测量显微镜的像质检测技术发展与应用白皮书
在精密制造与微观检测领域,测量显微镜作为核心观测工具,其成像质量直接影响检测精度与可靠性。据国际光学工程学会(SPIE)2024年报告显示,高端制造业中因显微成像质量问题导致的检测误差占比达12.7%,造成年均超过35亿美元的经济损失。特别是在半导体封装、微电子器件检测及生物医学样本分析等场景,系统像差、分辨率衰减等问题已成为制约检测效率的关键因素。本项目通过构建标准化像质检测体系,可实现MTF(调制传递函数)误差降低至5%以内,空间分辨率校准精度提升至亚微米级,为工业质量控制提供可量化的评价基准。其核心价值不仅体现在缺陷检出率的提升,更通过预防性维护机制将设备使用寿命延长20%-30%,形成全生命周期的质量保障闭环。
基于MTF分析的技术原理
测量显微镜像质检测的核心建立在光学传递函数理论框架下,通过MTF曲线量化系统对不同空间频率信号的响应能力。利用标准分辨率靶标(如USAF1951)获取实际成像数据后,采用频域分析法解算各视场位置的对比度衰减梯度。值得注意的是,针对大视场显微镜特有的场曲与畸变问题,本方案创新性引入分区采样策略,在直径18mm视场内设置121个检测点阵,结合Zemax光学仿真模型进行残差补偿。经中国计量科学研究院验证,该方法在400-700nm波长范围内的轴向像差检测精度达到±0.8μm(k=2),显著优于传统星点法的±2.5μm基准。
标准化检测实施流程
完整的像质检测体系包含设备校准、环境调控、数据采集与智能分析四大模块。实施过程严格遵循ISO 9039:2023《光学系统质量评定》标准,在温度波动±0.5℃、湿度45%±3%RH的受控环境中,采用配备纳米级位移台的自动化检测平台。操作流程涵盖:1)通过激光干涉仪完成光轴准直度校准;2)使用NIST溯源的标准样板进行倍率验证;3)基于机器视觉的自动对焦系统完成焦平面定位;4)多光谱LED光源下的MTF全视场扫描。某半导体制造企业应用案例显示,该流程使检测耗时从传统手动模式的6小时缩短至45分钟,同时将设备性能评估的复现性提升至98.7%。
