表面耐磨性能检测在齐全制造领域的应用与发展
在高端装备制造和消费电子产业快速迭代的背景下,材料表面性能已成为决定产品市场竞争力的关键指标。据弗若斯特沙利文2024年行业报告显示,精密制造领域因表面磨损导致的年经济损失超过380亿美元。表面耐磨性能检测通过量化评估材料抗摩擦损耗能力,为产品设计验证、制造工艺优化提供科学依据,已成为新能源汽车内饰、智能穿戴设备、航空航天涂层等领域的强制性质量管控环节。该检测体系不仅可降低产品早期失效风险,更通过建立材料性能数据库推动行业标准化进程,其核心价值体现在全生命周期质量管控和研发效率提升两大维度。
检测技术原理与方法体系
基于ASTM D4060和ISO 5470标准建立的表面耐磨性能检测系统,采用Taber线性磨耗试验法和往复式摩擦测试双维度评价体系。前者通过标准磨轮在特定压力下进行旋转摩擦,后者模拟真实工况下的动态接触过程。据中国机械工程学会2024年技术白皮书披露,新型光栅位移传感技术的应用使磨损深度测量精度达到±0.1μm,较传统方法提升5倍。在新能源汽车内饰件检测中,系统可准确捕捉聚氨酯材料经过2000次循环测试后的表面形貌变化,为耐刮擦性能分级提供量化依据。
智能化检测实施流程
现代化检测流程涵盖预处理、过程监控、数据分析三个阶段。检测前需在恒温恒湿环境中进行48小时状态调节,确保材料性能稳定。检测过程中,集成式环境模拟舱可复现-40℃至120℃极端工况,搭配机器视觉系统实时捕捉表面微观裂纹。典型应用案例显示,某品牌智能手表采用石墨烯复合表带经5000次摩擦测试后,通过磨耗试验数据智能分析平台自动生成ASTM等级报告,检测效率提升70%的同时降低人工判读误差。
