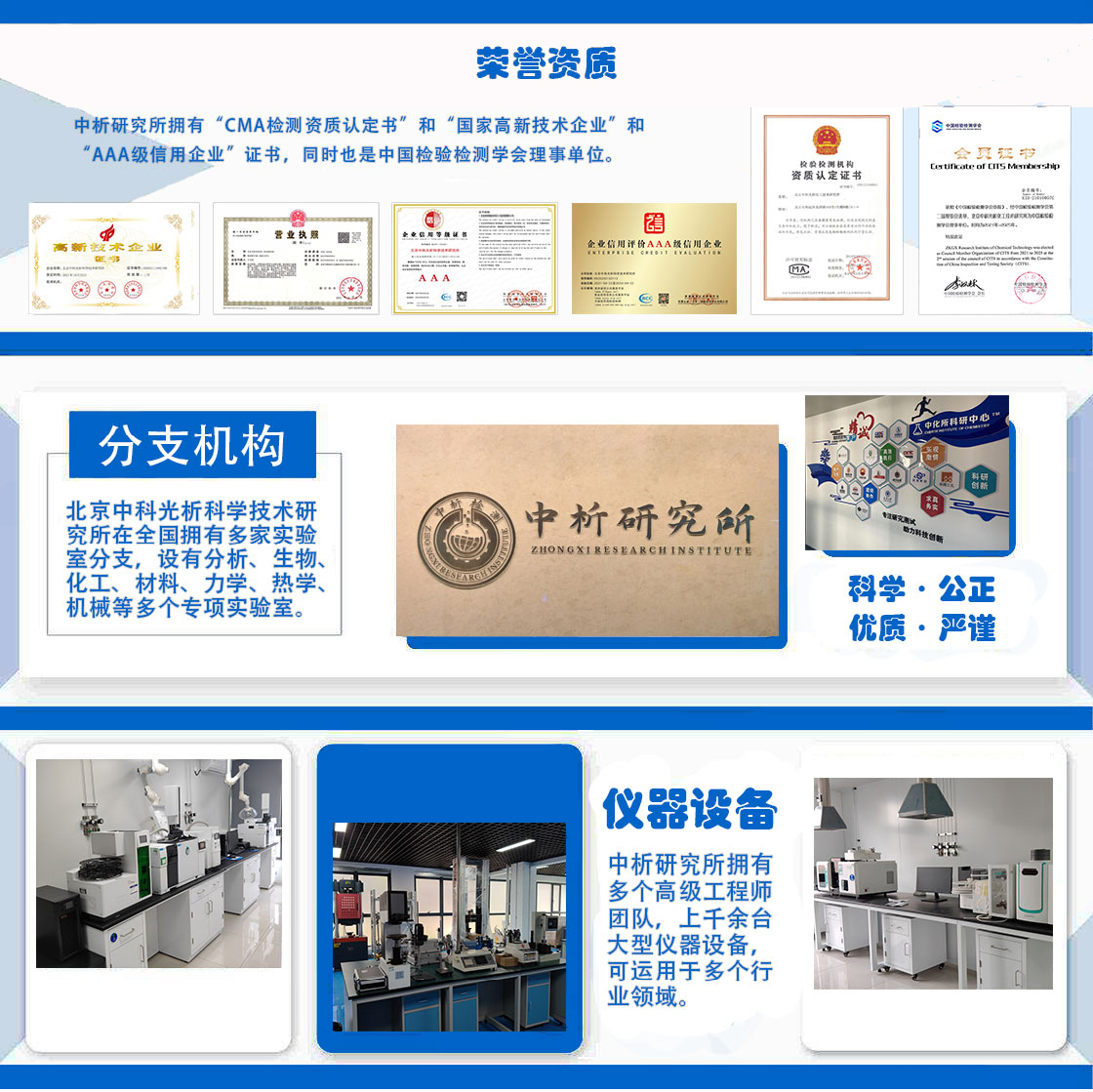
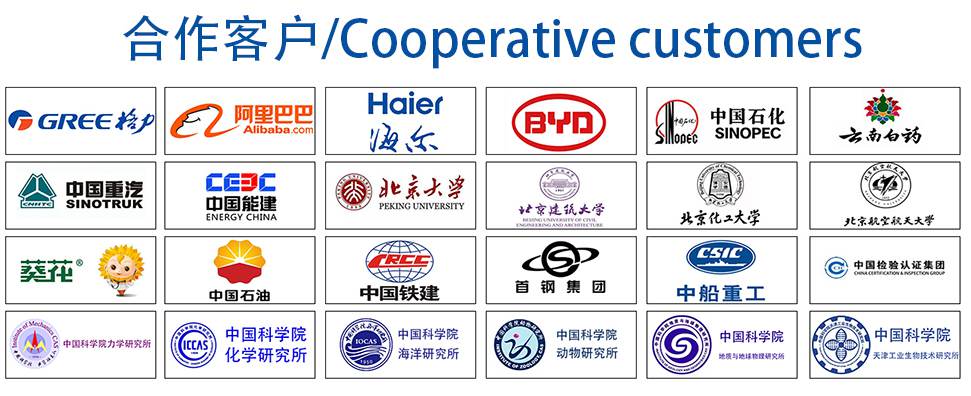