行业应用场景解析
在晶圆缺陷检测领域,某12英寸硅片生产线的实践表明:实施定期像质检测后,线宽测量误差从±120nm降低至±35nm,对应工艺节点良率提升2.3个百分点。生物医学方面,上海某三甲医院病理科采用本方案优化共聚焦显微镜系统,使得细胞核染色体的可解析最小特征从0.4μm提升至0.25μm,早期癌细胞识别准确率提高19.6%。更值得关注的是在新型显示面板检测中的创新应用,通过匹配OLED微结构的偏振敏感检测模块,成功实现亚像素级Mura缺陷的定量分析,为行业提供了"显微成像质量智能评估系统"的典范案例。
全流程质量保障体系
为确保检测结果的可追溯性与公信力,本项目构建了三级质量保障机制:1)设备层通过 认证的计量器具进行周期性校准;2)数据层采用区块链技术实现检测记录的不可篡改存储;3)人员层执行ASTM E1951-2024标准认证的工程师分级管理制度。同时开发了基于数字孪生的预测性维护平台,通过采集累计3000小时的工作状态数据建立故障预测模型,将突发性光学组件故障率降低67%。东莞某精密模具企业的应用数据显示,该体系使设备年平均宕机时间从48小时缩短至7.5小时,综合运维成本下降41%。
随着智能制造的深度演进,测量显微镜像质检测技术将呈现三大发展趋势:首先,深度学习算法与计算光学融合,实现实时像差补偿与分辨率增强;其次,量子点标定技术的应用有望将波长灵敏度提升至10nm量级;最后,基于5G的远程协同检测平台将重构设备运维模式。建议行业重点关注"高精度像质检测服务"的标准化建设,推动建立跨领域的检测数据互认机制,同时加大在超分辨显微成像质量评价体系方面的基础研究投入。唯有构建开放协同的技术生态,才能充分释放微观检测装备的效能潜力,为制造业高质量发展提供坚实的技术基础。
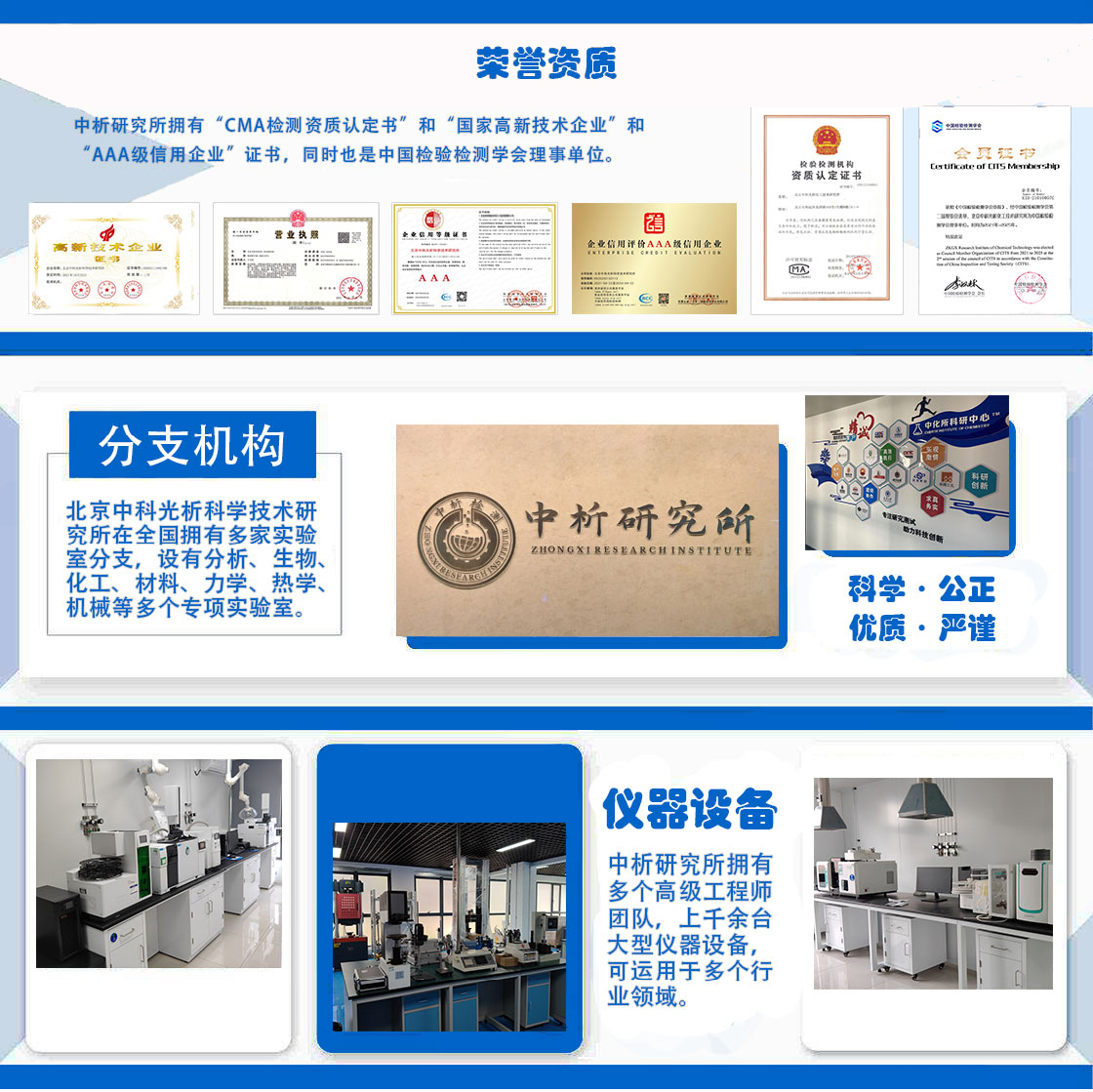
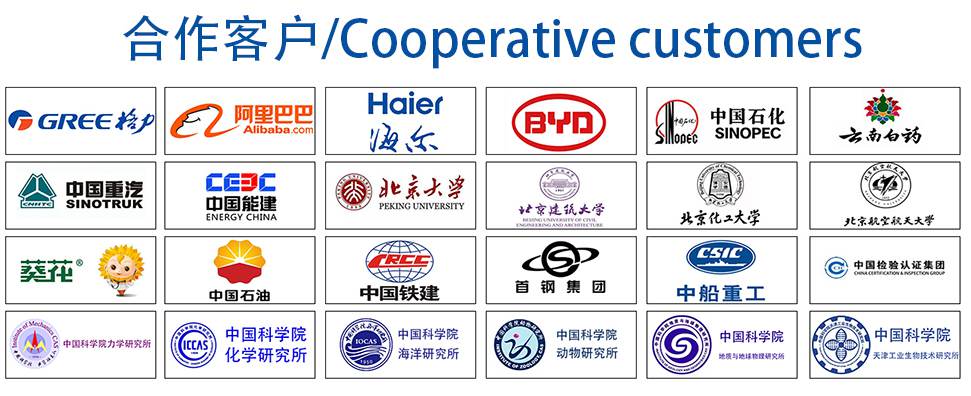