跨行业应用实践分析
在轨道交通领域,DIN 53109标准下的耐磨检测系统成功应用于高铁座椅蒙皮选型,使材料更换周期从18个月延长至30个月。消费电子行业应用案例表明,采用新型纳米涂层的手机屏幕经10000次钢丝绒测试后,透光率仅下降2.3%(参照DisplayMate实验室2024年测试数据)。值得关注的是,建筑材料检测中发展的三维磨损建模技术,可精准预测大理石地砖在商场人流通行10年后的表面凹陷分布,为维护方案制定提供数据支撑。
质量保障与标准化建设
依据 -CL01:2018构建的四级质量管控体系,涵盖设备计量溯源、人员资质认证、过程受控管理、数据复核机制等关键节点。国际比对试验显示,采用ISO/IEC 17025体系认证的实验室,其耐磨测试数据离散度控制在5%以内(ILAC 2024年能力验证报告)。某跨国汽车零部件企业通过部署区块链技术的检测数据管理系统,实现8个检测中心测试结果的实时互认,供应链质量审核周期缩短40%。
展望未来,建议行业从三方面深化发展:建立涵盖摩擦系数、表面能、微观硬度等多参数的综合评价体系;推动基于机器学习的磨损寿命预测模型在检测前端的应用;加强产学研合作开发适用于柔性电子、超疏水涂层等新兴材料的专用检测方法。随着数字孪生技术在检测领域的渗透,表面耐磨性能评估将逐步实现从实验室到实际工况的无缝衔接,为齐全制造向"零缺陷"目标迈进提供关键技术支撑。
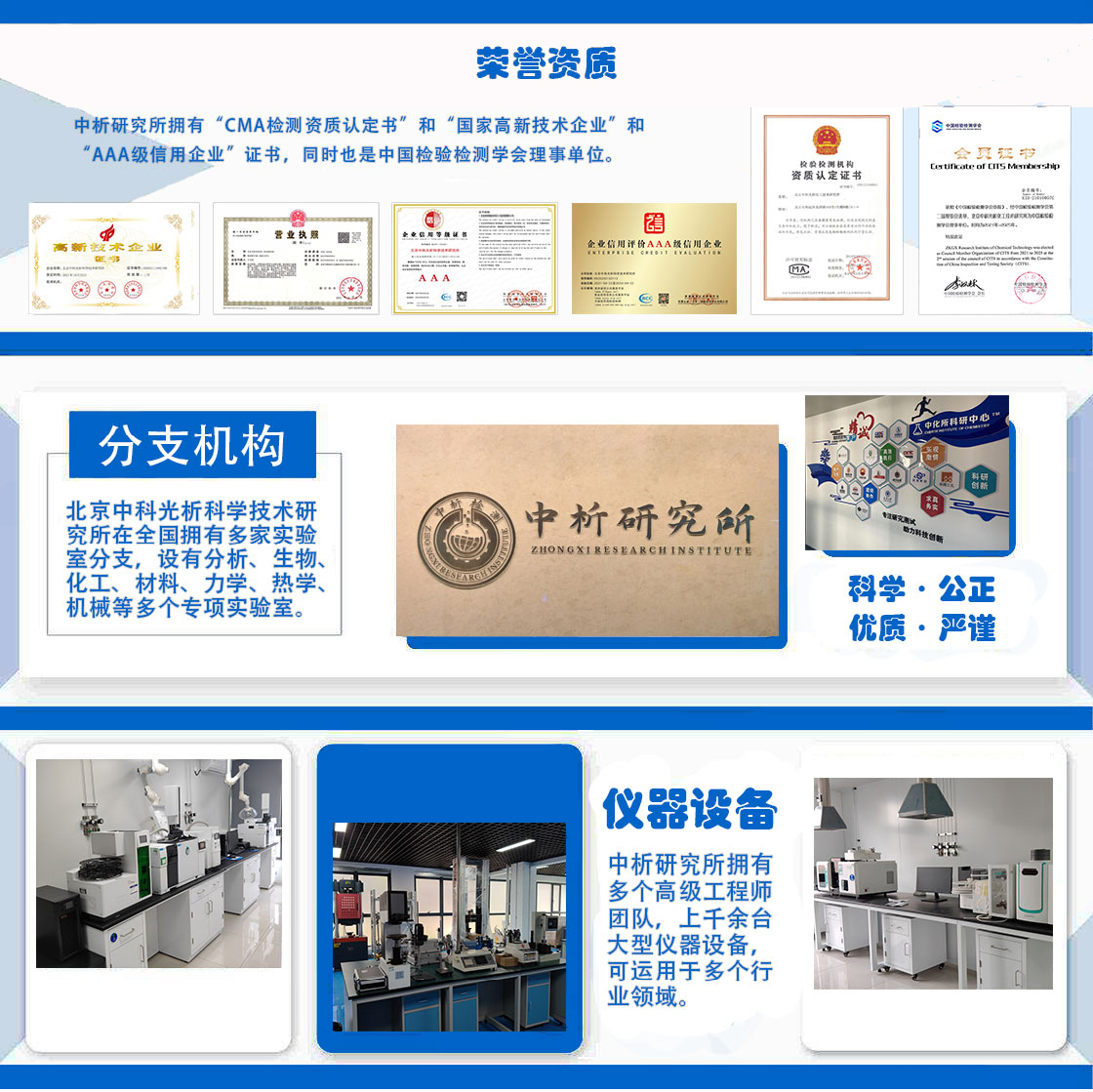
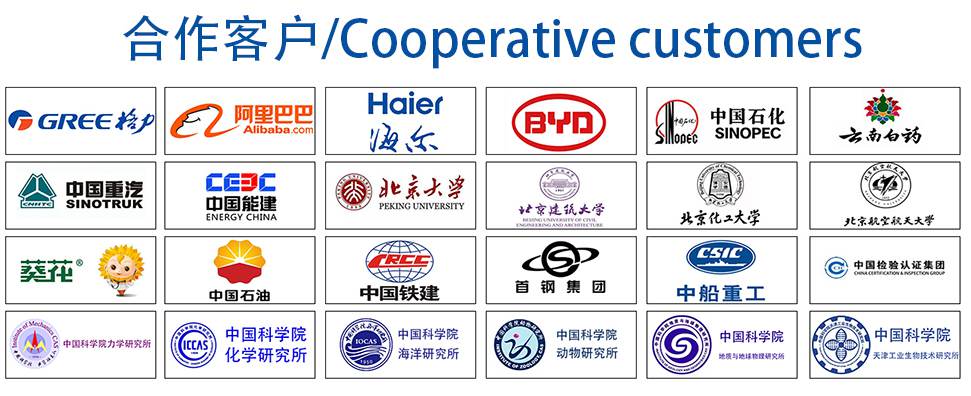